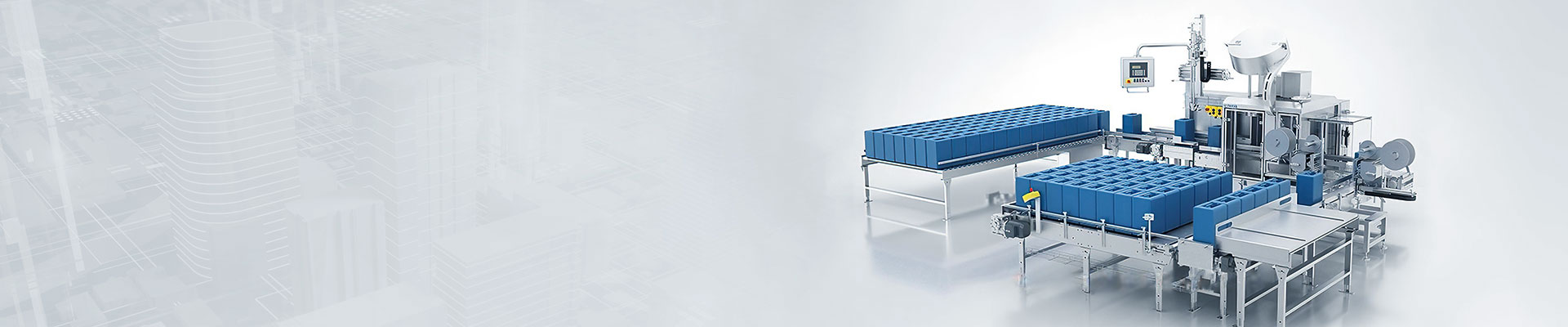
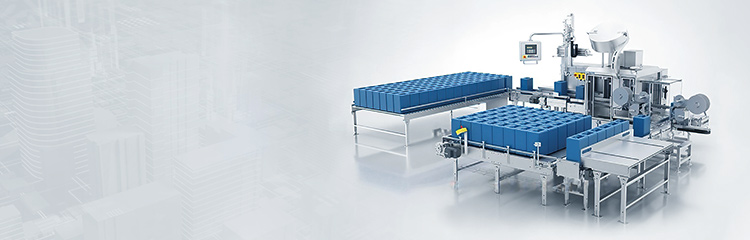

称量灌装机采用净重、毛重二种电子秤灌装模式选择,满足用户不同的灌装需求。通过压力称量模块进行重量的拾取,并将拾取的重量信号进行放大、滤波后,进入A/D转换器进行模拟量到数字量的转换,然后送入单片机进行信号的分析、处理,其结果通过RS232C通讯串口输出到工业控制,同时根据信号的结果做出相应的反应并执行相应的操作。称重控制系统以SCADA灌装为平台,在此平台上进行灌装功能的二次开发,实现智能灌装过程管理控制。建立服务于自动化过程控制的软件使用计算机识别技术,打印技术,自动控制技术,信息技术,形成智能自动灌装,满足客户对于灌装过程自动化,信息化,智能化的要求。
灌装设备对现场进行数据釆集和控制,灌装设备处于现场控制层,灌装系统实现对现场各类信号进行采集和控制,其主要功能有:与上位机系统通讯,装系统釆集并传递该灌装机的信息;在线连续采集液位、变频器频率等模拟量输入信号;实时采集泵、电磁阀、光电开关、接近开关、电动执行机构等开关量状态信号,并根据运行要求输岀信号控制各种阀通断;再与称量灌装机通讯,使称量灌装装置控制伺服电机实现对罐装容量的精确控制;最终实现对系统的自动控制。
灌装生产线由灌装机、旋盖机、封口机、喷码机组成,整个生产线由传送带贯穿始终,负责容器的运送。灌装机是这条生产线的主要设备,其性能对于整个生产线的功能及效率起到决定性的作用。为了提高灌装机的性能,灌装设计了由的伺服控制系统、步进控制自动灌装机系统、可编程控制器(PLC)、人机界面、传送带变频调速系统、增压气动部分及光电传感器等组成的机、气、电一体化自动控制系统。
液体灌装机采用可编程逻辑控制器作为其控制主体。灌装秤在硬件连接上,PLC作为控制系统中的下位机,与各种底层设备直接联系。PLC灌装系统与上位机通讯、获取产品资料和生产参数,以及依据生产线中各种传感器,控制灌装头的动作逻辑,控制灌装传送带的速度,称重灌装机驱动步进电机控制灌装头的调整,实现二维精确定位及灌装进口挡板的精确定位;依据PLC给岀的自动灌装容积,完成伺服驱动及液体灌装容量的补偿,驱动增压液压缸动作,实现灌装容量的调整,同时通过补偿算法计算出的补偿容积信息,加入到灌装容量的调整中。