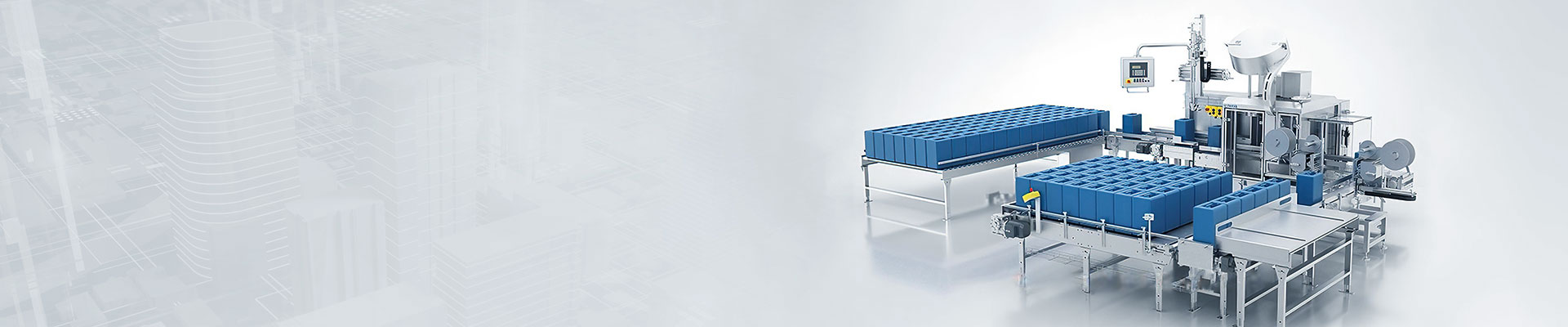
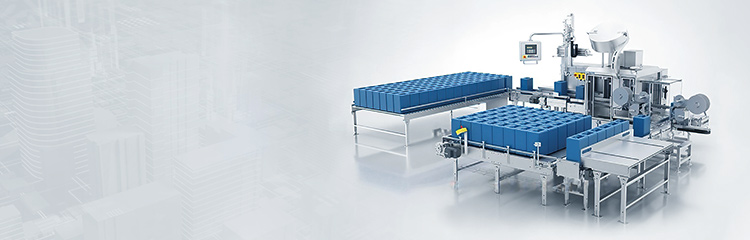

自动配料系统集数据采集、加热参数控制、顺序控制、位置控制、速度控制、带料控制、温度、变频器控制等任务。主要完成初始数据输入、物料跟踪、过程参数设定计算、数据记录和报表、人机对话处理、数据通讯、模拟树脂模型、历史数据处理、应用系统起动、配料监视等任务。投料系统直接与过程控制级服务器相连,是该系统主网,连接控制器、数据存储、实时获取设定,采样以及操作的数据。现场总线和远程I/O的普遍采用实现了以少量通讯电缆代替大量控制电缆的目的。根据搅拌配料工艺特点及设备分布,各功能控制器主要完配料区域逻辑控制、人机对话、数据传输、数据处理及物料跟踪等功能。根据现场经验汇聚配料方案,这个方案是否在配料行业起到借签作用?接下来给介绍配料系统的控制过程,上料系统的各控制分布如下:
(1)加热釜配料区共设6台PLC。称量配料系统数据采用以太网、Profibus-DP网等多种方式进行通讯,主控制器采用以太网的方式与上位机及轧线其他区域进行数据传输。系统向上位机传送数据,反应釜从混配储料罐获取要料信号,变频器向转子泵发送运转信号。系统按指定反应釜依次顺序控制、对出料储料罐进行抽料控制、反应釜以重量到达作为定量控制、同时反馈给转子泵停止向反应釜输送。
(2)混配区共设3台PLC。混配区的任务是把出反应釜输送到计量反应釜配料区。混配区混配不同反应釜搅拌速度按顺序依次控制、配好的液体再进行保温罩控制。
(3)配料区共设3台PLC。成品配料区控制称重精度与反应釜输送密切相关,在配料区采用了称重控制器,即每一台称重配料机设一台称重控制器,内设一个PIIICPU,三个称重模块安装在反应釜底部,来控制该反应釜的出料灌装及包装打包等。
(4)称重分选区共设5台PLC。以称重灌装完成后经过动力滚筒输出辊道速度控制、速度控制与自动跳步控制、包装后的重量检测灌装合格范围,不合格的灌装重量分别为欠重和超重的管理分段输送及管理。
(5)混配区配料区分选区CPU板集成以太网口,支持10/100M通讯,大大提高通讯能力。数据在中控室集中管理。
(6)基于VME总线的开放式结构,总线控制器结构和广泛的第三方的基于VME的CPU板及I/O模块。在同样的机架里支持现有的90-70I/O和新的I/O。
(7)Windows环境下的集成开发工程环境CimplicityME为PACSystems™RX7i系列的所有编程、配置和诊断提供了广义的工程开发环境。除I/O点外,可以直接使用变量名编程而无须关心其地址分配,使得设计更灵活同时提高了工程设计的效率。
(8)称重配料系统采用开放的VME总线结构,可安装超过300家不同厂商的VME标准模块。在系统配置中,除本身的机架I/O模块外还可通过现场总线(如ProfibusDP)与远程I/O模块相连接,构成一个功能强大、价格合理的控制平台,以满足各种大规模、复杂的高速控制要求。
(9)GE90-30PLC系列成本低、性能高,可以方便取代从简便的继电器到复杂的中型自动化系统应用场合。它的CPU具有强大的功能,如内置PID调节、结构化编程、中断控制、间接寻址及各种功能模块,能顺利完成复杂的操作。另外,90-30系列有功能很强的特殊模块可供选择,如高速计数模块、ProfibusDP通讯模块等。
(10)VersaMax系列PLC提供了广泛的I/O模块,组态更加灵活。通讯模块能将VersaMax与ProfibusDP网(或其它工业现场总线)相连,实现远程控制。