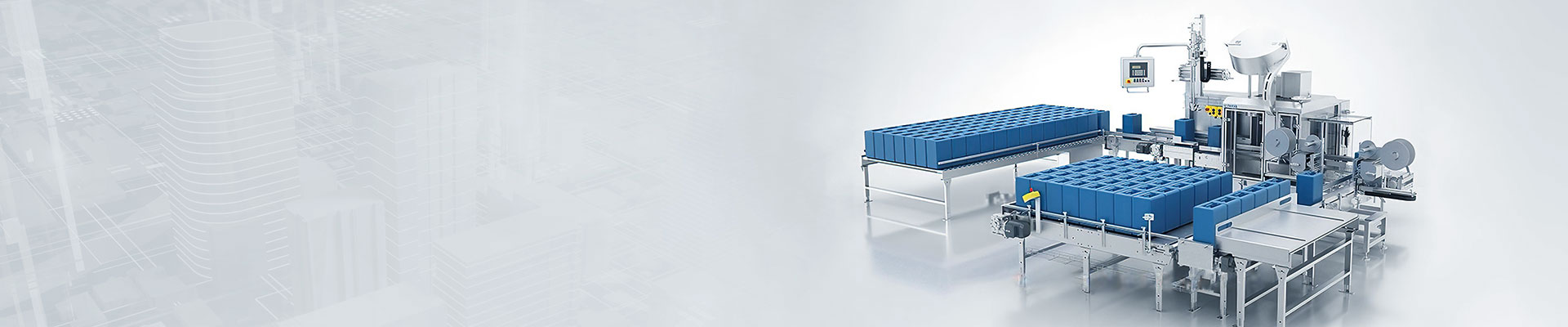
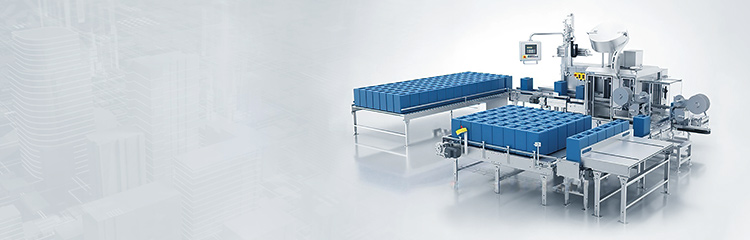
The weighing system of garbage truck is a weighing system product specially developed for online weighing of garbage cans of sanitation garbage trucks, which is suitable for side-mounted compressed and rear-mounted compressed sanitation garbage trucks. The biggest feature of this product is that it can realize weighing in the process of garbage hanging and lifting, and can automatically accumulate the weight of garbage collected and the number of garbage bins.

The Electronic scale of garbage truck is a Weighing system product specially developed for online garbage can weighing of sanitation garbage truck, which is suitable for side-mounted compression type and rear-mounted compression type sanitation garbage truck. The biggest feature of this weighing module is that it can realize weighing in the process of garbage hanging and lifting, and can automatically accumulate the weight of collected garbage and the number of trash cans.
The front camera records the video information of vehicle driving in real time, and the rear camera records the video information of garbage loading and unloading in real time;
It can be customized according to users' needs, and the data can be communicated and docked with customer platforms or equipment.
Data interaction: it can display the operation status information of garbage truck in real time, and make statistical analysis of data according to user's needs; Users can issue management control instructions through the management platform;
Can print vehicle operation information in real time, such as garbage weight, number of trash cans, time, customer name and other information;
Real-time operation management platform and vehicle terminal
Non-inductive weighing, the weighing process does not need to stop, and high-precision weighing is realized in the process of overturning and lifting the trash can;
The weighing sensor dynamically weighs in the whole process, with quick response and fast and efficient weighing;
The weighing accuracy can reach 3%;
Adapt to a variety of trash can specifications, automatically identify large and small barrels and weigh them;
Can obtain a variety of data such as total weight, net weight of garbage, tare weight of trash can, and can be switched freely;
Single/double station independent bucket number accumulation function;
Statistical function of total cumulative weight of garbage collected and transported in a single day;
Can automatically identify the identity information of trash cans and associate it with the weight data of garbage collection and transportation;
Can realize vehicle fuel consumption information management;
Photographing and video monitoring functions of vehicle working process;
4G network remote data communication function;
BD/GPS dual-mode positioning function;