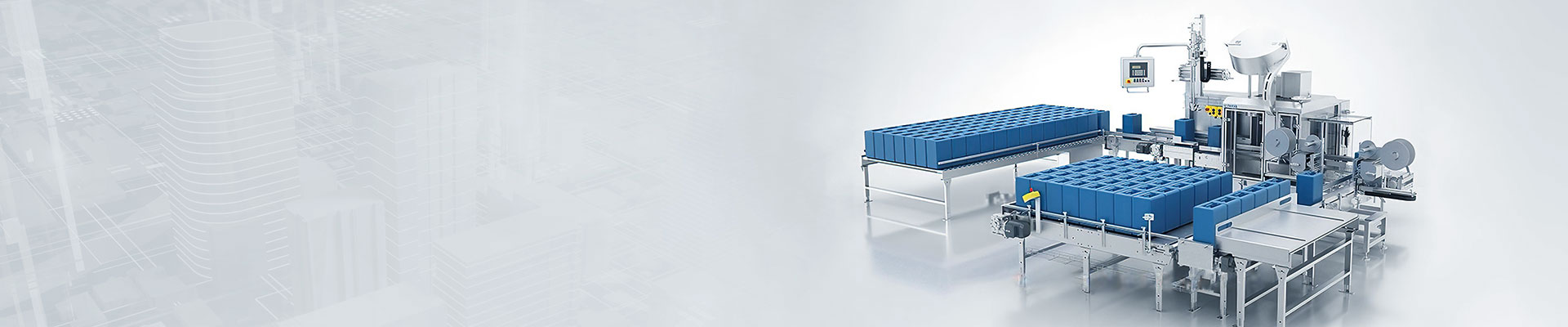
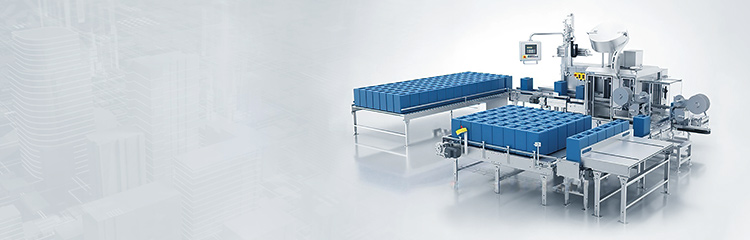
RFID称重系统是一种先进的无线称重技术,RFID称重系统可以让很多管理都实现无线的方法,而且更多的商业企业将陆续实施打码到条项目的工作,为了提高运行的效率,同时也要尽量不改变现在的物流仓储模式,这样就要使用托盘作为载体了,采用托盘标识的方式能让仓储管理起来更加方便。

RFID称重系统采用无线网络和条形码技术,以无线网络与RFID选型的依据,以及管理实施策略,基于自动称重RFID综合管理系统主要由订单管理系统、自动排单系统、生产包装系统、仓库管理子系统以及数据同步和系统集成等模块组成。系统选用NET作为软件开发平台,开发环境分为PC端与RFID采集终端(手持)两部分,其中后者为智能移动设备,使用NET精简版框架实现嵌入式开发。称重系统采用SQLSERVER系列数据库平台,根据实现目标及功能需求设计数据库结构,利用SQLSERVER的复制机制实现分布式数据库,并结合非织造布生产经营实际经验提出RFID数据库的管理及优化策略。
RFID称重系统可以非常细致地分解为:基础信息管理、客户订单管理、生产计划管理、物料需求管理、物料采购入库、物料生产领用出库、自动称重打标签管理、产品检验信息管理、产品RFID仓储物流管理、产品出库RFID管理、产品库存盘点RFID管理、产品销售退货RFID管理。条形码编码规则采用国际物流通用码制ODE128,码编号是此产品的唯一身份编码,例如:0120100423A0001.意为产线(01)、日期(20100423)、班次(A)、生产件数(0001)。其中,班次定义为A早班、B中班、C晚班;件号是自增。如0001代表01线的当天早班第一卷产品。
1产品质量追溯及防伪功能
系统自动记录产品的生产工号、生产日期、生产线、物料批次号等各个环节信息,建立完善的产品档案。如某产品出现问题,只需输入产品唯一身份RFID,系统自动查询此产品的生产工号、生产日期,检验工号、检验日期、入库工号、入库日期、出库工号、出库日期、发货车牌号及使用的原材料批次号等详细信息。由于每个产品都有自己的唯一身份RFID,如果非本厂产品,只需扫描产品RFID,系统自动报警“此产品非本厂产品”。
2用料成本控制
通过每种类型的产品物料清单,将产品生产计划分解成为用料计划,可合理计算原辅材料余量,控制每批产品的原辅材料用量。
3自动统计产量,生产调度灵活
本系统在每批次自动称重时,自动记录操作员、机台号及生产日期,可以很容易地统计员工产量,并能追究产生残次品的相关责任人员。有权限管理人员可以实时查询到整个公司的销售订单,生产计划单、批次等,根据具体情况对生产计划进行合理的调度。
4提前预警功能
订单生产有预警功能,时刻提醒生产部门,某订单定交货日期有多长,防止到期还未生产好的现象发生,提高公司的形象。对外销产品也进行称重,提醒员工有无超出理论重量,每月对超出重量部分进行考核,便于提高员工的工作积极性和认真程度。
由于各个部门信息共享,各个部门都可预先知道本部门工作任务,提前做好准备,如:仓库部门可查询即将完成的产品,提前把库位按克重、颜色或客户进行整理,将已生产好的产品立刻搬入仓库,不会产生乱堆乱放现象。
5提高生产效率
在生产线上,工人只需把产品放在电子秤上,系统自动打印产品身份RFID,并同时记录产品生产信息,确保产品信息的准确性,不需再手工记录信息,提高生产效率,提升公司形象。
6操作方便,减少差错
出库操作采用扫描RFID方式进行理货,并自动打印出库清单,装车时实物与出库清单进行再次核对,防止发错货的现象发生。出入库操作、盘点、移库等操作采用RFID扫描方式,速度快,数据准确。对次品、原辅材料也采用RFID进行管理,能实时查询次品及原辅材料的库存情况。
7信息共享与查询
从产品的销售订单到生产领料、产品称重、入库、出库都采用扫描RFID的方式来操作,保证了数据的实时性与正确性,只要一个地方输入信息,其他相关部门可以共享,保证了数据的一致性,管理层也能有效地进行在线管理。