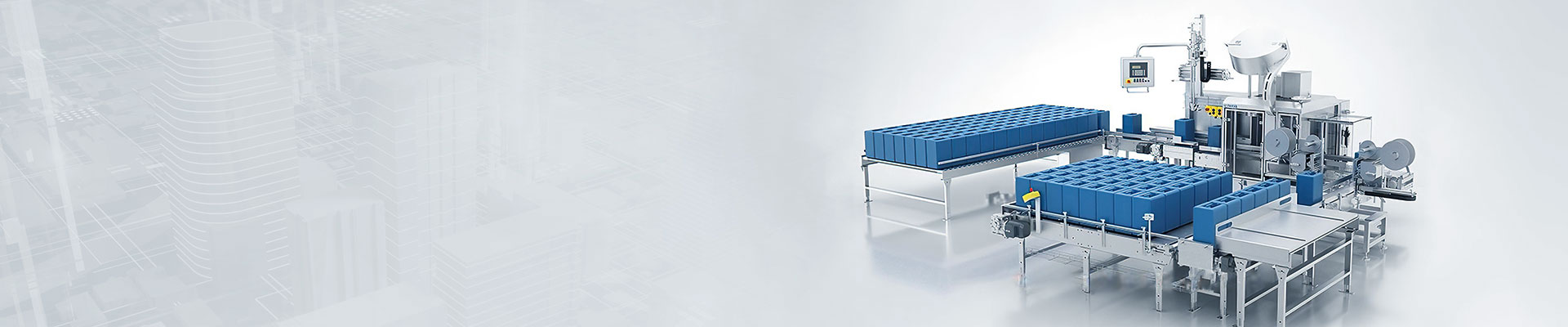
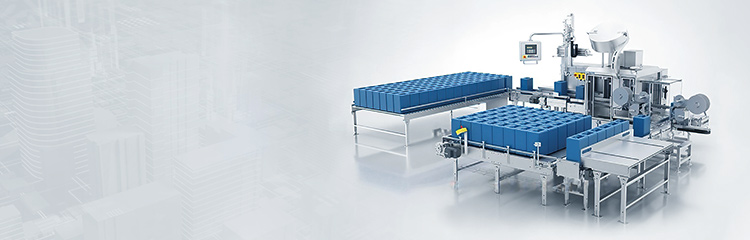
The wireless crane scale is the ideal measuring instrument for weighing suspended goods, with LED display, all-steel construction shell, good anti-electromagnetic interference performance, and can be used directly on electromagnetic suction cups. Excellent dynamic performance, even under strong shaking can quickly obtain stable and accurate weighing results.

Electronic crane scale to be composed of sensors, scale frame, weighing display master three major all components, will drive the weight of the items on the belt transmission to the load cell acceptance and transmission installation, but also the first degree of the weighing process of the items converted link, the electronic transmission belt scales the most important group of components. The accuracy and stability of a link for the function of the electronic drive belt scales play a decisive role in the use of the use of the crane scale sensor should also pay attention to avoid the use of overload.
Radio electronic crane scale by the scale body and instrumentation, the scale body contains a mechanical bearing mechanism, sensors, A/D board, wireless transmitter, power supply and shell, of which the mechanical bearing mechanism includes unloading buckles, hooks and pins. In addition, there is a sensor protection device to ensure the safety and reliability of the system.
Various functions: gross/net weight, zero setting control; date and time display; preset tare; storage and printing of number, item number, times, data statistics and inquiry, overload alarm, optional index value; anti-shaking effect setting, low battery warning and automatic power saving shutdown function.
Many considerate designs: backlit dot-matrix LCD display in Chinese, clearly visible during daytime and nighttime; Chinese character display user interface and built-in Chinese and Western micro-printer, intuitive and easy to operate; all-steel chrome-plated chassis, durable; antenna collision avoidance device to maximize protection of the antenna; environmentally friendly high-performance nickel-metal hydride batteries power supply, no leakage of liquids, lightweight, and charging/discharging cycle times, long service life. RS232 output interface. RS232 output.