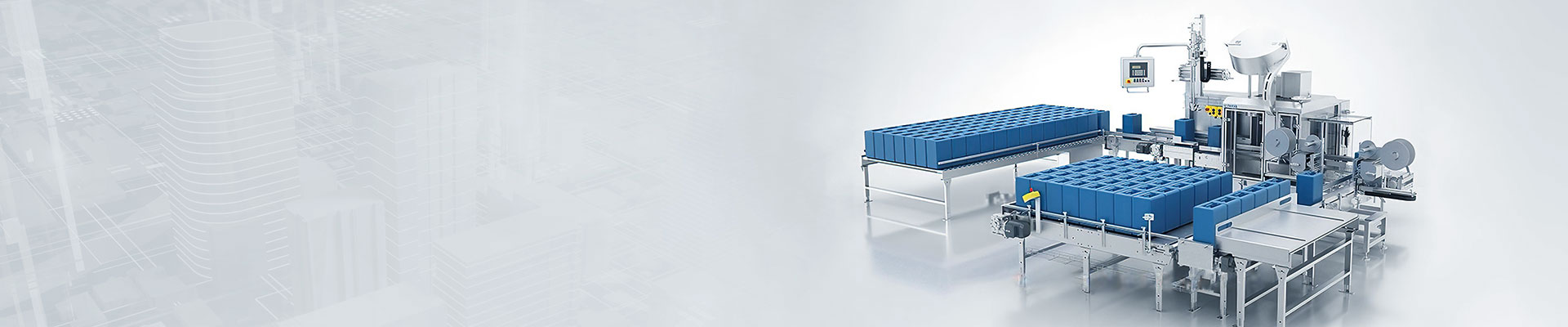
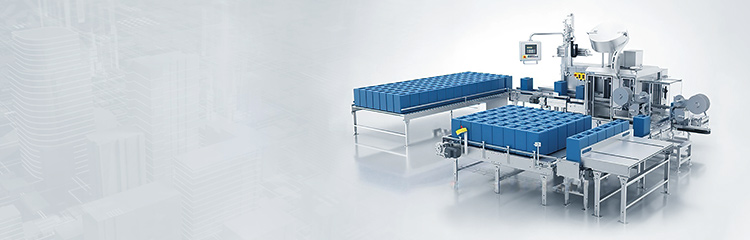
The electronic scale of stacking truck is mainly composed of touch screen +PLC and automatic weighing system, which can automatically realize the ideal weighing equipment for finished product production through the automatic control program of PLC touch screen through different sequences. A centralized control console is set, and the dynamic weighing and metering instrument is installed on the console. The electronic scale installed at the lower part of the supporting leg of the metering tank is connected with the dynamic metering instrument. Real-time data is transmitted from the metering instrument to the industrial computer in the control center through the communication line, and the weighing data and control commands are transmitted from the industrial computer in the control center to the instrument and PLC controller through the communication line.

Existing forklift trucks and Electronic scales are designed as a single unit, measuring and shifting at the same time, saving valuable time. Integral casting cylinder, the descending speed of the cylinder is not affected by the load, imported seals are used, and the piston rod is chrome plated. Internal relief valve provides overload protection, effectively reducing maintenance costs. High quality centripetal roller bearings are used at the connection of rotary shaft, which is flexible and non-shaking.
Stacker truck electronic scales are mainly composed of touch screen + PLC and automatic Weighing system, etc., can be various raw and auxiliary materials through different sequences, through the PLC touch screen automatic control program to automatically realize the finished product production of the ideal weighing equipment. A centralized control console is set up, the dynamic weighing and measuring instrument is installed on the console, the electronic scale installed on the lower part of the support leg of the measuring tank is connected to the dynamic measuring instrument, the real-time data is uploaded to the industrial control machine in the control center by the measuring instrument through the communication line, the weighing data and control commands are downloaded to the instrument and PLC controller by the industrial control machine in the control center through the communication line.
Stacker truck electronic scale adopts human-computer interaction, communication, display and storage, printing and other functions, and has data, graphic display, status monitoring, data input, information storage and other related operations of various functional screens. It can realize real-time process data monitoring, simulation display of process flow, electronic scale real-time data record access, operator privilege setting, process parameter setting, setting alarms for running process events and switching between manual and automatic control.
Forklift electronic scales are implemented by the configuration software to monitor and control, through the control interface to implement the process of operation, production data stored in a timely manner to the system database to complete a variety of production data storage and analysis, while also realizing the raw materials into the inventory of materials management, finished product management, personnel management, contract management and other functions.
Technical indicators
Technical Parameters
Model: CSD-0.5, CSD-0.75, CSD-1.0, CSD-1.5
Rated lifting capacity (kg): 500/0.1, 750/0.2, 1000/0.2, 1500/0.5
Lifting height (mm): 1600-5500
Load center distance (mm): 400 (500)
Outer width of fork legs(mm): 520, 580, 720
Fork length (mm): 800, 1000, 1150
Minimum Ground Clearance (mm): 85/90
Maneuvering form: Walking handlebar operation
Tire type: rubber or polyurethane
Driving wheel size (ф): 250*80, 260*90
Full load traveling speed (km/H): 0-6.0
Full load lifting speed(m/min):>4.5
Electric speed control system: Domestic/imported Mos tube stepless speed control system and electronic speed control handle.
Pumping station system: imported Italian pumping station
Full load climbing degree(%):5
Rated battery voltage/model (v/Ah): DC-24V 3QA-150*4, D-210*12, D-240*12
Reference use time: 5-6 hours
Drive motor (kw): 0.5, 0.75, 1.2
Hoisting motor(kw):1.5、2.0、2.2、3.0
Minimum outer turning radius R (mm) 1450, 1500, 1550, 1750
outline dimensionL*W*H:1550*750*1800、1630*800*1860、1732*800*1860、 1938*840*1960
Vehicle weight(kg):720、780、820