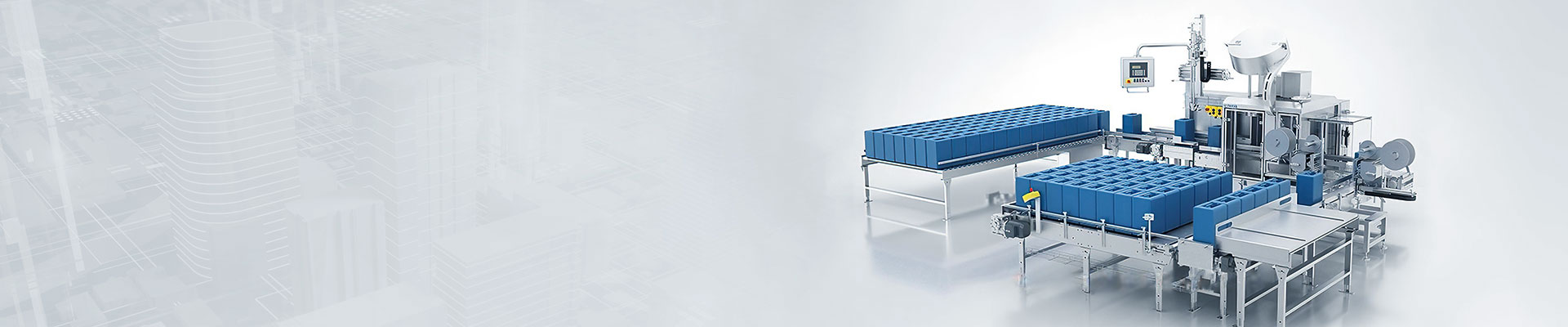
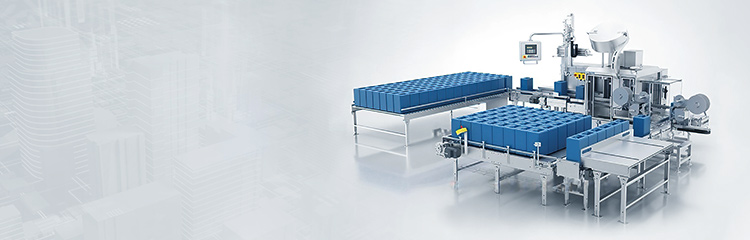
RFID weighing system has the functions of empty box storage (including initialization), real box storage and real box out of storage. Empty container loading is the loading task performed on returned empty containers. When the empty box is stored in the warehouse, the weight of the empty box is first weighed at platform B, and then the weight information of the empty box is read by an RFID reader at platform C. Finally, the weight information of the two is compared.

Tobacco storage RFID Weighing system adopts flat library mode, which is used to automatically store expanded tobacco and meet the function of automatically transporting the tobacco box to the export. The weighing control system is mainly composed of chain-plate conveyor, chain-lift transplanter, smoke-box disassembly/palletizing machine, smoke-box elevator, satellite trolley and other mechanical equipment, as well as electronic weighbridge detection device, RFID reader and electrical control system.
RFID weighing system has the functions of empty box storage (including initialization), real box storage and real box out of storage. Empty container loading is the loading task performed on returned empty containers. When the empty box is stored in the warehouse, the weight of the empty box is first weighed at platform B, and then the weight information of the empty box is read by an RFID reader at platform C. Finally, the weight information of the two is compared.
When the difference between the weight information of the two exceeds the standard, the smoke box is judged to be abnormal (damaged or containing debris), and cannot be stored and removed to the K platform for processing (cleaning or replacing the RFID chip). When the difference between the two weight information does not exceed the standard, it means that the smoke box is not damaged and does not contain debris, and it is allowed to be stored.
When the empty box is initialized, the weight of the empty box is first weighed at platform B, and then the RFID reader at platform C writes the basic information of the smoke box to the RFID chip (such as empty box weight, box number, box type), and then reads the information of the RFID chip to analyze whether the writing information is successful. If it is not successful, the smoke box is removed to the K platform for processing.
Empty boxes are provided from platform E of the cache line to the packing station, which automatically boxes the boxes according to the set weight, and then delivers the solid boxes to Platform G. Meanwhile, the net weight of the tobacco in the box and relevant information of the materials (such as batch number, specifications, quality information, etc.) are provided to the control system of Platform G. When the quality is abnormal, the system does not write any information to the RFID chip and directly excludes the real box to the Y platform. For the qualified smoke box, the information of the RFID chip is first written, and the information of the writer is the net weight of the tobacco, the batch number, and the packing time. Secondly, the information of the RFID chip is read to determine whether the RFID information is successfully written and the corresponding processing is performed.
When the real boxes are out of storage, according to the scheduling of the warehouse management system, the smoke boxes out of storage are successively sent to the J platform by the satellite car, conveyor and elevator. At platform J, the RFID reader reads the information stored in the tobacco box, and then compares it with the information of the outgoing tobacco box required by the warehouse control system. If the information is inconsistent, the tobacco box is returned to the third-layer tobacco warehouse, and the correct one is sent to the exit warehouse at Platform Y.