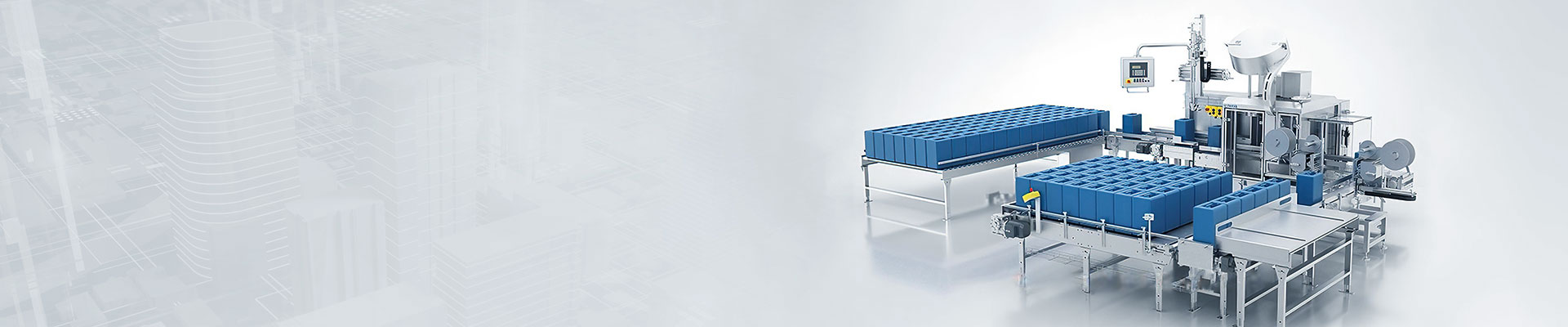
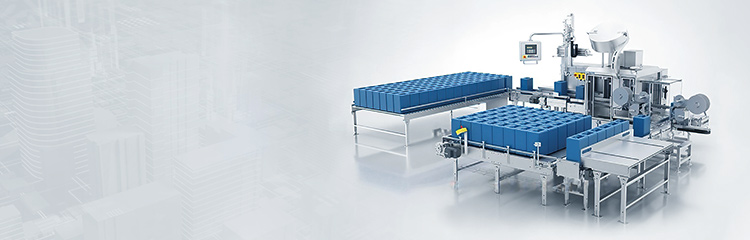
The real-time and TCP/IP-based communication on a line is realized by wireless PROFINET communication, and the controller, distributed I/O system and other Ethernet-based devices can be integrated into a common communication framework. It really realizes the synchronization of weighing and handling, and the data information of each weighing can be displayed automatically on the weighing instrument, which truly ensures the dual-purpose function of one machine and completes the weighing and transportation at the same time.

The weighing oil drum truck adopts the industry's high-precision weighing technology, which can accurately measure the weight of the liquid in the oil drum. Manual weighing is no longer needed, which saves complicated calculation steps and has higher accuracy. Just put the oil drum on the car, and the electronic display will display the weight data in real time, which is convenient and fast. Material handling and production efficiency of oil drum tipping truck with weighing function. Compared with traditional loading and unloading methods, weighing oil drum truck has many advantages.
The real-time and TCP/IP-based communication on a line is realized by wireless PROFINET communication, and the controller, distributed I/O system and other Ethernet-based devices can be integrated into a common communication framework. It really realizes the synchronization of weighing and handling, and the data information of each weighing can be displayed automatically on the weighing instrument, which truly ensures the dual-purpose function of one machine and completes the weighing and transportation at the same time.
Advantages of weighing oil drum dumper with Electronic scale: manual hydraulic lifting, manual turnover and 360-degree turnover.
It is used for simultaneous handling and weighing of dangerous goods such as transport tanks and discharge tanks.
The design structure is simple and light, and the hook/hoop structure is suitable for steel oil drums and plastic oil drums, and the operation is simple and labor-saving.
High-quality oil cylinder, fast lifting speed, lifting height can reach 1500 mm.
With electronic scale, it has the functions of zero setting, peeling and weighing, and the accuracy reaches 3/1000kg.
Bucket-holding mode of weighing oil drum dumper with electronic scale: holding type, hook type and hook-and-hold type are optional.