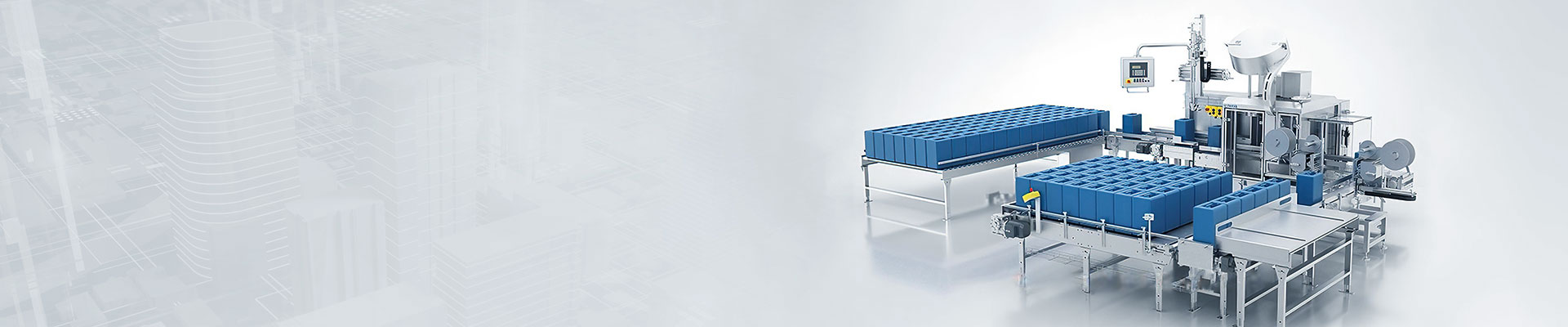
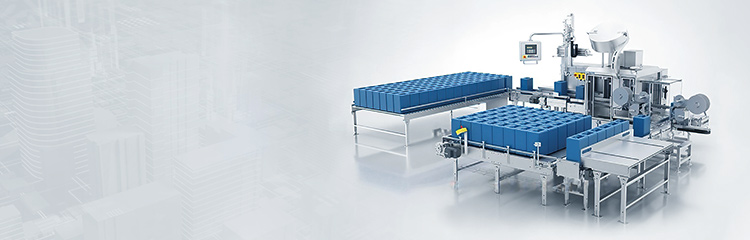
Automatic batching system is mainly composed of feeding system, weighing device, reactor and screw conveyor. It is suitable for mixing, batching and feeding of 3-8 kinds of materials. It adopts computerized scale for automatic control, pneumatic door to control the main material bin for quantitative feeding, and the material is mixed by the mixing bin and then automatically sent out by screw. It has the advantages of simple operation, high batching precision, adjustable material proportion, energy saving, easy to install and move.

The automatic Dosage system integrates the tasks of data acquisition, heating parameter control, sequence control, position control, speed control, banding control, temperature, and inverter control. It mainly accomplishes the tasks of initial data input, material tracking, process parameter setting calculation, data recording and reporting, man-machine dialogue processing, data communication, simulation resin modeling, historical data processing, application system startup, and dosage monitoring. The dosing system is directly connected to the process control level server, which is the main network of the system, connecting the controllers, data storage, and real-time acquisition of setup, sampling, and operational data. The common use of fieldbus and remote I/O realizes the purpose of replacing a large number of control cables with a small number of communication cables. According to the mixing and batching process characteristics and equipment distribution, each function controller mainly completes the batching area logic control, man-machine dialog, data transmission, data processing and material tracking and other functions. According to the field experience convergence dosage program, this program in the dosage industry play a role in lending sign? Next to introduce the control process of the dosage system, the distribution of each control of the feeding system is as follows:
(1) heating kettle dosage area with a total of 6 PLC. weighing and dosage system data using Ethernet, Profibus-DP network and other means of communication, the main controller using Ethernet and the host computer and other areas of the rolling line for data transmission. The system transmits the data to the upper computer, the reactor gets the signal to feed from the mixing storage tank, and the frequency converter sends the running signal to the rotor pump. The system controls the reactors in sequence according to the specified reactors, pumps the material from the discharge storage tank, controls the reactors by weight as the quantitative control, and at the same time feeds back to the rotor pump to stop conveying to the reactors.
(2) There are 3 PLCs in the mixing area, the task of the mixing area is to convey the outgoing reactors to the dosing area of the measuring reactors. Mixing area mixing different reactors stirring speed according to the order of sequential control, with a good liquid and then the heat preservation cover control.
(3) batching area with a total of three PLC. finished product batching area to control the weighing accuracy is closely related to the kettle conveyance, in the batching area using a weighing controller, that is, each weighing and batching machine set up a weighing controller, built-in a PIIICPU, the three Weighing modules are installed in the bottom of the kettle, to control the kettle filling and packaging packaging and so on.
(4) weighing and sorting area is set up a total of five PLC. to weigh and fill the completion of the output roller conveyor speed control through the power drum, speed control and automatic skip step control, packaging weight detection filling qualified range, unqualified filling weight were underweight and overweight management segmentation conveyance and management.
(5) Mixing area batching area selecting area CPU board integrated Ethernet port, support 10/100M communication, greatly improve the communication ability. The data is centrally managed in the central control room.
(6) Open structure based on VME bus, bus controller structure and a wide range of third-party VME-based CPU boards and I/O modules. Supports existing 90-70 I/O and new I/O in the same rack.
(7) Integrated Development Engineering Environment for Windows CimplicityME provides a broad engineering development environment for all programming, configuration and diagnostics of the PACSystems?RX7i series. In addition to I/O points, variable names can be programmed directly without concern for address assignment, making the design more flexible and improving the efficiency of engineering design.
(8) The weighing and dosage system adopts an open VME bus structure, which allows the installation of VME standard modules from more than 300 different manufacturers. In the system configuration, in addition to its own rack I/O modules can also be connected to remote I/O modules through the field bus (such as ProfibusDP), constituting a powerful and reasonably priced control platform to meet a variety of large-scale, complex high-speed control requirements.
(9) The low cost and high performance of the GE90-30 PLC series makes it easy to replace everything from simple relays to complex medium-sized automation system applications. Its CPU has powerful features such as built-in PID regulation, structured programming, interrupt control, indirect addressing and a variety of function modules to successfully complete complex operations. In addition, the 90-30 series has highly functional special modules available, such as high-speed counter modules and ProfibusDP communication modules.
(10) The VersaMax series PLC provides a wide range of I/O modules for more flexible configuration. The communication module can connect VersaMax with ProfibusDP network (or other industrial fieldbus) to realize remote control.