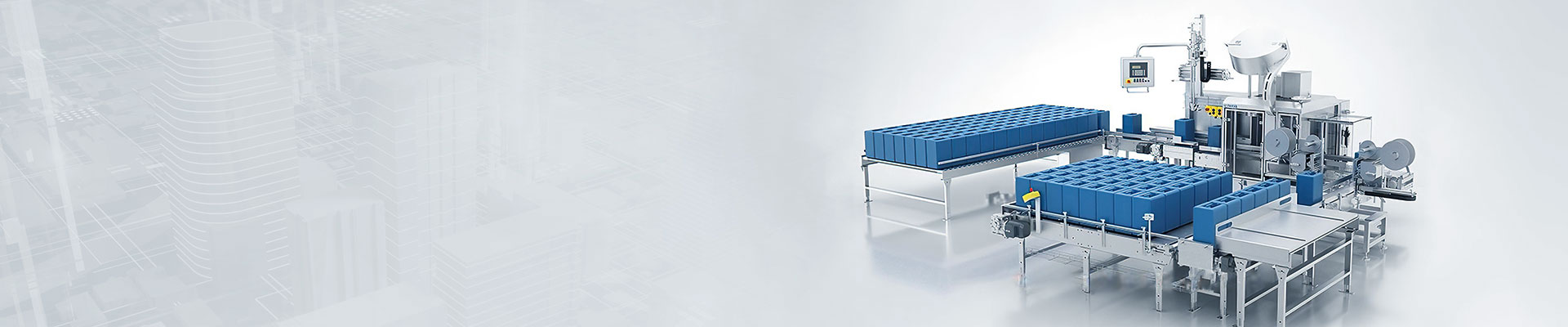
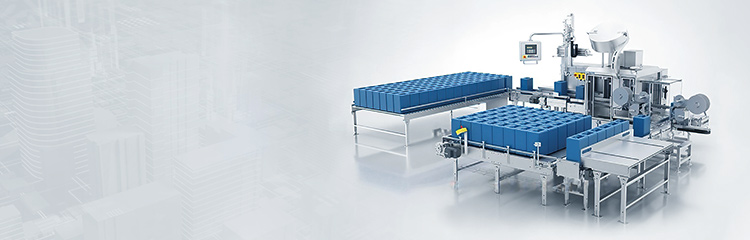
Explosion-proof weighbridge will weigh objects placed on the load-bearing scales, there will be a certain gravity on top of the load-bearing scales, by the scales will be subjected to the distribution of force transmission to the various load cells, in the sensors, the original gravity signal through the deformation of the strain gauges of the force is transformed into an electronic signal, and then drive the electronic signals to the junction box for the organization of the convergence of the weighing instrument through the collection and processing of specific weighing information, after which the weighing value can be displayed. The weighing information is collected and processed by the weighing instrument, after which the weighing value can be displayed. In addition, the weight indicator can be connected with the computer, and the data information can be sorted out by the tool software, which is convenient for users to analyze the data and store the relevant work.

Explosion-proof weighbridge is used in the site with explosive gas or explosive dust, and can be divided into different hazardous level areas according to the frequency, duration and degree of danger of explosive substances. Various technical measures such as voltage reduction, current limitation, isolation, sealing and optical communication are taken to eliminate or block the possible triggering sources (electrical sparks, electrostatic sparks, high temperature ......) in the electrical lines of the weighing scale so that the vehicle weighing scale can work safely in the corresponding hazardous areas.
Explosion-proof weighbridge will weigh objects placed on the load-bearing scales, there will be a certain gravity on top of the load-bearing scales, by the scales will be subjected to the distribution of force transmission to the various load cells, in the sensors, will be the original gravity signal through the deformation of the strain gauges of the force transformed into electronic signals, and then drive the electronic signals to the junction box in the collation of the convergence of the weighing instrumentation through the collection and processing of the specific weighing The weighing information is collected and processed by the weighing instrument, after which the weighing value can be displayed. In addition, the weight indicator can be connected with the computer, and the data information can be organized by the tool software, which is convenient for the user to analyze and store the data and other related work.
Technical parameters:
Table size: can be customized according to requirements
Accuracy class: OLML Ⅲ, index value: ≥2000
Working temperature (℃): (instrument -10 to +40) (scale body -30 to +65)
Power supply: AC220V (-15% to +10%), frequency: 50 ± 1
Standard configuration:
One set of weighing platform (including load cell, connecting parts, junction box).
One explosion-proof weighing instrument.
One printer (for non-explosion-proof area)
One set of pre-buried base plate, limit support and fasteners.
One signal cable (50 meters).
Selection of accessories: computer and weighing software, large screen display, regulated power supply (for use in non-explosion-proof areas).