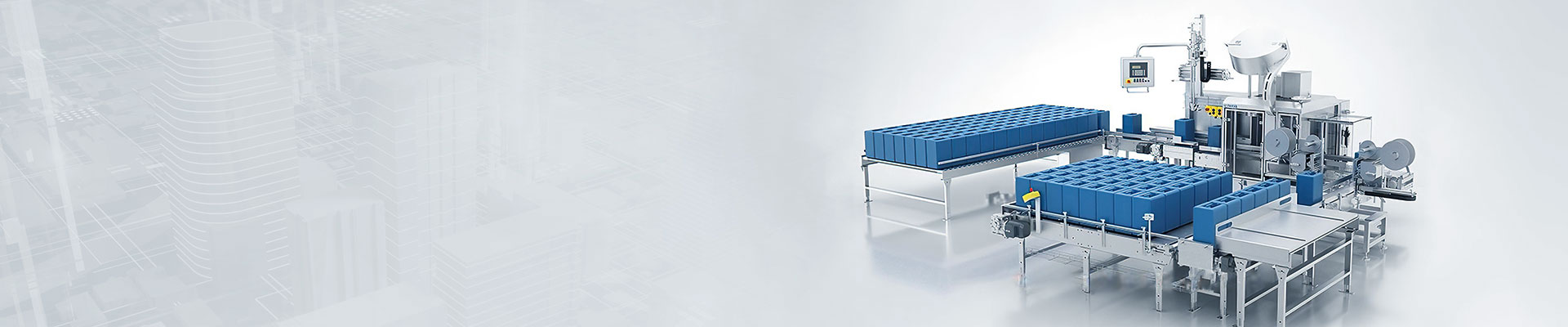
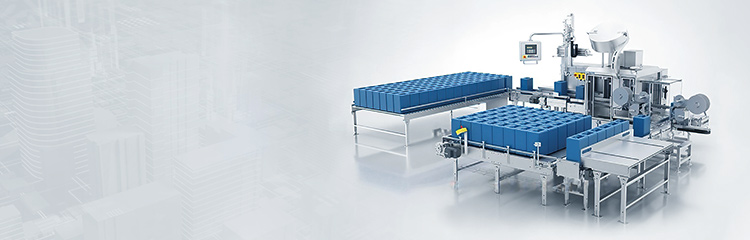
称重灌装机当储液箱内的液体液位在下液面(下限值)及以下时,浮球压板脱离机械阀及气动蝶阀打开,通过进料口向储液箱内输送液体物料,随着液体液位不断上升,浮球组件按箭头方向旋转,当储液箱内的液体液位达到上液面(上限值)时,浮球压板压下机械阀触头及气动蝶阀关闭,停止向储液箱内输送液体物料。灌装系统选用气控阀、机械阀、气动蝶阀控制。

称重灌装机采用集散型结构,开放性好、易于扩展、性能稳定可靠“结构模式:“上位计算机+PLC系统+灌装触摸屏控制仪表”,各部分设备的连接采用RS485现场总线,结构简单、可靠。填充机采用优质的控制器,具有高精度,高可靠性,抗干扰能力强等特点。传感器选用高精度称重模块。称重模块安装简单、维护方便。
称量灌装机使用的计算机监控管理功能强大、实时采集,及时显示运行工况及有关数据,画面形象逼真,动感强;可自动完成系统灌装工艺流程,计算机画面实时显示工作流程,软件操作简单,画面逼真。上位机软件设置运行密码和重要参数密码修改保护,且用户实现分级管理,可任意定义人员的权限。智能报表软件为生产管理提供大量数据信息,如灌装结果列表、原材料消耗列表、生产量列表、灌装使用结果记录等,可按时间、灌装等生产班报、日报、月报和年报等统计及打印功能。故障响应准确及时,可自动显示或打印故障时间、性质和地点,并进行声光报警;控制模式可分为远程自动、本地自动、本地手动以及本地仪表控制等操作方式。
基本参数:
最大秤量:30kg
最小感量:0.1kg
灌装误差: ±0.1-0.2kg
灌装速度:20L约1500-1800桶/小时
控制方式:2挡控制
灌装方式: 插入式,液面上
枪头管路: 特氟龙枪头、阀门+特氟龙软管
结构材质: 液体灌装机主机SUS304不锈钢,输送码垛碳钢防腐漆。
秤台尺寸:400×800mm (304不锈钢动力滚道)
空桶滚道:400mm×2500mm (304不锈钢动力滚道)另附1200mm斜坡无动力滚筒
重桶滚道:400mm×2500mm (304不锈钢动力滚道,2组)
分桶装置:适用于20L桶,碳钢防腐漆结构,304不锈钢滚道。
码垛设备:平移式,适用托盘1200*1200*140mm,含供托盘、码垛、下托盘输送。
管路压力:0.2-0.6MPa(与料性有关)。
物料接口:DN40法兰接头4个,可按用户提供接口标准
气源接口:用户提供12mm气管接头,用于快速接头连接
使用电源:AC220/50Hz(用户提供至机器一侧)
使用气源:0.4-0.8Mpa(用户提供至机器一侧)
使用温度:-10℃-50℃
基础条件:水平的坚固混凝土地面,混凝土厚度应大于10cm。
可选机型:标准型、防爆型灌装秤