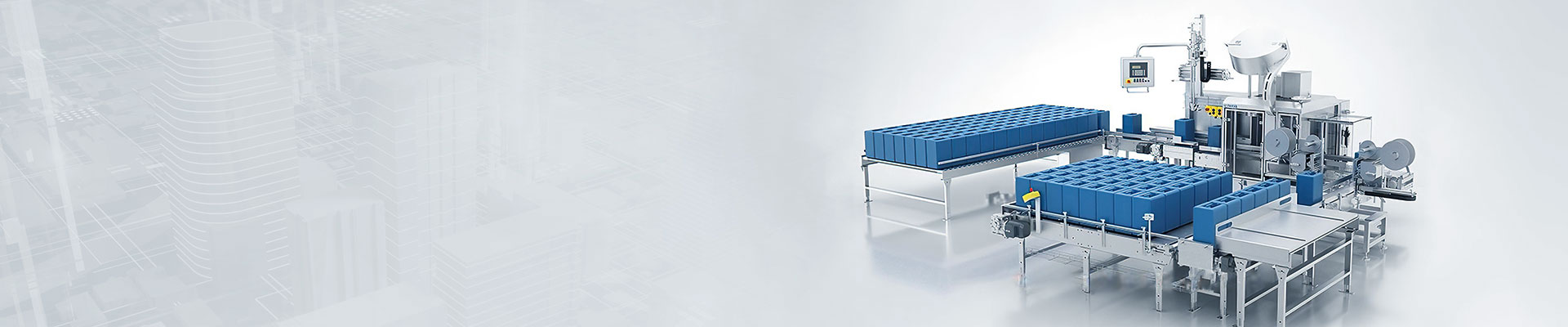
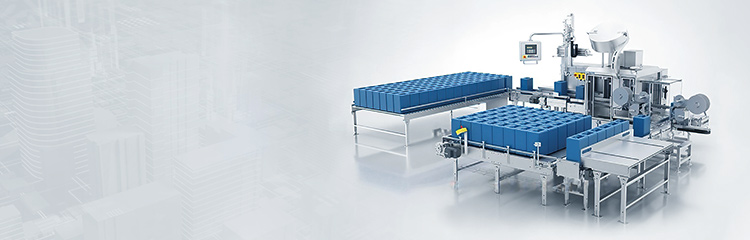
PRODUCTS
防爆电子秤具有人机交互、通讯、显示及存储、打印等功能,并具有数据、图形显示,状态监控、数据输入、信息存储等各种有关操作的功能画面。实现实时过程数据监视、模拟显示工艺流程、实时数据记录查阅、操作员权限设定、工艺参数设定、设置运行过程事件报警及手动与自动控制切换。监控系统中现场控制称重仪表实时显示流量、载荷、累计值、温度等。温度指示通过现场温度显示仪表、压力指示通过现场压力及电机经现场显示仪表远传至中控室集中显示。
Product details

防爆电子秤通过A/D转换实时显示物料的重量,通过串行通讯的方式将显示重量数据传送到PLC,PLC将采集到的仪表重量与触摸屏(或计算机)设定的重量比较,称重仪表进而控制整个电子秤称重的动作。如果配置了计算机管理系统,计算机可动态显示的工作状态。
防爆电子秤具有人机交互、通讯、显示及存储、打印等功能,并具有数据、图形显示,状态监控、数据输入、信息存储等各种有关操作的功能画面。电子地磅系统可实现实时过程数据监视、模拟显示工艺流程、电子秤实时数据记录查阅、操作员权限设定、工艺参数设定、设置运行过程事件报警及手动与自动控制切换。监控系统中现场控制称重仪表实时显示流量、载荷、累计值、温度等。温度指示通过现场温度显示仪表、压力指示通过现场压力及电机经现场显示仪表远传至中控室集中显示。变频器调节配备自动切换开关,与主控计算机通讯。
精度等级:OLMLⅢ,分度值:≥2000
工作温度(℃):(仪表-10至+40)(秤体-30至+65)
使用电源:AC220V(-15%至+10%),频率:50±1
台面尺寸:要求定做