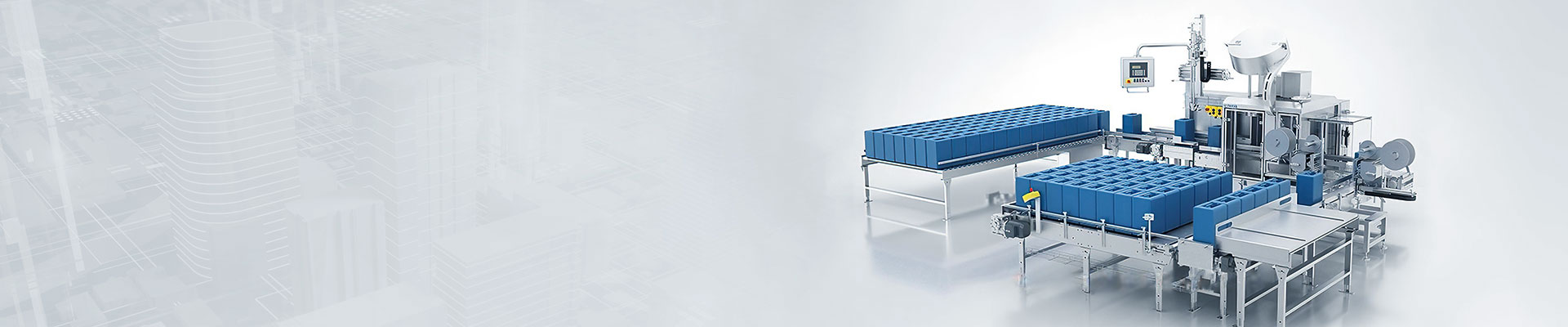
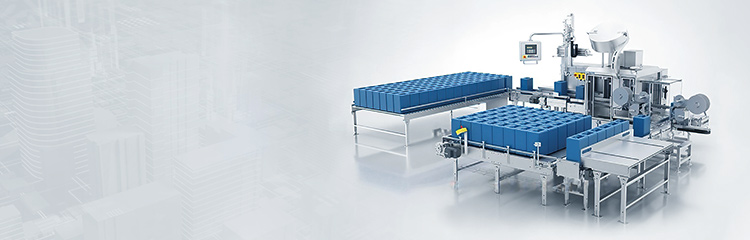
配料机主要为称重仪表,PLC作为辅助控制系统,计算机人机界面显示配比参数(配方)及监控记录实时数据。在自动控制方式下,单击前配工艺画面中自动配料“启动”按钮,或前配控制柜“启动”按钮,称重仪表就按设定好的配方打开电子秤的称料阀。系统检测到某秤配料阀未关,会发生报警并进入暂停状态。每台秤根据称料快慢设有提前量,当控制仪表检测到秤称料重量达到设定值时,会减去提前量,控制仪表则关闭进料阀。提前量可人为修正或自动修正,使控制称重仪表控制配料秤每次配料精度达到设定的目标值。

配料机是对散状物料进行连续配料和计量的理想设备,可用于计量给料又可多机组合进行自动配料,用于对各种粉状、颗粒状物料进行连续输送的动态计量,为特殊工业现场的生产、控制、管理提供准确性的计量数据。该设备由两根非对称式螺旋,在绕轴线自转的同时借助转臂的回转作用在锥体内作公转运动,通过螺旋的公、自转将物料反复提升最终达到混合均匀的目的。该产品适用范围广阔,能进行粉体与粉体、粉体与液体的混合,易能搅拌细粉、纤维或片状的物料;该设备是市场上开发应用较早的混合机之一。
称重投料系统有两套接收和称量控制系统:套批量接收和配料,批量车辆通过出料正压运送到临时液体料仓。料仓的液体通过隔膜泵从料罐排出,螺旋由料仓排出,检查后以正压气压方式传递到混合仓。搅拌仓的液体通过隔膜泵从料仓排出,管螺旋推进器从料仓排出。使用定量螺旋推进器搅拌重型液体,管螺旋推进器通过分布器混合进入料仓。设置传递过程中的磁分离过程。由于高密度相气力输送,除尘系统只需要少量吸入除尘的相对移动料斗、空压机料斗和液体料仓;除尘器的计量通过气压方式运到液体料仓。批量料仓单独安装插件脉冲除尘器。
自动喂料机使用由空压机和旋转阀组成的正压高密度相气力输送系统,直接输送到反应釜,动力由压缩机提供。配料压力高,流量低,但承载能力大,对物料影响不大。运输过程中需要高压,所以液体物质会堵塞。相应地,液体输送管根据每个输送装置的计量布局安装辅助风道、解除阻塞管和阀门。堵漏应该沿着输液计量放置。阻塞臂管的外径为φ50~φ100mm,支管直径为φ40~φ65mm,阻塞支管和液体输送管的水平角度不超过30。止回阀、插头阀或球阀必须安装在输液计量附近的下水道计量中。除尘器处理的计量通过现有的正压气体输送回液体反应釜。罗茨鼓风机提供出料来源。为了防止脉冲排出,在脉冲底部安装出料注入口,使反应罐流化。