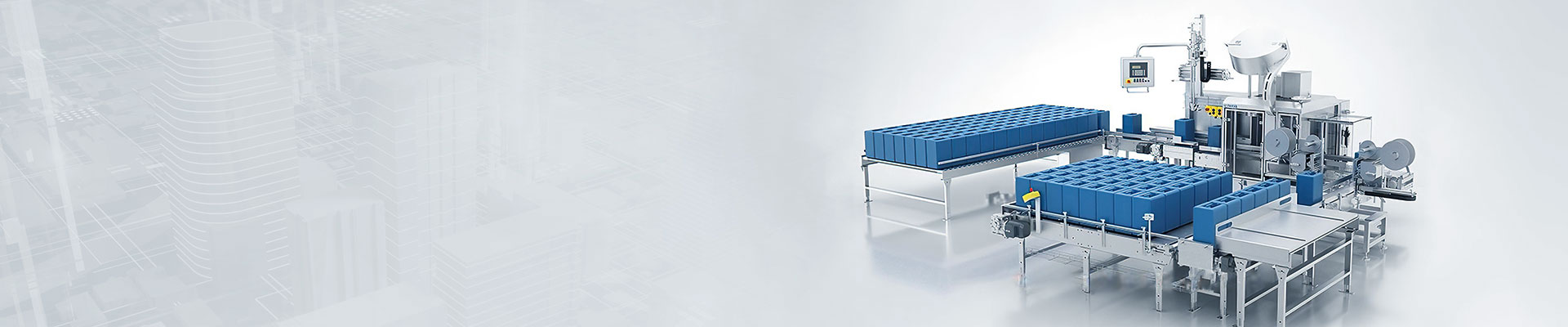
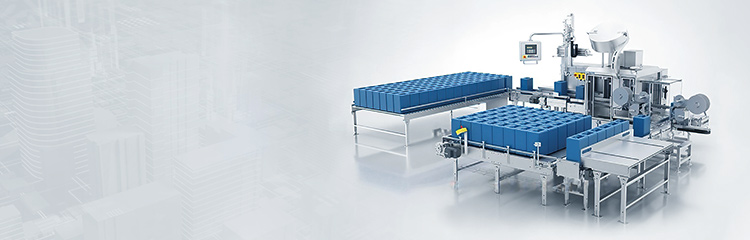
防爆配料机是在化工生产工艺中的一道电子秤非常重要的工序,主要完成主料和各种配料的称重、配比。后配料将前系统形成的基粉通过皮带秤和传送带送人预混器与的各原料混合后,由传送带送人成品仓。后配料实现了对输送物料流量的计量。

防爆配料机包括原料的储存、输送、称重配料、除尘、物料混合、包装灌装等多种设备,涉及粉状、粒状、块状、片状及液体等多种物料;可根据行业特点及工艺要求,结合物料特性,合理的选择单料配料、多料顺序累加、减重配料、失重秤配料、皮带/螺旋秤、散料秤等多种计量方式。
配料系统由一套PLC系统和一套上位机监控系统组成。PLC系统由硕人时代STEC系列控制器和仪表及通讯电缆组成,STEC控制器之间用以太网通讯,控制器还提供RS232、RS485接口和ADSL、GPRS、CDMA、光纤等通讯,上位机监控系统采用Windows操作系统,安装硕人时代SRDev2.0编程软件及HOMS5.0组态软件。对整个配料系统进行实时监控,画面显示和报表打印;PLC:实现配料的自动控制。
此系统采用顺序启动、顺序停止、紧急停止、同时启动,手动时将现场控制箱和仪表箱的转换开关都打到手动位置,由现场控制箱上的启停按钮、电位器、频率表等实现控制,由称量仪表显示物料瞬时量及累积量。主要用于网系统故障PLC控制配料发生故障或其它原因,需要进行手动检修试车工作情况下的应急操作。半自动时将现场控制箱和仪表箱的转换开关都打到自动位置,由现场控制箱上的启停按钮、频率表、称重仪表等实现控制,可以通过称重仪表设定的配方自动调整配料量,显示物料瞬时量及累积量;也可通过现场的操作屏,设定配方来调配料量。主要用于不需要上位控制时,实现现场操作。全自动时将仪表箱的转换开关打到联动位置,由上位机控制皮带的启停,动态显示各物料量、运行状态、各种报警指示,各配料量由上位机根据工艺要求统一设定,可进行采集和处理各配料控制回路来的称量信号与开关量状态,实现整个配料系统的给料、称量检测、料量调节,选择和切换料仓等配料过程的自动控制。此时现场手动控制配料系统不起作用,完全通过中控室进行操作。
顺序启动用于配料的初次启动或者顺序停止后的配料系统再启动,顺序启动功能可以控制参加配料的给料设备按照皮带的运行方向按一定的时间间隔依次启动,保证料头能够对齐。顺序停止:用于希望长时间停车的场合,这样可以保证输送皮带上的物料都运送干净,使皮带处于物料状态,并且可以保证料尾对齐。紧急停止用于发生紧急情况所有参与配料的设备立即停止运行的场合。同时启动用于急停后的再启动,能够使配料系统在上一次的“断点”处接着往下运行,就像没有发生过任何事情一样。(注意:不能随便,无顺序的点击这四个按钮,必须按操作要求来操作。)
当某种物料量所需配比确定后,将其作为设定值输入上位机,经网络传输给称重仪表。物料落到称重螺旋上,其重量由称重传感器检测,取得物料流量(测量值)的反馈电压信号到称量控制仪表并运算成为PV当前值,经PID运算再输出4~20mA控制信号至变频器,以此改变其U/F输出值,从而改变皮带速度来控制物料量的大小,实现自动配料。物料配比的控制:本配料系统给料任务以来自上位机的配比输入与计算进行控制为主,即将各种原料的工艺参数输入计算机,由计算机直接对各料种进行设定和配比协调。当上位机出现问题时,可以通过现场的操作面屏来实现自动控制。
解决方案的主要功能
监控功能:对皮带称配料过程的瞬时流量、日累计、月累计、年累计等参数进行检测和监视;
画面显示:通过计算机显示器可显示配料过程中有关控制参数的运行状况,以及显示实时配料曲线和表格;
打印管理:可随时打印配料报表,以便保存和查询;
通讯功能:工控机与PLC和仪表之间进行可进行双向数据及信息交换;
数据处理:系统可自动对采集的信号进行运算处理,并输出到相应的控制量;
控制功能:根据操作前相应的设定值,自动控制设备的正常运行,包括PID调节;
报警功能:上位机以画面方式和声光信号方式对各种参数超限或设备状态异常进行报警。