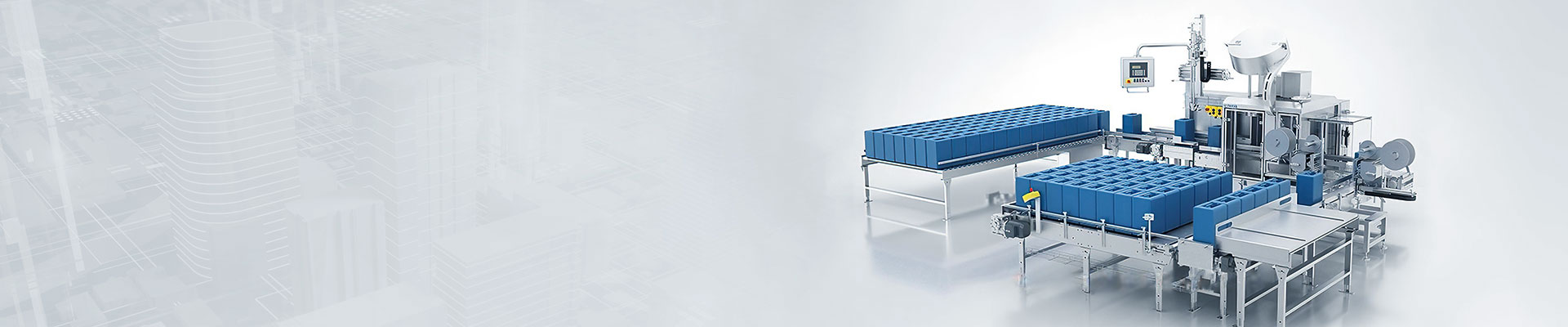
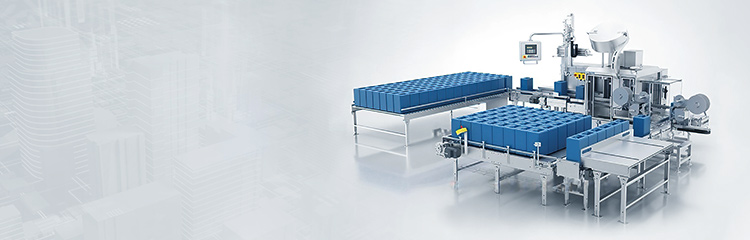
The electrical part of pneumatic batching scale is mainly composed of weighing sensor, weighing instrument, programmable controller (PLC), inverter, industrial computer and printer. In the process of dynamic weighing, the weight signal of the weight sensor on the quantitative weighing hopper is received. When the weight of the material in the hopper reaches each set value, the output I/O quantitative signal to the PLC. PLC collects the quantitative output signal of the weighing instrument, and controls the output frequency of each frequency converter through PLC, so as to control the thickness and fine feeding amount of the corresponding vibration feeder and the switching door action of each weighing hopper.

The electrical part of pneumatic batching scale is mainly composed of load cell, weighing instrument, programmable controller (PLC), frequency converter, industrial control machine and printer. During the dynamic weighing process, it accepts the weight signal from the load cell on the quantitative weighing hopper. When the weight of the material in the hopper reaches the set value, it outputs I/O quantitative signal to PLC, which collects the quantitative output signal from the weighing instrument, and controls the output frequency of each frequency converter through PLC, so as to control the quantity of coarse and fine material of the corresponding vibrating Feeder, and the opening and closing of the material door of each weighing hopper. The industrial computer communicates with the weighing instrument through RS232 interface and displays the obtained weighing data of each scale on the monitoring screen, so that the user can adjust the formulae on the panel of the weighing instrument or on the operating interface of the industrial computer.
Dosing scale is mainly to Roots fan generated airflow as a carrier to particles, powder, small pieces of material transport to the designated discharge point of the pneumatic conveying system, flexible conveying pipeline arrangement, good airtight, less dust overflow, energy saving and environmental protection, high efficiency, simple operation and easy to maintain, can be realized in the bulk of the material transport, the degree of automation is high, and effectively reduce the cost of personnel conveyor costs, packaging and loading and unloading costs, in addition, positive pressure In addition, positive pressure pneumatic conveying system conveying process, but also at the same time on the material for a variety of materials or chemical processes, such as mixing, crushing, grading, drying, cooling and other processes.
Positive pressure dilute-phase pneumatic conveying system configuration generally use Roots blower as the air source, Roots blower in the forefront of the system, relying on the fan's outlet wind will be blown to the material far away from the receiving bin.
Positive pressure dilute phase pneumatic conveying dosing scale is mainly composed of Roots fan, conveying system (rotary feeder, continuous conveying pump, pipeline, switching valves, valve instrumentation, etc.), ash storage system (ash storage, roof dust collector, dry ash bulk loader, humidifying mixer, valve instrumentation, etc.) and other equipment, mainly powered by the Roots fan, ash hopper storage ash is sent by pipeline into the ash storage, and then transported out by tanker trucks or automobiles, because of its Because of the low pressure of gas source and low concentration of dust in the pipeline, it has the advantages of large conveying capacity, low energy consumption, wear and tear of equipment and low maintenance cost.
Dilute phase positive pressure pneumatic conveying batching scale
Characteristics of batching machine
①Positive pressure dilute phase pneumatic conveying system equipment, high degree of automation, less investment in gas, simple operation and easy maintenance, energy saving and environmental protection with high efficiency;
②the use of gas dynamic pressure, the material at a higher speed in the pipeline forward (8m / s-25m / s), conveying pressure along the conveying pipeline is gradually reduced;
③Continuous conveying, conveying flow, conveying speed and conveying pressure, material and gas ratio is basically stable, high operational reliability, easy maintenance;
④When applied in closed-loop system, it is not necessary to increase the pneumatic buffer equipment, and it is easy to control;
⑤Short conveying distance, especially suitable for short or medium distance pneumatic conveying;
(6)The system conveying is continuous conveying, can also be intermittent, no accumulation of materials in the pipeline, conveying the environment less pollution.