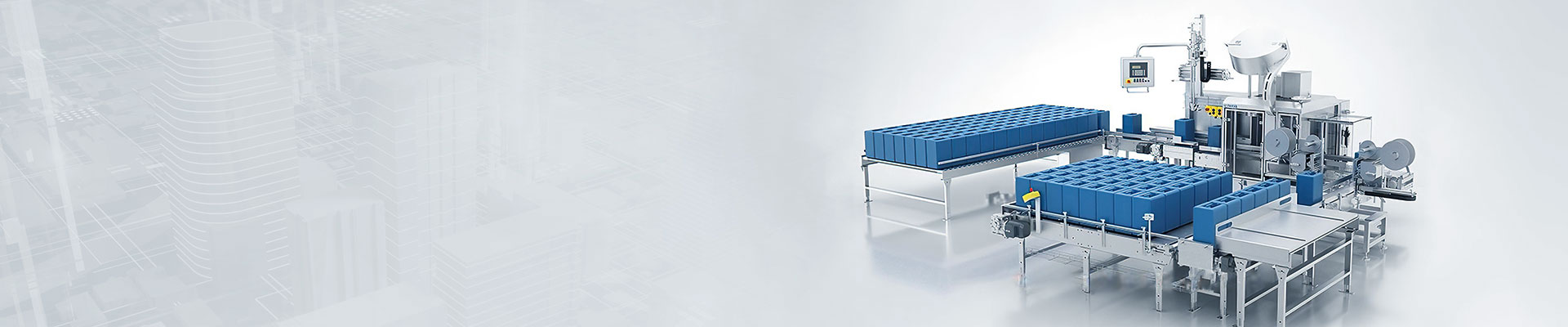
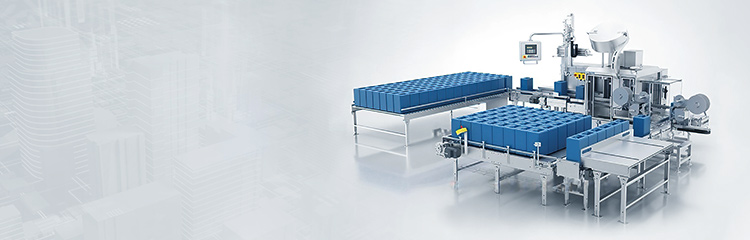
称重分选机分级卸料过程实时控制系统,提出一种产品等级信息与产品实时位置间的连续动态配准方法,实现输送线上产品流的动态位置的实时检测、连续跟踪、产品等级信息与其实时位置间的连续动态配准以及产品分级卸料过程的自动控制。给出控制系统的电路结构,分析步进电机的控制过程,实际运行实验表明,在该系统的控制下,所有产品都能在检测装置为其判定的等级出入口处自动平稳卸料。

检测机为通用系统,所处环境和检测对象千差万别,因此需要根据具体的环境和检测内容进行相应的配置。通常嵌入式系统的程序调试需要使用仿真器,只能对程序代码进行修改,费时费力,使用不便,故本系统设计了一套可以通过网络接口进行在线配置的程序。这样只需一根普通网络直连线将检重机与电脑相连,利用该程序就可以方便地配置系统参数及实时察看图像情况。配置内容包括相机IP地址及端口号、SPI配置及输出、UART配置、图像高宽及增益等属性、相机曝光时间等参数和相关图像存储等操作与显示该图像等。
采用合适的算法对所采集到的图像进行有效处理外,工业在线分选秤还必须满足实时性的要求,因此需要对算法程序进行优化,以充分发挥DSP的运算能力。DSP是一种具有并行指令执行功能的器件,本系统所采用的DM642可以在一个指令周期内并行执行8条指令。优化的目的就是使程序语句之间的相关性降低,更多地以并行方式被执行,充分发挥DSP的运算能力。除此以外,当系统采用C语言优化设计仍不能满足要求时,需要将运算量大的以循环体为主的核心程序采用线性汇编编程。
为分选机在实际工作生产线上所采集到的图片,为在包装生产线上进行的药片检测,检测内容为查看物品是否被装进包装中和药片是否有破损。该包装设备运行速度为2m/s。可以真实采集到高速生产线上有检测目标图像,而且图像灰度均匀、基本无畸变,细节清晰,完全能够满足图像处理的要求,采用优化过FFT程序对系统运算速度进行的测试中,测试对象为1024x1024黑白图像,运行时间为14ms。中断的出现会打断处理程序的运算,再加上执行一次中断需要进行一系列保护和恢复当前运算过程的程序,这些都会使得中断处理的效率与运算程序相比低得多。给出了每秒出现中断次数与运算效率之间的关系。