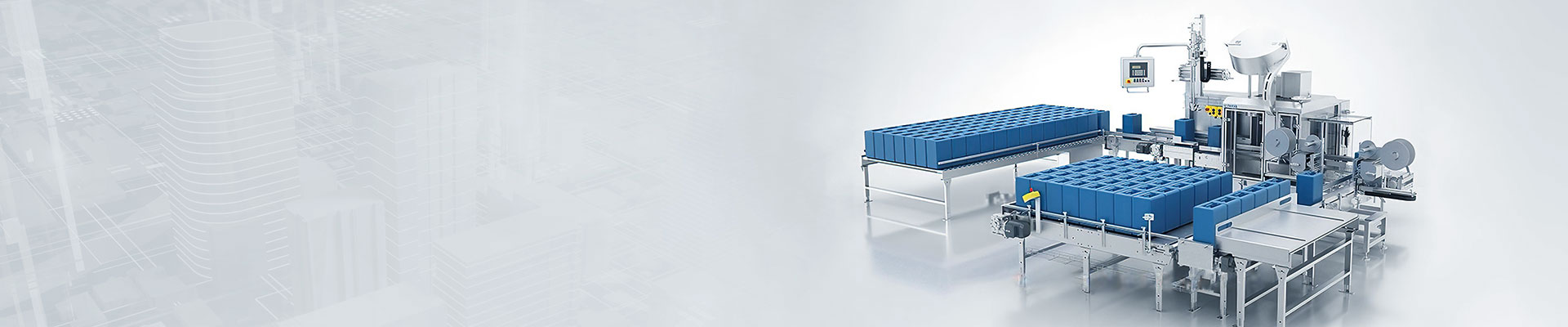
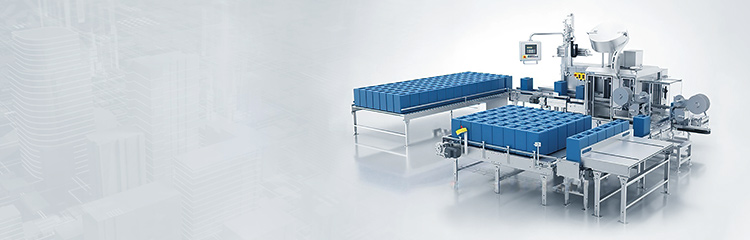
自动配料系统是反应釜混配生产过程的重要组成部分,通过电子地磅直接采集重量信号,自动控制称重,操作人员通过键盘或鼠标在上位机人机界面(HMI)上输入加料信息(加料种类、重量等),监视上料控制的全过程,打印加料的结果和生产报表,实现上料过程的测控管一体化,不失为一种切实可行的有效方法。

配料机采用调节阀或改变发料罐压力进行配料,将重量值进行PID调节配料罐的压力或调节阀的开度。采用标准比例功能和称重系统的比例计算,保证称重性能的稳定。给出值经过乘法器计算配料重量目标值,作为控制量的远程给定,取倒数后经乘法器计算出料重量,从而实现交互配料。
具有全自动控制功能和称重数据管理功能。生产过程中它可以按工艺流程要求,称量模块根据预定配方,对多种物料按固定比例重量值将物料加入料斗秤内,反应釜当称量显示到量后(即完成每一种物料的称重计量),反应罐再按照卸料程序将物料一次或分步多次卸入混合机入料口。
投料系统原理
1.称重料控制系统实时采集称重计量罐上的重量信息
2.将当前的流量数据在控制系统处理经过运算后输出控制信号至给料机构。
3.此时开始计量从计量罐中流出的物料重量,当累计值等于设定重量时,定量控制系统将关闭阀门停止定量流程。
性能特点
1.配料控制系统具有全自动控制功能,可在手动/自动配料功能之间切换。
2.可适应恶劣的工作环境。
3.可根据用户需求进行配方管理,例如,配方输入、存储、调整、删除、修改,软件具有保密功能,即计算机内的数据不能随便拷贝和下载等。
4.在工作过程中,可实时显示配料数据,便于及时作出调整,可对称重数据进行管理,记录配料数据和统计报表。
5.可对多种物料按配方要求自动配料,具有配料过程中自动密封对接入料口、出料口,并可实现配料过程中的收尘功能;
6.配料具有配料车准确定位,定位精度正负10mm;
7.提供历史数据查询系统,在授权情况下可查询任一时间段配料参数,提供打印功能,在授权情况下可打印任一时间段配料参数;
8.人机界面清晰易懂,控制系统能自动计算并在显示屏上显示出储料仓内物料的重量,自动称重的运行状态、瞬时重量、累计重量等文字或图像信息,具有界面的模拟功能。