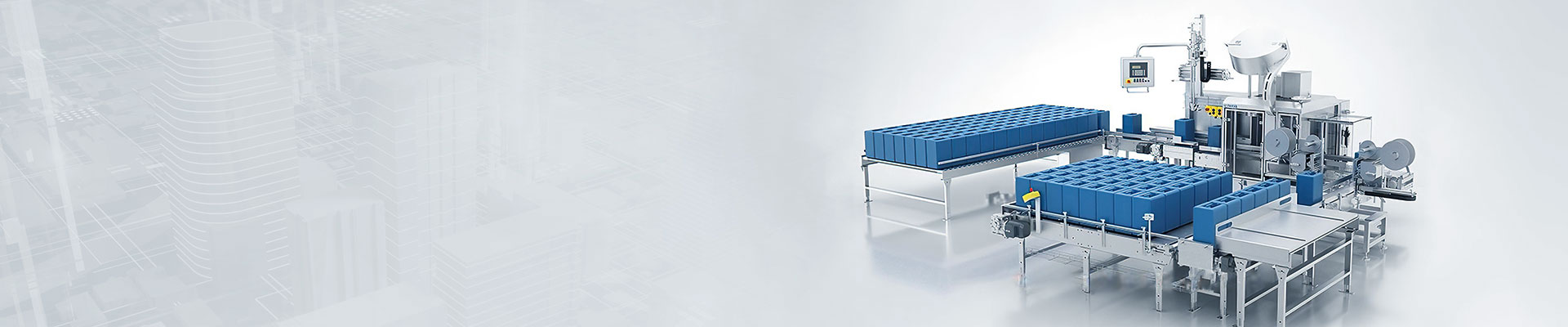
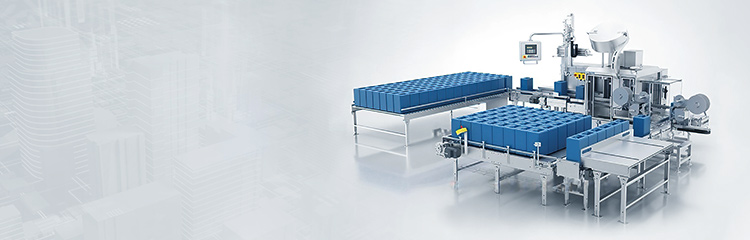
电动叉车秤为装载设备在装载过程中称量装载物料的一种称重设备。可以提供被称物料的累计值和打印清单。 称重系统是一种车载称重设备,与车载的机械控制部分集成为一体,在车载行进中实现称重。

叉车电子秤系统的网络拓扑结构其中包括:监控管理系统、电动叉车队列管理、称重主机、采样主机、实时监控、数据库服务器和其他在线工作站等。各单元称重系统之间通过厂内局域网联结在一起,实现数据共享。
称重系统要采用严格的分级管理技术,操作口令和智能卡验证网络权限设计,双重认证,有效地避免非法越级操作,各级的管理通过客户的要求来定义。
对于所有的数据文件都有保护措施,对于数据的建立、修改、删除以及查询都应有授权,以防止对数据的非法操作;对于原始数据的修改及删除均有日志文件进行记录以便日后核查。
为了保证叉车称重的各种环境中测量精度,一般在叉车称重的应变片桥路中增加线性补偿、零点补偿和温度补偿等处理,以及传感动态设计等。同时为保证传感器远程激励时的精度,一般在应变片的激励两端再输出两根导线至称重仪表,用于计算激励电压在长线传输时的损失补偿,在调校或更换数字称重传感器,数字称重仪表,直接在称重仪表进行调校,无需通过接线盒调校角差,大大提高了称重定期检测维修的简单性及取保商业计量的准确性。
叉车在不影响称重的的情况下,能快速检测出超重货物,并通过配套的电子显示牌及称重仪表、标志引导超重进入接受进一步复查和处理,从而实现不影响正常称重数据保存,实现不停车超限检测,预检后超载的才提示复检,实现检测与称重的融合。通过RS一485总线与中控室实现通信,既可独立控制,又可实现PLC联机控制。由计算机、称重模块和外围设备组成,作为整个系统的人机界面。完成全部系统参数设定、过程监控、数据记录。
技术参数
最大称量:2000kg,3000kg,5000kg
最小称量:1kg,2kg,2kg
精度:±0,1%
计量部分:电子秤显示仪表和传感器
使用电源:6位LED显示
选择事项:电动叉车专用打印机(RS-232C)