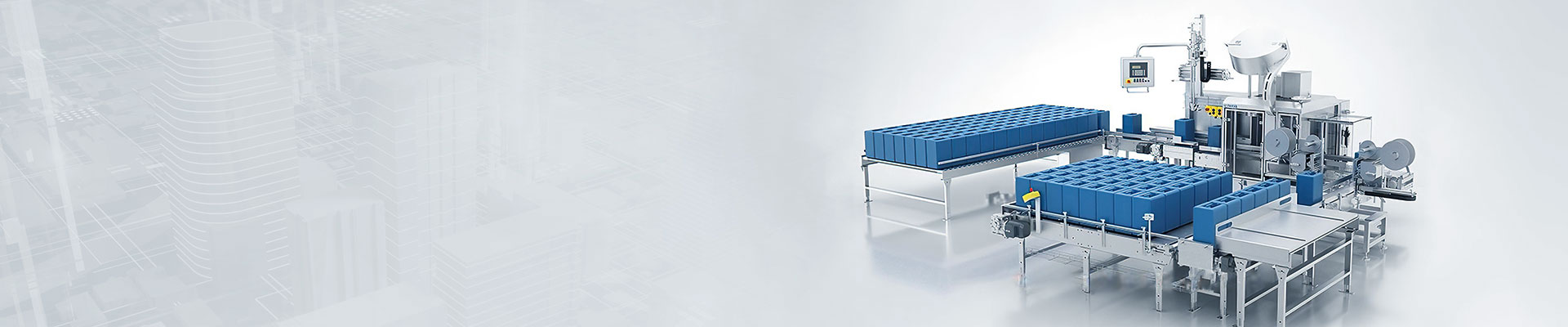
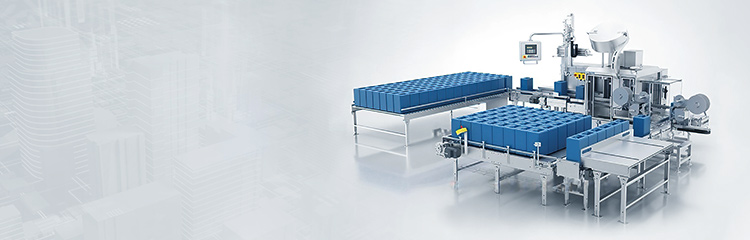
分选称进行生产过程中的成品检重,通过重量检测,亦可判断出成品的数量、漏装和错装,以及对合格品、欠重品、超重品进行分别统计,以达到产品质量控制的目的。当被检的进过秤台时,被检物品在秤台上会有短暂的稳态过程,通过判断被检物品的稳态重量是否在其设计的重量范围内。称重控制器通过指示灯给出检测结果,并给出后序流水线相应的执行动作。

分选机实现物料生产过程先进的实时数据控制,企业各个部门的生产调度、生产过程、设备、物料、质量和人员的全面管理与控制,为企业搭建一个可扩展的生产管理信息化平台,使得生产过程透明化、高效化、柔性化、可追溯化、事中控制、高客户满意度、低成本运行。同时,项目以智能化分选装备为基础,数字化物料生产过程,并应用网络技术和信息化技术,集成基于大数据的智能化分析与决策支持算法,实现了物料生产过程的智能化分析和管控。
通过设置各类终端和过程数据采集接口,建设高速的车间管理网络,实现物料信息、人员信息、设备运行过程数据、质检数据、制造环境数据的高效、快速采集,将产品制造流程中的“人、机、料、法、环”信息自动地进行集成和关联,实现制造指令的下达、制造执行过程中管控与制造执行进度状态反馈的高效协同。由此加强对生产过程的正向管控与反向问题追溯与定位,不断优化生产管理的组织和协调,提高生产效率,降低生产成本,提升产品品质,增强对市场的响应能力。
分选秤通过气路板进行气源分配结构紧凑采用集成技术,为客户订制了一种类似于气路板性质的元件:在两块铝板之间是一块塑料板,塑料板上包含所有的进气管线,各进气管线连接至相应的气动元件。完成配送中心拣选、分货、分放作业的现代化设备,是开展分选、配送作业的强有力的技术保证。具有很高的分选能力,能处理各种各样的货物。
检重秤可与各种包装生产线以及输送系统集成,主要用于在线检测产品重量是否合格,包装内是否缺少部件。或按照物品的不同重量输送到相应的重量范围区域中去。一般由控制装置、计量输送机、剔出装置及分选道口组成。控制装置的作用是识别、接收和处理分选信号,根据分选信号的要求指示、按商品品种、按商品送达地点或按货主的类别对商品进行自动分类。这些分选需求可以通过不同方式,如可通过条形码扫描、色码扫描、键盘输入、重量检测、语音识别、高度检测及形状识别等方式,输入到分选控制系统中去,根据对这些分选信号判断,来决定某一种商品该进入哪一个分选道口。
分选秤的作用是根据控制装置发出的分选指示,当具有相同分选信号的商品经过该装置时,该装置动作,使改变在自动检重秤上的运行方向进入其它输送机或进入分选道口。计量检重秤的种类很多,一般有推出式、浮出式、倾斜式和分支式几种,不同的装置对分选货物的包装材料、包装重量、包装物底面的平滑程度等有不完全相同的要求。
产品特点
全自动式选别方式(推出式、喷气式、摆臂式),免除人为错误。
友好的操作界面,功能可按要求定制。
采用*的数字式称重单元,实现高速稳定计量。
故障自动检测报警,掉电自动保护。
零点自动分析和特殊的跟踪处理技术。
强大的数据统计存储功能,可以存储数百个产品数据,记录几十万条数据记录。
随时都可以修改参数,而不需重量选别机暂停分选。