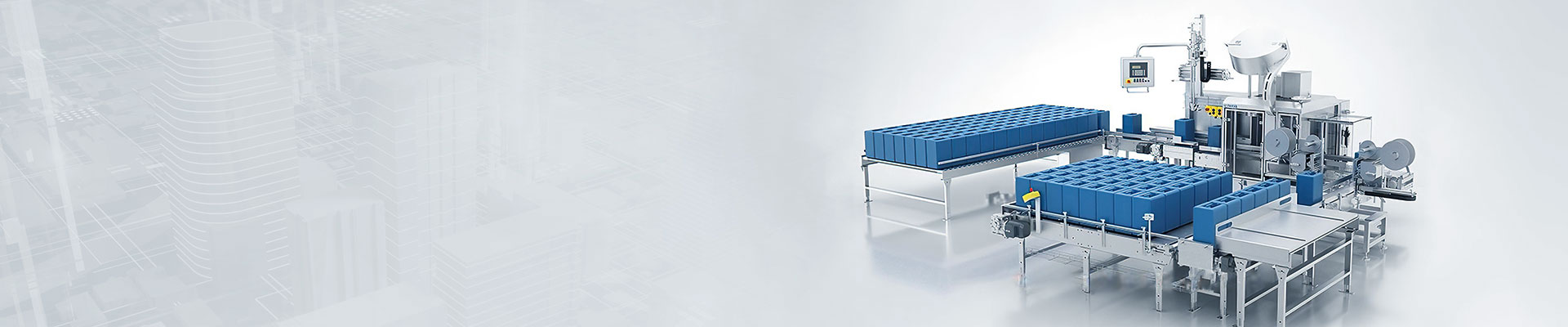
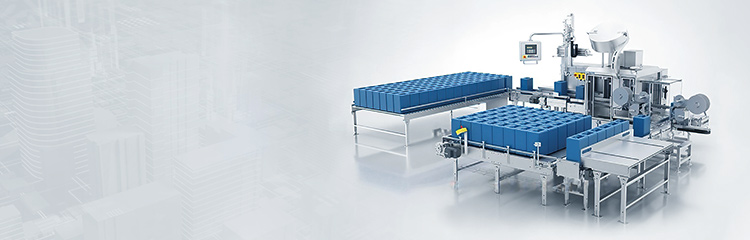
自动配料系统统以原有称重模块结合称重仪表构成的电子称重为基础,以现场总线通讯方式结合现有的外围执行设备完成对从料仓出口开始到混合机出口的配料输送混合的全过程的自动控制。配料系统对整个系统的报警提示、联锁进行显示和监控,并完成配方管理、生产数据管理、设备运行状态管理和指挥生产的人机对话来满足生产对混合料的配料要求。

投料系统采用主从式结构。以工控机为上位主机,以西门子PLC、变频器和称重仪表为下位从机。主机处于主导地位,实现对各从机的通信管理和控制,将工控机的RS-232异步通信口经电平转换后与PLC相连,形成上、下位机通信的一个物理通道;将主机的另一个RS-232口和称重仪表的通信口相连,构成第二个物理通道。上位机采用轮询方式,逐个与从站通信。上位机把任务规划的结果传送给PLC,在PLC进行控制的过程中,上位机使用上位机连接命令监视下位机的运行状态和数据区内容,实时读取PLC的内部状态以及称重仪表的实时数据,在上位机上显示。
自动配料系统由工控机、PLC、工业称重仪表、变频器、振动电机、混料机、称重模块、传送带等部分组成。上位工控机提供人机交互界面,完成控制信息输人、数据管理、进行数据显示、存储、统计和报表等功能,上位机采用IPC810工控机,主要工作如下:工控主机首先根据操作人员的指令,读取某个编号的配方,然后,根据配方中配料的比例及先后顺序,向PLC发出开始配料的指令,使得PLC能够起动特定的变频器。在配料过程中,工控主机以轮询的方式,一方面实时读取PLC的状态字,了解PLC及PLC下级设备的运行状态;另一方面实时读取安装在配料机上的称重仪表的称重数据,按照配料策略,当称重接近配方中的设定值时,主机向PLC发出停止本次配料的指令。当一个配方上的所有材料都配完后,整个配料过程暂停,等待操作人员的指令。
上料系统具有如下功能:
①全自动配料,在设定好配方之后,自动按照配方称重配料,无需操作人员干预;
②具有报表功能,可以产生日报表,实时报表和月报表、年报表等;
③动态增加和修改报表,系统通过设定权限,赋予技术人员或操作人员修改,增加配方的权利,同时记录该次修改的日期和操作人员编号;
④断电恢复功能,系统能够在突然断电的情况下,恢复断电前的测量记录;
⑤局域网共享功能,主机在局域网内可以共享数据,方便车间主管了解工程进度和其他情况。