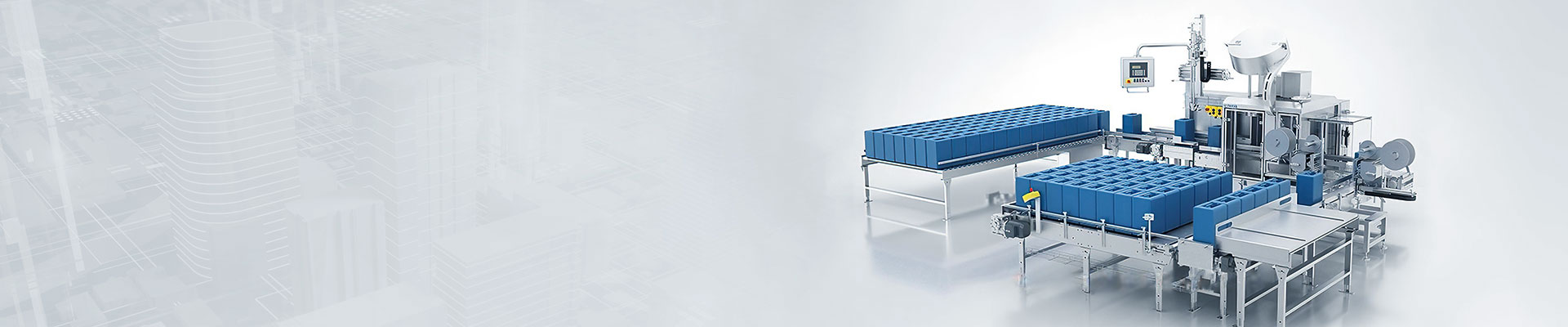
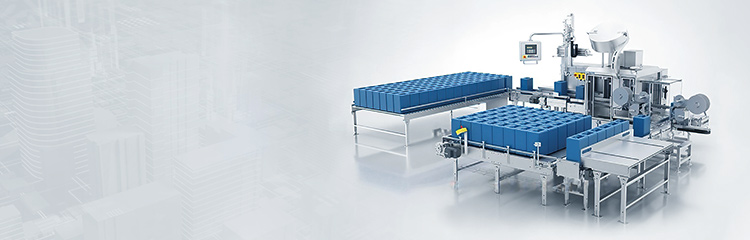
Batching scales in order to control personnel directly and accurately weighing data of raw materials, the production process can not be a small amount, lack of material, loss of material. To realize the manual or automatic to select the bin number location, the bottom line of the various dosage inventory for automatic alarms and other functions, the digital display of the electronic scales and the PLC and touch screen for information exchange, all system control will be brought together in a special system software, the controller only need to click on the appropriate location to control such as electrical switches, rotating transport components, water, gas valves, etc., the human-machine interface is very good! The human-machine interface is a good way to display the whole production line in the form of dynamic and static diagrams on the computer screen, so that the staff can understand the operation of the whole production of ingredients without leaving home.

The batching machine accomplishes the weighing and proportioning of the main material and various ingredients. After mixing and blending the ingredients, it carries out grouping and classification of dosage, realizing the measurement of dosage scales. S7300 PLC is adopted to form the data acquisition and control system. Sealed junction box is adopted at the batching site, which is dust-proof and moisture-proof, and can ensure reliable signal transmission. The instrumentation adopts special industrial process controller, which is controlled online through PLC, and the signal detection of each valve position and unloader position adopts load cell, which is non-contact, anti-interference, dust-resistant and moisture-resistant. The silo level adopts heavy hammer type material level meter, which can realize continuous silo level detection.
The loading system has the functions of human-computer interaction, communication, display, storage and printing, etc. The Weighing system also has the functions of data and graphic display, status monitoring, data input, information storage and other relevant operation screens. The system can realize real-time process data monitoring, simulation display of process flow, real-time data record access, system operator privilege setting, process parameter setting, setting alarms for running process events and switching between manual and automatic control. In the monitoring system, the on-site control instrument displays real-time flow rate, load, totalized value, temperature and so on. Temperature indication through the field temperature display instrument, pressure indication through the field pressure display instrument and motor current through the field display instrument is transmitted to the centralized display in the control room. The frequency converter regulation is equipped with automatic switching switch, communicating with the main control computer, 10-inch screen weighing and batching instrument and monitoring and recording real-time data. In the automatic control mode, click the automatic dosage button in the screen. If the system detects that the dosage valve of a scale is not closed, an alarm will be generated and it will enter the pause state. Each scale has an advance quantity according to the weighing speed. When the control instrument detects that the weighing weight of the scale reaches the set value, the advance quantity will be subtracted and the control instrument will close the feeding valve. The advance amount can be corrected manually or automatically, so that the control instrument can control the dosage scale to reach the set target value every time the dosage accuracy.
Batching scales in order to control personnel directly accurate raw material weighing data, the production process can not be a small amount, lack of material, loss of material. To realize the manual or automatic to select the bin number location, the bottom line of the inventory of a variety of ingredients for automatic alarms and other functions, the digital display of the Electronic scales and PLC and touch screen information exchange, all system control will be brought together in a special system software, the controller only need to click on the appropriate location to control such as electrical switches, rotating transport components, water, gas valves, etc., the human-machine interface is very good! The human-computer interface is very good at displaying the whole production line in the form of dynamic and static diagrams on the computer screen, so that the staff can understand the operation of the whole production ingredients without leaving home.