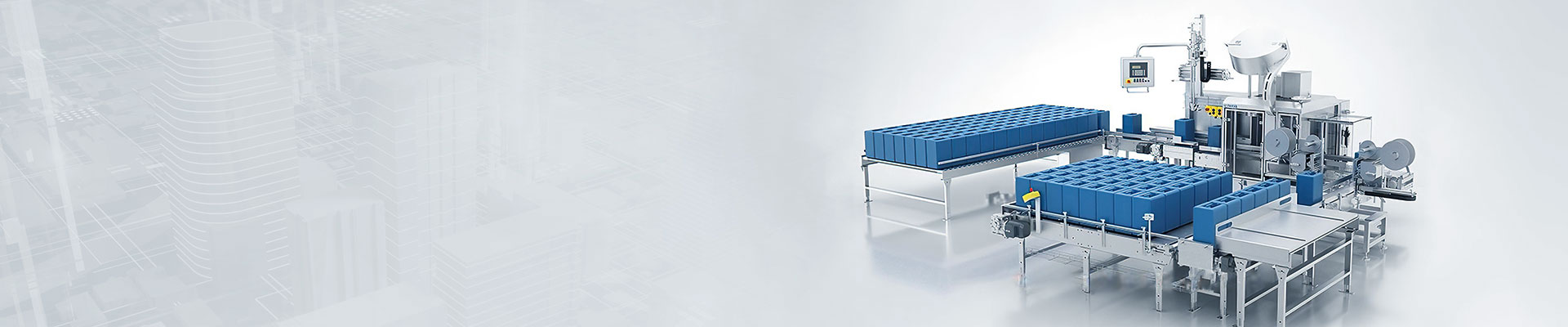
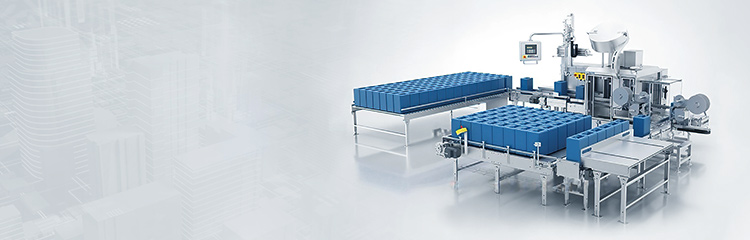
称量混合设备通过将计算机技术与传统的继电器控制系统有机结合,在配料过程中,PLC主要负责接收外部的开关信号,以此来判断当前系统的运行状态,并输出各种控制信号,控制接触器、继电器、电磁阀等部件进行相应的动作。根据具体的配料过程,在配料开始时,电机正常运行,给料系统高速下料,在物料重量接近目标值时采用PLC点动控制模式进行点动下料,从而保证物料计量精度的要求。

投料系统采用西门子 S7 系列 PLC,CPU 使用高性能的 315-2DP 型处理器,以确保配料控制系统的稳定性和快速性。基础自动化部分包括称量混合设备。称量混料机由一台 S7-300PLC 组成。主站和各远程 I0 站采用 PROFIBUS 通信网络,以保证控制系统可靠、及时、高速地通信。称量混合机同时还和过程配料级计算机相连,接收过程配料级的指令和管理信息,并向上传送现场装置的实时运行数据。
I0站直接与现场的各类装置相连,进行监测和控制,其中完成设备自锁、启动、停止等信号的采集和控制输出,以及地仓各种物料的配料调节。完成螺旋秤、给料机等设备自锁、启动、停止等信号的采集和控制输出,以及贮灰罐各种物料的配料调节。
配料系统平台是 Simatic WinCC,软件实现以下功能:
(1)工艺流程总貌及设备运行状态显示配料程序画面动态显示工艺流程图、运行设备的工作状态,供操作人员了解系统生产状况。
(2)工艺图的切换
配料程序提供各个工艺子系统的图形界面,通过按钮可以切换至不同的界面,来展现各个生产工艺部分的生产实际情况和相关信息。
(3)控制方式的选择
称重控制系统提供两种远程控制方式:自动控制方式和手动控制方式。可在配料程序界面上通过选择按钮设定。手动操作方式作为自动控制操作方式的一种补充,为控制系统的人为介人提供了灵活性。
(4)参数设置
根据生产工艺的变化要求,在线调整控制参数。
(5)实时趋势显示
配料程序提供了生产工艺参数实时趋势曲线的显示,通过选择按钮,可以显示不同趋势曲线,从而了解生产状况。
(6)报警处理
设备出现故障时,系统将通过报警画面提示操作人员,在报警窗口中提示详细的故障信息,同时将该信息打印出来。