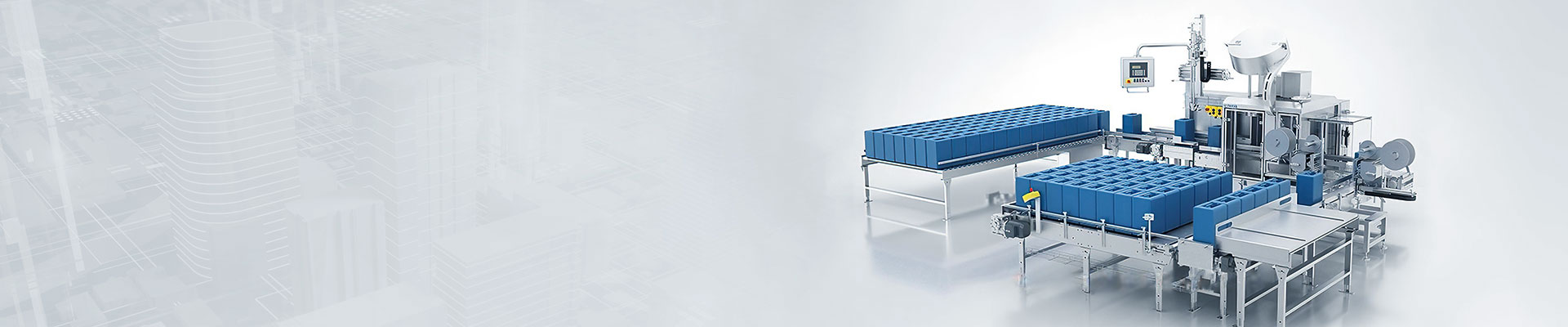
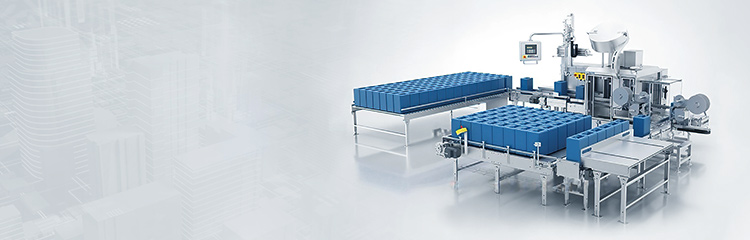
Electric forklift electronic scale refers to all kinds of wheeled handling vehicles that carry out loading and unloading, weighing, stacking and short-distance transportation of pallet goods. ISO/TC110 is called electronic scale industrial vehicle. Belonging to a material handling and weighing machine. Widely used in stations, ports, airports, factories, warehouses and other national economic departments, it is an efficient electronic scale weighing equipment for mechanized loading and unloading, metering, stacking and short-distance transportation. The forklift electronic scale is a widely used weighing machine for lifting, loading, unloading and transportation, which is widely used for loading, unloading, stacking, weighing and short-distance transportation of finished goods in ports, docks, warehouses, freight yards and industrial and mining enterprises.

For a long time, the forklift truck was only a tool for lifting and transporting goods. In order to weigh the goods in the lifting and transporting process, the electric forklift truck was equipped with a weighing console, and the weighing instrument was installed on the console. The data lines of the weighing sensors installed at the lower parts of the two fork support legs were connected with digital instruments. When the elastomer with digital weighing was subjected to the force from the stress direction (such as the gravity of goods), the elastomer produced corresponding slight deformation. It is transmitted to the digital weighing instrument through the force transmission mechanism. The gravity signal output by the sensor is amplified and filtered, and then sent to the A/D converter to be converted into a digital signal. The weight value is calculated by the microprocessor according to the mechanical mathematical model, and the weighing data is prompted to be read when the forklift mast is vertical. The digital weighing LED displays the results, and the real-time data is uploaded to the computer control room by the weighing instrument wirelessly. Now it is widely used in short-distance transportation and warehousing of goods in stations, docks and large and medium-sized enterprises. With the development of market economy, the position and role of logistics in economic development is becoming more and more obvious, and the weighing popularity of battery forklift is getting higher and higher, which makes forklift have multiple functions of handling, lifting and weighing, thus greatly improving the working efficiency and warehouse management level.
In order to ensure the measurement accuracy of forklift weighing in various environments, linear compensation, zero compensation and temperature compensation, as well as sensing dynamic design are generally added to the bridge circuit of forklift weighing strain gauge. At the same time, in order to ensure the accuracy of remote excitation of the sensor, two wires are generally output to the weighing instrument at both ends of the excitation of the strain gauge to calculate the loss compensation of the excitation voltage during long-distance transmission. When adjusting or replacing the digital weighing sensor and the digital weighing instrument, it is directly adjusted in the weighing instrument without adjusting the angle difference through the junction box, which greatly improves the simplicity of regular inspection and maintenance of weighing and the accuracy of commercial measurement.
The forklift Electronic scale adopts sealed junction box, which is dust-proof and moisture-proof to ensure reliable signal transmission. The weighing instrument adopts special industrial process controller, and communicates with the central control room through RS-485 bus, which can be controlled independently and online by PLC. It is composed of computer, weighing module and peripheral equipment, which serves as the man-machine interface of the whole system. Complete all system parameter setting, process monitoring and data recording.
technical parameter
Maximum weighing: 2000kg, 3000kg and 5000kg.
Minimum weighing: 1kg, 2kg, 2kg.
Accuracy: 0,1%
Measurement part: electronic scale display instrument and sensor.
Power supply: 6-bit LED display
Option: Special printer for electric forklift (RS-232C)