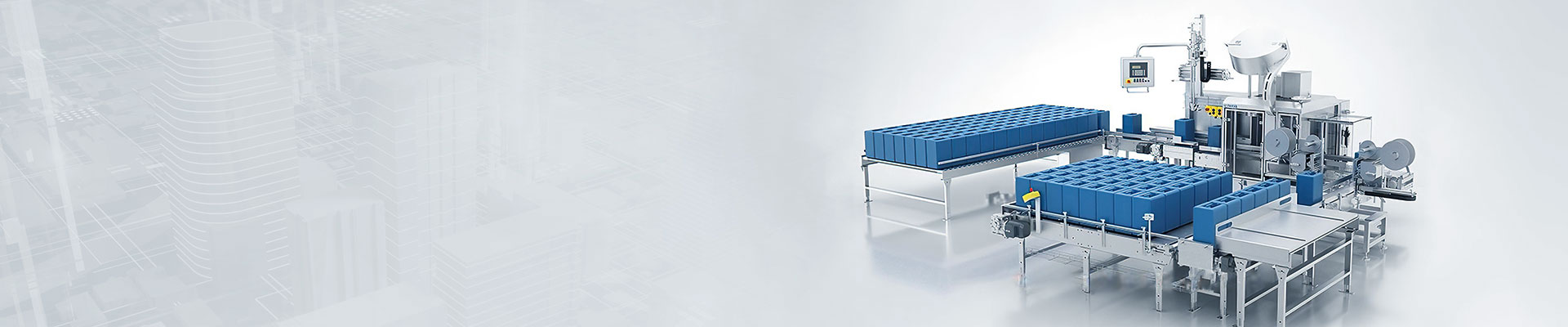
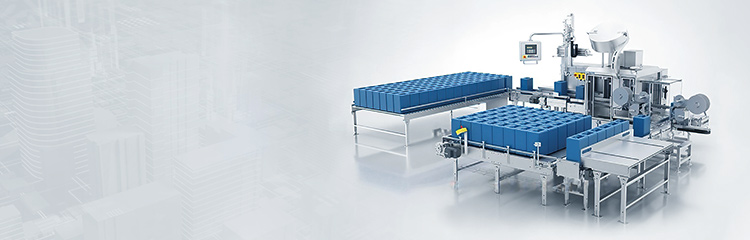
称重混料设备结构由高位料仓、阀门、振料电机,称重模块和反应釜,以及一套位置检测装置组成。在加料等待阶段,移动桶停在电子秤上及反应罐加料口位置上等待控制命令。根据操作人员输入的加料参数,料仓阀门开启下料。通过电子秤不断地采集进料量,当达到加料设定值一提前量时关闭阀门,提前量可由阀门的时间计算或根据经验获得。当所加物料到达指定重量时自动关闭阀门。

自动配料系统采取由上位机一工业电脑,下位机-PLC可编程序控制器,粉体配料,液体配料,微量加料及控制系统等部分组成。本控制系统是以真空上料,加料螺杆定量加料,称重料斗自动称重配料,同时进行累加称重的一种自动称重系统。适合于物料的精确计量和生产过程中的自动配料作业。
称重混料机结构由高位料仓、阀门、振料电机,称重模块和反应釜,以及一套位置检测装置组成。在加料等待阶段,移动桶停在电子秤上及反应罐加料口位置上等待控制命令。根据操作人员输入的加料参数,料仓阀门开启下料。通过称量模块不断地采集进料量,当达到加料设定值一提前量时关闭阀门,提前量可由阀门的时间计算或根据经验获得。当所加物料到达指定重量时自动关闭阀门。
自动上料系统组成
1、配料机主要完成粉体和多种液料的配料混合,计量罐单独设置,液体原料分开计量加料,每个原料罐底部都安装有送料管道,分别由自动阀门和手动阀门控制开关,每种液料的自动阀门安装在靠近管道出口位置,由送料泵负责将料通过管道打到计量罐,送料泵两端预留回流管与回流阀,在计量罐进料口处的安装自动阀门,实现物料的快投和慢投料控制;液料或粉体通过管道可直接加进计量罐,计量罐的四个支撑底脚与支撑架根底之间各安装称重模块,负责计量进入计量罐的物料重量。
2、通过计量罐底部的的自动分流装置,分别自动加到相应的搅拌罐中,在计量罐的总卸料阀后水体平安装到各个搅拌釜的分料自动阀门,把各个分料自动阀门的前端进料管用管道联通,这样可以保证卸料后根本无存料,到各个搅拌釜的卸料管道粉体和液料管道可以合并一条管道,以减少管道用料本钱。搅拌好的成品通过反响釜底部的管道泵送至成品罐,由自动阀门和泵控制。
3、全部配料数据均存储于控制中心的工控机数据库内,配料过程均由组态软件实施监控,通过控制界面实施过程操作,生产数据适时存储到系统数据库,以完成对各种生产数据进展存储和分析,同时还能实现原料进存用料管理、成品管理、人员管理、合同管理等各项功能。