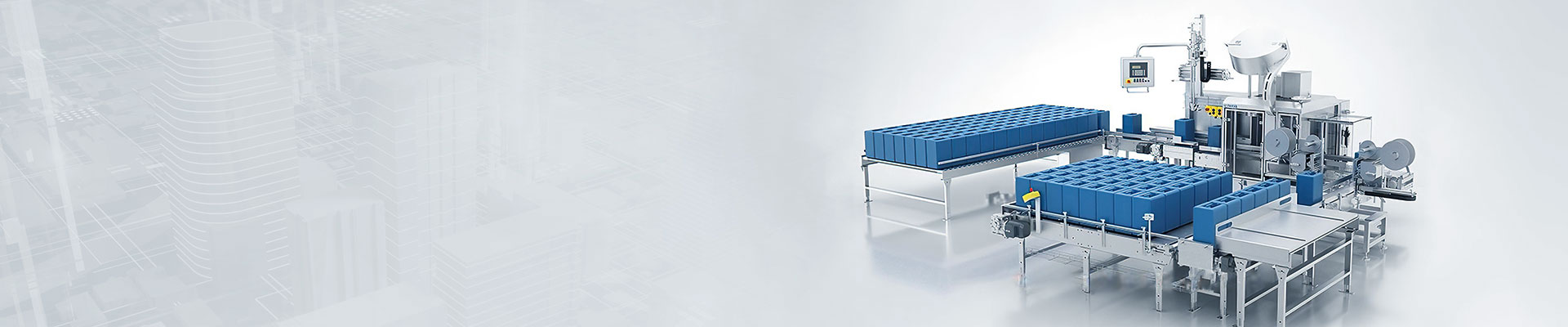
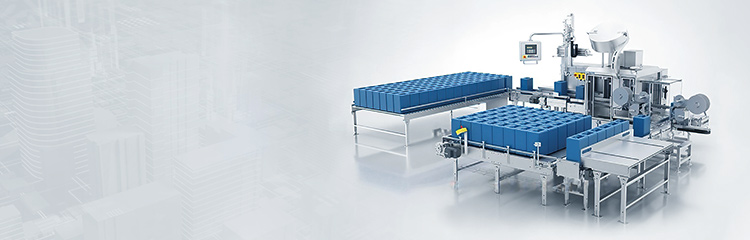
The weighing scale acts linearly on the weighing module through the weighing frame, and the velocity sensor measures the speed of spiral operation. The instantaneous flow rate of the material can be measured after calculation. The instantaneous flow rate and cumulative flow rate are displayed after calculation, and the instantaneous flow is sent to the computer system as an input signal with 4~20mA analog current signal at the same time. After comparing the signal with the set value, the computer outputs 4~20mA analog current signal to control the speed of the feeding motor through the inverter, which realizes the closed-loop control of the material discharge flow.

The weight of the material on the batching machine acts on the weighing module linearly through the weighing frame, so that the strain body in the load cell produces micro-strain, and then the resistance of the resistance strain gauges of each arm of the bridge affixed to the strain body changes, and under the excitation of the voltage supplied to the bridge, there will be the output of the unbalanced potential, and at the same time, the speed sensor measures the speed of the helix, and the two signals are sent into the microcomputer accumulator through a series of arithmetic calculations, which can measure the instantaneous flow of the material. The instantaneous flow of material can be measured, in the system accepts analog signals from the weighing module and motor frequency conversion speed control, after calculation, display the instantaneous flow and cumulative flow, and at the same time will be the instantaneous flow of 4 ~ 20mA analog current signal to the computer system as an input signal, the computer will be the signal and the set value of the comparison of the output of the analog signal of 4 ~ 20mA analog current signal through the frequency converter to control the feeding motor speed, to achieve the material under the material, and to achieve the material under the material, and to achieve the material under the material, and to achieve the material under the material, and to achieve the material under the material. The rotational speed of the feeding motor is controlled by the frequency converter, which realizes the closed-loop control of the material flow.
The feeding system is composed of inlet dome valve, exhaust dome valve and fluidized air pipeline; the outlet feeding station is composed of inlet dome valve, exhaust valve, outlet dome valve, fluidized air pipeline and post-pump make-up air pipeline; each feeding station is designed with a high material level meter in the pump, and the pipeline between the pumps is designed with a make-up air pipeline between the pumps; on each inlet pipeline, there is a throttling orifice plate used for adjusting the amount of air; on each inlet pipeline, there is a backstop valve used for airflow and In each inlet pipe, there is a backstop valve for air flow and preventing ash backflow.
Prior to operation of the mixer and when other conditions are met, all inlet dome valves 'open' when the cycle interval time is reached or when triggered by a low level of ash in the ash hopper by 'energizing' the corresponding solenoid valve coils. Since the exhaust valves use the same pneumatic control valve as it, the exhaust valves also open at the same time. By gravity, the accumulated ash in the ash hopper falls into the mixer. When the fall timer arrives or the mixer level meter triggers a signal, after a delay of 2 seconds, all inlet valves and exhaust valves are 'closed' after 'de-energized' by the corresponding solenoid valve coils. When all the inlet and exhaust valves are closed and send back the sealing signal, the main conveying air valve and all the fluidizing air valves are 'opened' after being 'energized' by the corresponding solenoid coils, and the conveying air enters into the conveying silo through these two pipelines respectively. When the conveying pressure is lower than the set end pressure (0.03MPa), after a delay of 20 seconds, the main conveying air valves and fluidizing air valves of all feeding stations are de-energized by the corresponding solenoid valve coils, and the conveying is finished. When the conditions are met, a new conveying cycle starts.
Main functions of automatic Dosage system
1)Monitoring function: detect and monitor the instantaneous flow, daily total, monthly total, yearly cumulative amount and other parameters of the weighing process.
2) Screen display: through the computer monitor can display the operating parameters of the control parameters in the dosage process, as well as display the real-time dosage curve and table.
3)Printing management: dosage report can be printed at any time for saving and inquiry.
4) Communication function: two-way data and information exchange can be carried out between PLC and meter.
5)Data processing: the system can automatically process the collected signals and output them to the corresponding control quantity.
6)Control function: according to the corresponding set value before operation, it can automatically control the normal operation of the equipment, including PID adjustment.
7) Alarm function: The host computer alarms various parameter abnormalities or equipment status in screen mode and sound and light signal mode.