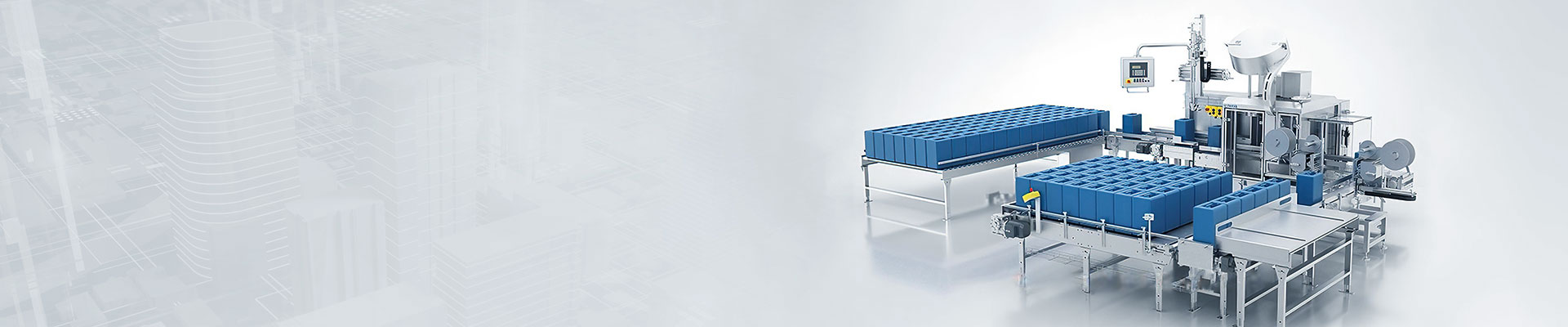
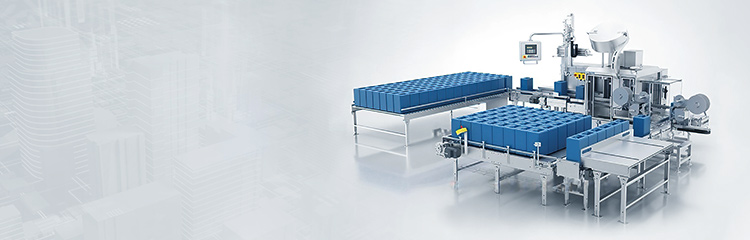
自动化配料系统作为中央控制区来完成称重加料的全过程,在配备之前工作人员开启加开关,PLC中央控制区发出信号,启动相应的电磁阀注入物料到反应釜中,与此同时称量模块开始工作。当反应罐的量增加到与定量设定指所设定的重量等值时,中央控制区接收到称重模块的动作信号,立即使加物料的电磁阀关闭,停止加物料。

自动配料系统主要应用于干燥粉末及颗粒产品以气流为载体的输送,是一种借助空气在密封管道内的流动来输送固体物料的新技术。一般来说,气流为普通空气,但在一些特殊状态下干燥的,冷却的,加热的空气或惰性气体如氮气也可以作为输送气流。用于干燥粉末及颗粒产品,以气流为载体的输送。一般来说,气流为普通空气,但在一些特殊状态下干燥的,冷却的,加热的空气或惰性气体如氮气也可以作为输送气流。按照这个基础结构,产品(固体颗粒)在混入气流后由气流携带通过一定长度的管道。该管道与上料系统或旋风分离器相连接将气体和产品分离。
气力输送包括四个组成部分:
1.源动力-鼓风机、螺旋风机、压缩机、抽风机或真空泵,用于产生气流。
2.供料器-旋转阀、文丘里管、螺杆上料器、风管或其他供料装置,在控制下把颗粒加入气流中。
3.输送线-直管、弯管和分流阀。
4.分离器-旋风分离器、上料器、过滤、上料器或筒仓/管道,将颗粒与气流分离。
气流称重系统有两种方式:
1.稀相输送(疏相流)-气流量高,产品输送量低,颗粒含量少,质量流比大约为0-15,产品悬浮于气流中。负压-0.5bar至-1.0bar
气流称重上料机优点:
a正压气流输送系统或气运系统是以鼓风机(如罗茨风机)输出的气流为载体将散装粉粒物体物料卸入管道进行压送,稀相正压气力称重配料系统的正压值小于0.15Mpa,气固比为5~20,正压气力配料系统能力可达到60吨/小时(单条风运线)且输送距离能达到400米。
b负压风送系统或负压风运输送系统是真空泵(如罗茨或水环)产生的真空将散装粉粒体物料用负压气流吸送到指定的设备,负压气力计量配料系统系统的负压值小于0.06Mpa,气固比为1到15,高真空气力由接受罐,过滤装置和真空泵组成,真空泵将物料吸进接受罐,气体经过滤后排出,物料则落入接受斗中,属于负压高浓度气力输送方式,具有输送距离较远(<60米),气固比为2~8的特点,负压气力具有送料连续均匀,可输送用压送式难以供料如垃圾,木片,细长纤维等,可实现由数处向单一集中输送并具有一定的混合功能。同时风送系统能力可达30t/h(单条输送线)。
管道内颗粒相对于气体的浓度是一个非常重要的指标,称为相对密度或质量流比,是颗粒量与气流量的比值。有许多的配置和因素需要考虑。为了确保正确而有效输送系统的设计,选择配件也是至送重要。
气力输送系统特点:
1.低保养,低人工,低成本-输送线封闭光滑管道组成,没有机械运动部件。
2.布线灵活-相对于皮带/螺杆/托链输送来说,气力输送的管道的布置可垂直,水平,弯管并可穿越狭小空间。通过分流阀分配产品到多个输送点以及从多个供料点提取物料的方式可以更简单和更易于实现。管线易扩展或今后重新布线使用。
3.通用性-一套配料系统可以在不同时刻输送不同种类的产品,实际上所有的粉末和颗粒都可以由气力输送。
4.洁净的内部系统具有很多益处:输送不同物料时不会有交叉污染,危险产品和贵重物品,保健品,食品和药品都可以通过密封控制系统来输送,在某些需要特殊控制的环境里,气体可以密封并在系统中循环使用。