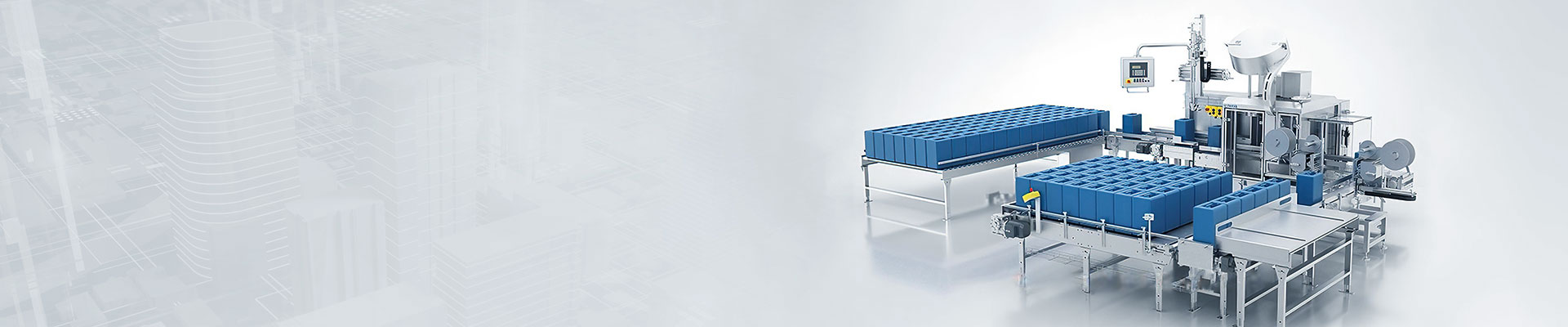
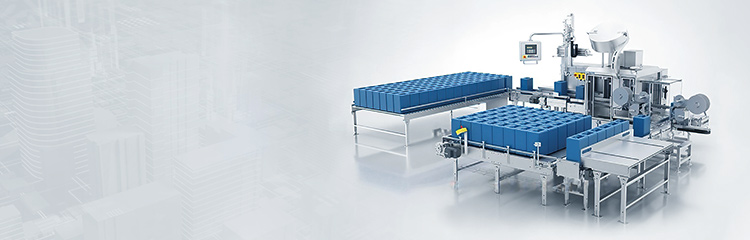
Reduction scale according to the recipe requirements in a number of silos to complete the measurement of a variety of materials under the dosage, to each discharge port automatically unloading, you can realize the receipt of automation, the control room using industrial computer and PLC system, the entire state of the dosage in the industrial computer screen can be seen at a glance, the user can be manipulated at the scene of the entire production process, the scene does not need artificial, the system can also record and print the results of the dosage, print the daily, monthly statements, computer storage of up to 100 formulas, the computer can store up to 100 formulas, and the dosage of the dosage. The system can also record and print the results of each dosage, print daily and monthly reports, and store up to 100 recipes in the computer. Target value setting and dosage control can be operated by touch screen panel, or can be controlled and managed by DCS system commands.

Reduction scales take the hopper scale and the feeding mechanism as the whole scale body, through the weighing instrument or the upper computer constantly samples the weight signal of the scale body, calculates the ratio of weight change per unit of time as the instantaneous flow rate, and then through the processing of all kinds of software and hardware filtering technology, it arrives at the "actual flow rate" which can be used as the object of control.
Reduction scales are mainly composed of hopper scales, feeding Feeders, weighing feeders and suspension devices. The control part mainly consists of Weighing modules, signal amplifiers, input and output interfaces, host computer (host computer) and so on.
The dosage process of subtractive scale is divided into two stages: feeding and unloading. After the dosage starts, the weighing feeder is started firstly, and the controller detects and samples the weight of materials in the hopper scale, and stops feeding when the weight of materials in the hopper scale reaches the upper limit value set for dosage. At the same time, the controller detects and samples the material weight of the hopper scale, and stops feeding when the material weight of the hopper scale (feeding quantity) reaches the upper limit value set by the dosage. In the unloading stage, the controller starts the weighing feeder to unload the materials in the hopper scale to the next level of feeding equipment to send away. When unloading, the controller detects and samples the weight of the material in the hopper scale, and when the weight of the material in the hopper scale reaches the lower limit value set by the dosage, it will re-feed the material to the hopper scale. However, after the second feeding phase begins, the weigh feeder continues to unload without stopping.
Subtractive scales continuously weigh the entire feeding system, including hopper scales, feeding mechanism, equivalent to a static scale; at the same time, through the frequency control to control the discharge flow of the feeding mechanism.
Subtractive scales hopper scales every unit of time the weight of the material to reduce the feed flow. Subtractive scale controller will be preset to feed the flow of comparison, and by adjusting the speed of the feeder to automatically correct, so you can maintain an accurate feed flow.
When the weight of material in the hopper scale falls below the preset value, the subtractive scale control module locks the feeder speed, keeping the downcomer mechanism feeding in a volumetric manner while opening the fill valve for rapid feed. When the weight of the material in the hopper scale reaches the high preset value, the charging valve will be closed automatically. At the same time, the subtractive scale controller automatically switches the discharging mechanism to the weighing mode of dosing.
Technical features
Subtractive scales have the characteristics of both static and dynamic scales. For the traditional dynamic weighing and measuring method, it has the characteristics of continuous weighing, realizing the high efficiency of the process, but it also has the problems of low system accuracy and high maintenance, etc. While the static weighing method, although it greatly improves the system measurement accuracy (up to 0.1%, or even higher), it can only satisfy the application of intermittent batch feeding (dispensing), and it cannot meet the requirements of modern process industry's high efficiency to the greatest extent. To meet the modern process industry's high efficiency and high output requirements. The emergence of subtractive scales, just both the advantages of the two, to make up for their shortcomings, the main advantages are:
1) High system accuracy
Subtractive scale work, the bin measurement is actually completed in the static state, and is in the feeding and discharging each measured once, according to the two working conditions measured the difference between the two weights calculated flow. The difference and the flow rate of the given value error can also be compensated in the next cycle, and these two weight measurement time in a few minutes to complete, there is no sensor zero drift and temperature drift and other effects. Therefore, the measurement accuracy can be quite high, the system measurement accuracy can reach 0.5%, or even 0.2%,.
2)、Totally closed structure, suitable for all kinds of bad site.
The feeding system is all steel, which is suitable for occasions with poor environmental conditions, and is characterized by robustness, low maintenance, and not afraid of high temperature materials.
Many industrial and mining enterprises are big consumers of electricity, so how to save energy is also a very important topic. As the subtractive scale adopts the fully enclosed structure, the dosing process does not produce dust, eliminating the need for dust removal devices, simple structure, without the need to match the spiral scale and other supporting, not only saves investment in equipment, but also saves electricity and improves production efficiency.
3)、Maintenance-free and simple calibration
As the subtractive scale is through the measurement of the weight difference to calculate the flow of material measurement, there is no such as spiral scales and other dynamic scales in the existence of zero drift (spiral run-off, sensor displacement, material impact vibration spiral slippage, spiral sticking caused by the impact of material, etc.), material adhesion, deformation of the scale body mechanical structure and other factors to ensure long-term stability of the system's measurement accuracy, basically do not need maintenance and a lot of calibration work. Calibration work.
According to its measuring principle, not only can it be physically calibrated, but it can also be calibrated online during production operation. That is, according to the hopper scale materials in the upper and lower limit weight difference and subtract the scale flow display value comparison calculation accuracy, this calibration method has a simple, convenient features, saving money and effort.