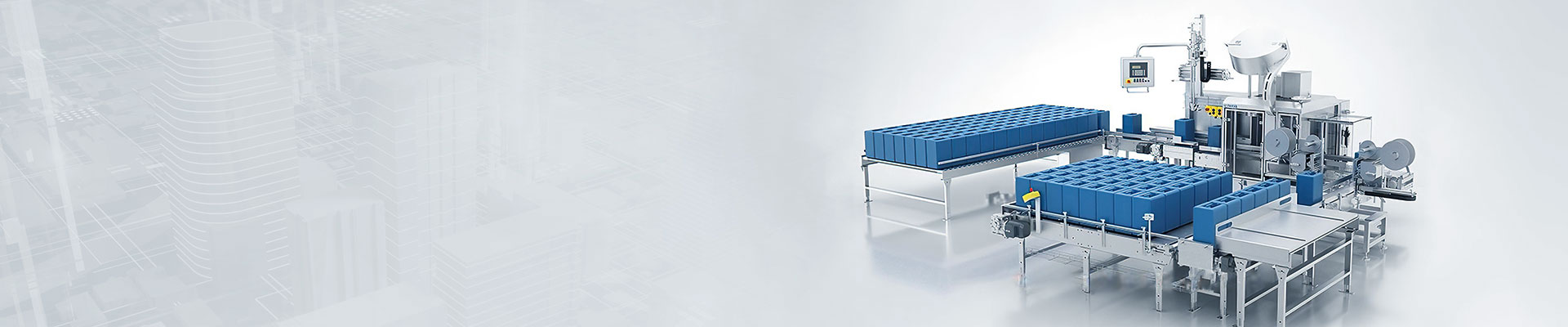
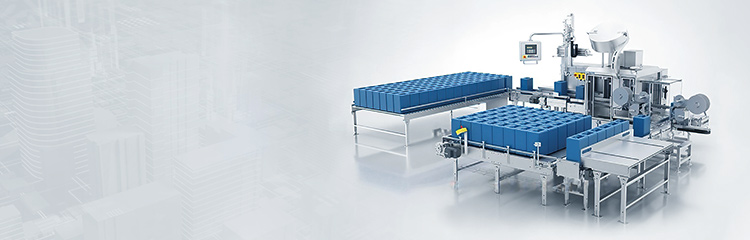
PRODUCTS
自动投料系统通过压力称重模块进行重量的拾取,并将拾取的重量信号进行放大、滤波后,进入A/D转换器进行模拟量到数字量的转换,然后送入单片机进行信号的分析、处理,其结果通过RS232C通讯串口输出到工业控制,同时根据信号的结果做出相应的反应并执行相应的操作。
Product details

投料系统主要通过电子秤实现整个系统的自动控制,主要完成自动送料、下料、运输、物料混合搅拌等功能。采用了工控机配料集散控制方式,是由一台主机和多台从机通过网络联结起来,主机将控制任务交给各个从机完成。
集散控制配料通过压力称重模块进行重量的拾取,并将拾取的重量信号进行放大、滤波后,进入A/D转换器进行模拟量到数字量的转换,然后送入单片机进行信号的分析、处理,其结果通过RS232C通讯串口输出到工业控制,同时根据信号的结果做出相应的反应并执行相应的操作。
配料过程和控制要求包括进料、物料运输、搅拌和下料。每个原料反应釜库都有完整的投料系统和下料系统,两者互不干扰。配料启动前,工作人员需要建立原材料配方和物料配比的程序。
配料启动时,进料系统将按照设定的程序进料,进料结束。原料反应釜下料时,物料通过检测物料流量是否达到设定值,当物料达到设定值时,关闭下料阀完成下料。
工序完成后,物料通过传送带输送到相应的中间反应釜。物料运输后,在中间反应釜中混合和搅拌物料。
中间反应釜混合完成后,物料通过卸料阀到达传送带,并通过传送带进入混合反应釜。
步骤结束后,物料到达混合反应釜,开始混合搅拌。搅拌结束后,卸料系统启动,物料通过卸料阀开始卸料。