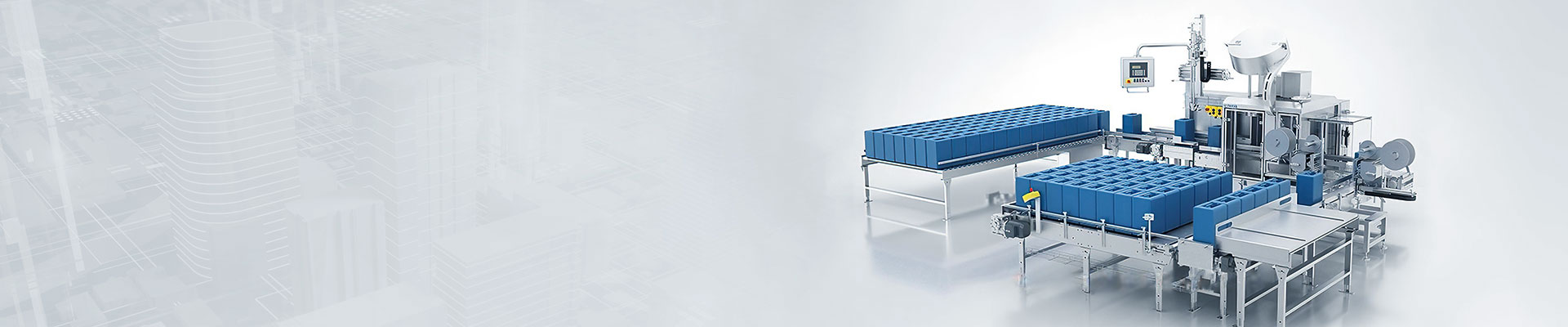
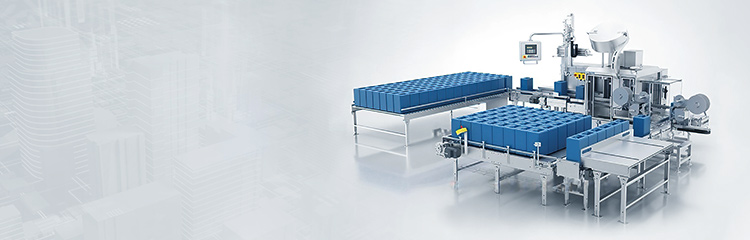
称重投料系统主要显示多个传感器及称重仪表,并输出多阶段控制信号, 用户可以直接访问PLC原料系统、终端控制系统,实现多阶段控制和自动控制。按照预先确定的配方,把各种不同的原料按比例进行混合,为了提高配料的精度和速度,保证产品的质量和增加产量,采用了微机控制技术。微机控制的配合生产线。

称重喂料机由两部分组成,一是秤体部分:包括料仓、秤架、螺旋、负荷称重模块、测速传感器、交流或直流驱动电动机及藏速机等。二是称量仪表部分:包括称重仪表、交流或直流调速设备及接门电路等。多喂料配料机有的把各台电子称分别接人工厂的计算机集散控制系统进行集中控制,现场仪表的模拟量信号与计算机的信号传输、连接智能现场设备和自动化系统的数字式、双向传输、多分支结构的通信网络。
称重喂料系统主要显示多个称重传感器及称重仪表,并输出多阶段控制信号, 用户可以直接访问PLC原料系统、终端控制系统,实现多阶段控制和自动控制。按照预先确定的配方,把各种不同的原料按比例进行混合,为了提高配料的精度和速度,保证产品的质量和增加产量,采用了微机控制技术。微机控制的配合生产线。
投料系统为了进行计量必须调节螺旋单位时间排出饲料的数量,通过调节单位时间螺旋的回转角度,来改变单位时间的饲料排出量;每个原料仓底部都安装有送料管道(管道口径DN65),分别由自动阀门和手动阀门控制开关,每种粉体的自动阀门安装在靠近管道出口位置,由送料泵负责将料通过管道打到计量仓,在计量仓进料口处的安装自动阀门,实现物料的快投和慢投料控制。
计量仓的四个支撑底脚与支撑架基础之间各安装一只称重模块,负责计量进入计量仓的物料重量,支撑架基础需做水平调试;原料计量完毕通过计量仓底部的的自动分流装置,分别自动加到相应的搅拌仓中。在计量仓的总卸料阀后水平安装到各个搅拌仓的分料自动阀门,把各个分料自动阀门的前端进料管用管道联通,这样可以保证卸料后基本无存料,到各个搅拌仓的卸料管道水和液料管道可以合并一条管道,以减少管道用料成本。