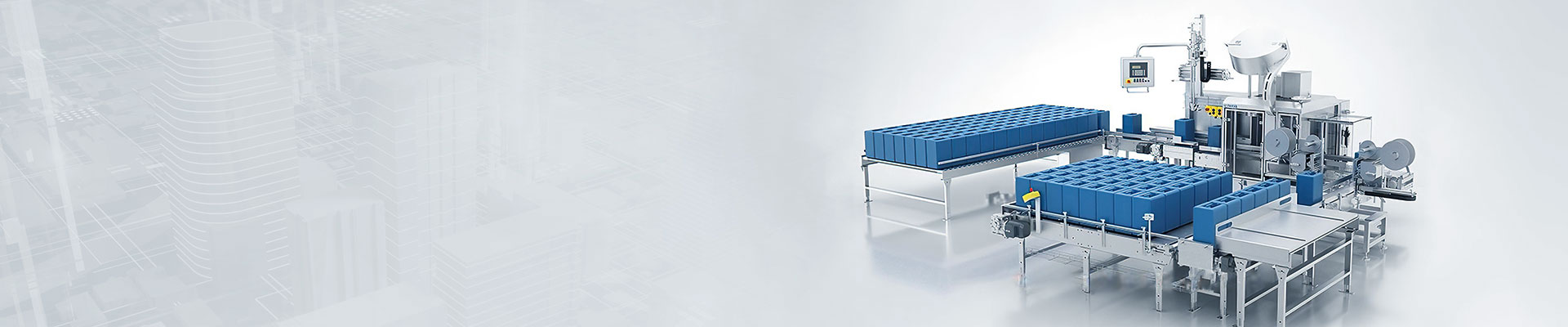
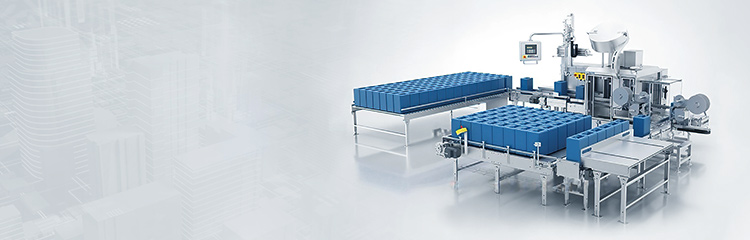
反应釜自控系统采用自动化配料设计、进料、出料全由电脑控制,动态称重模块、精密放大器、模/数转换器、微型计算机、显示器、打印机和执行系统等组成。通过触摸屏设定好各种物料所需的重量,按次序自动输送到配料自动进行称重、流量控制,从而实现精确计量和配料。

反应釜称重系统在操作时按下启动按钮,系统触摸屏启动,称重触摸屏清零。然后给原料快投料和慢投料有效信号,系统打开阀门启动料泵,开始原料的快速加料过程(即同时打开两个进料阀门),同时触摸屏启动随时跟踪读取电子秤信号,当重量接近达到预设的大投值时,称重触摸屏将关闭快投料信号,使系统进入原料慢加料过程(关闭一个阀门),同时称重触摸屏继续随时跟踪读取称重模块信号,触摸屏将判别料斗重量是否大于等于原料目标值—原料落差值。
配料系统如果大于等于则称重触摸屏关闭小投信号,停止加料过程(全部阀门及上料电机关闭),本次计量结束。如果需要在同一个计量反应锅内累计加量计量则开始第二种物料的加料,此时称重触摸屏首先清零显示输出,快投料和慢投料有效,其过程同上。否则开始卸料到反应釜。
在配料系统启动后,系统PLC自动控制顺序开启各原料气动阀及上料阀,同时启动上料电机,加料结束自动关闭上料阀门及电机,开启卸料阀及搅拌电机,原料开始卸料,反应锅开始搅拌,搅拌结束,系统开启反应罐卸料阀门和卸料电机,把成品料输送到成品罐,本次配料结束。灌装工人可以启动灌装机,进行装桶工序操作。反应釜配料过程也可以由操作员按照工艺要求手动顺序按动操作台上的阀门、电机按钮,进行手动配料过程操作。
每次生产前可以设置输入本次配料的配方,按比例分配所需原料数量(也可采用缺省方式,即仍然使用上一次的配方)。给自动上料提供数据依据。在生产启动的同时,PLC就将动态计量启动信号发给称重计量触摸屏,触摸屏即开始对各环节的重量进行采集、显示,并在不同的重量阶段采用快投料和慢投料策略,以兼顾提高效率和计量精度。在到达目标值时,输出停止计量信号,由PLC控制关闭相关阀门、泵等。同时完成卸料到反应釜的动作,计量触摸屏自动清零去皮。