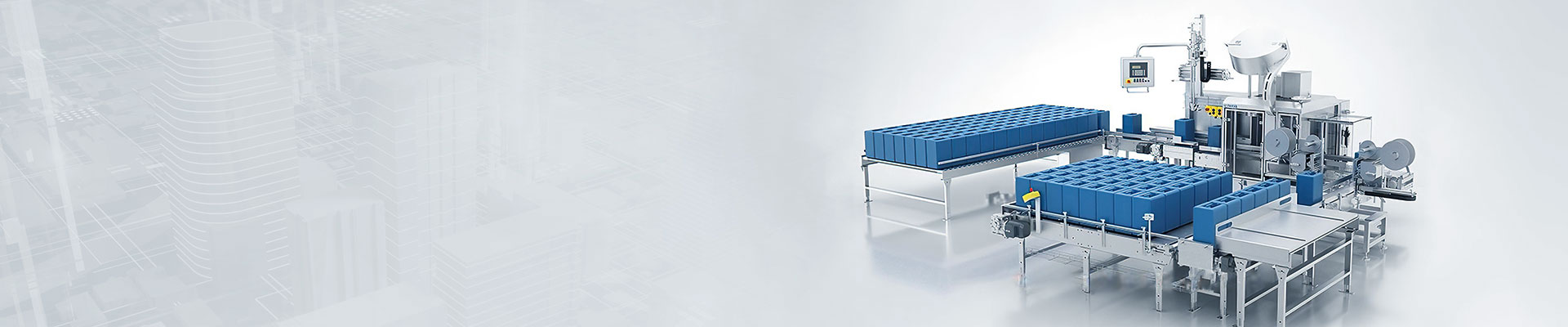
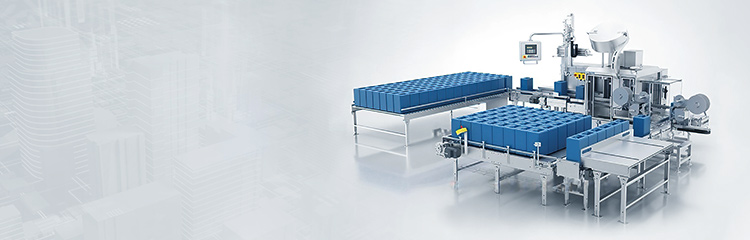
混配系统采用环形以太网实现PLC之间及PLC与监控管理级的共享,监控站与服务器之间采用TCP/IP协议传输,经过CPU运算后直接控制现场的反应釜电机。现场称量斗部分称重信号通过ISPMomentum称重模板由现场总线进入TSXMomentum,然后通过MB+通信将信号远传至CPU,完成称量的连锁和反应釜电机频率的精确控制。

喂料系统的广泛应用与现场总线技术的飞速发展,具有互操作性、互换性、可替代性、可扩充性和多台支持工业电脑。在配料的功能方面,要求实现的算法更多,实现的控制目标更高,配料功能更趋综合化。在称重控制系统的自诊断功能方面,要求自诊断功能尽善尽美、准确无误。在这种情况下,控制的自动化水平越来越高,从经典的PID调节、反馈、前馈回路控制逐步发展到批次控制、集散控制、面向对象的优化控制、人工智能的控制逐步发展到多参数多目标控制,对其进行校正、补偿,算法越来越要做大量细致精确,并显得尤为重要。配料、和混合对象优化控制、自适应控制或人工智能,通过计算机集散控制系统自身实现,不再附加其它计算机硬件。采用IPC与网络通讯组成的控制系统,对配料设备的支撑的要求已不仅仅是其功能多么强大、内容多么丰富,而是对其具有不同对象的用户再开发能力的需求日渐重要。配料机支持多种流行的高级语言,用户根据各个特殊控制对象的不同要求能实现自己的控制策略,将对行业的针对性提供了重要的手段。
投料系统采用集中/分布式结构,由称重控制器和微机监控站构成集散控制系统,采用MB+网,将一系TSXMomentum连接在CPU处理器上实现对现场设备的数据采集及控制。采用环形以太网实现PLC之间及PLC与监控管理级的共享。监控站与服务器之间采用TCP/IP协议传输。来自现场设备称重传感器信号通过MB+网络引QuantumPLC,经过CPU运算后直接控制现场的反应釜电机。现场称量斗部分,称重信号通过ISPMomentum称重模板由现场总线进入TSXMomentum,然后通过MB+通信将信号远传至CPU,完成称量的连锁和反应釜电机频率的精确控制。
(1)现场智能化称重仪表普遍使用,各种通讯技术与PLC互通互换控制,现场可触摸屏可以自动去皮等不同称重操作,如触摸屏故障的情况下智能称重仪表可以替代定量控制等,解决了相互替换功能的需要。
(2)数字化的直流调速、变频控制器、软启动装置、开关元器件等在反应釜生产过程中配合搅拌定量称重控制,触摸屏可以微调搅变频功率,搅拌电机在微速下转动,液体物料得到更好的混合,不会在高速搅拌下破坏物料的性质,适用于低速变频混合搅拌配料。
(3)人工的干预越来越少,操作的点越来越集中,操作方式越来越软件化。反应容器生产配料现场可以一边加料一边读取实时显示重量,同时搅拌功率显示器也在同一个监控位置,方便随时读取不同数据,节省人工干预时间,配料系统为人为不正确的操作自行纠错,解决误加料过程中的错误。
(4)配料控制系统的功能越来越向综合性发展,CRT的作用越来越强。控制系统及
配料现场在不同办公室可以监控现场配料状况,提升员工工作效率。
(5)数字信号越来越深入现场,控制将进一步分散,这个程序主要体现在数字称重仪表和数字称重传感器的应用,现场称重控制精度不会因外部机械结构受到影响,数字化集成技术也在触摸屏生综合应用,避免了现场的使用空间,简化了设备的复杂配置。