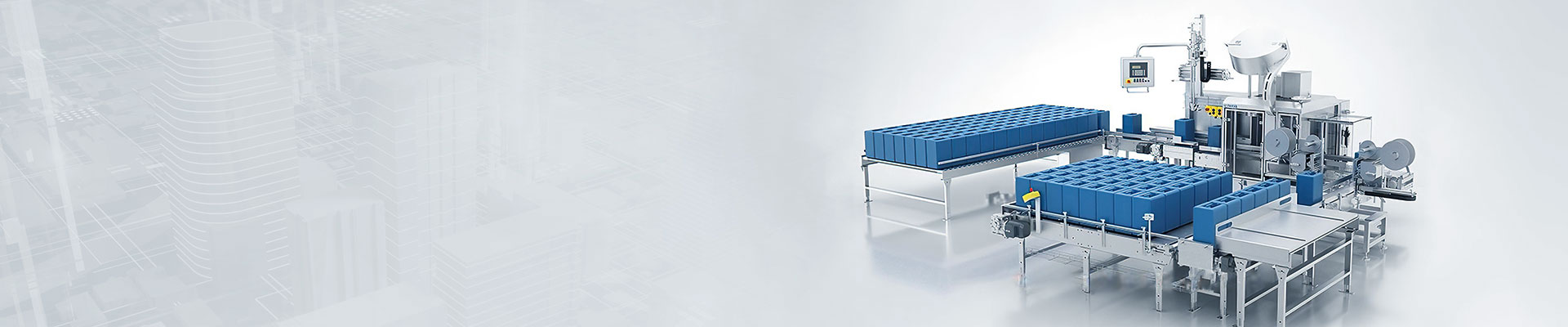
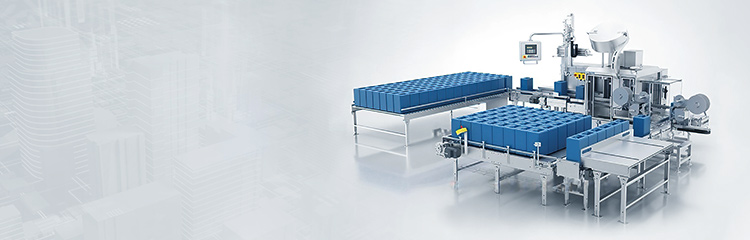
Reduction scales take the hopper scale and feeding mechanism as the whole scale body, through the weighing instrument or the upper computer constantly samples the weight signal of the scale body, calculates the ratio of weight change per unit of time as the instantaneous flow rate, and then through the processing of various software and hardware filtering technology, arrives at the "actual flow rate" which can be used as the control object.

Reduction scale adopts the whole machine type weighing frame, the material falls from the tail receiving section, and passes through the weighing section of the scale body under the spiral operation, the weighing module and the speed sensor measure the instantaneous weight of the material and the running speed respectively, which are sent to the weighing controller for processing, and get the instantaneous flow rate of the material, and output the PID control signal after the software calculates it, and then adjust the frequency through the frequency converter, and control the rotating speed of the feeding equipment or the dosing scale, so as to make the flow rate of the material reach the set requirements. The speed of feeding equipment or batching scale is controlled through frequency conversion adjustment, so that the flow of materials reaches the set requirements.
Reducing scale utilizes the rate of material reduction per unit time to account for the material flow rate of quantitative feeding equipment, using static weighing, dynamic control method, is a high-precision metering feeding control system. Hopper scale material reaches the lower weighing limit position (or empty scale), start the discharge port, the material in the silo quickly down to the hopper scale to reach the upper limit value set off, start the charging port, charging to the upper limit of the weighing to stop charging, in order to achieve the purpose of quantitative feeding. By adjusting the time of falling material and the difference of filling point through the rate of falling material, it improves the accuracy of weighing and control precision.
Multiple devices can be used to connect with the upper computer system to form a centralized dosage control. When the weight of the material in the weighing bin is greater than or equal to the upper limit of the bin, it will be switched on and enter the dosage state directly, and when it is lower than or equal to the lower limit of the bin, it will turn on the dosage Feeder and rapidly feed the material into the weighing bin, and then stop dosage feed when the material in the bin reaches the upper limit of the bin, and the unloading of the bin is in a continuous working state, and during the process of decreasing the material inside the bin, the instrument will carry out anti-P In the process of decreasing the material in the bin, the instrument carries out inverse PID control, so that the instantaneous flow rate is close to the set flow rate, and when the material is rapidly added to the bin, the instrument controls the discharging and metering in a volumetric control mode. The two control modes are converted periodically, thus realizing the continuous quantitative and quantitative feeding of the equipment.
Technical parameters:
Hourly flow rate:0~15t/h
System precision: better than 0.5% Ambient temperature: -20~+50℃.
Relative humidity: <90% RH (non-condensing)
Instrument power supply: AC 187V-242V, 50Hz±1Hz
Main function:
Control dosage by meter panel setting
Control dosage by superior computer
Completing the control of the whole process of discharging and timing materials.
The meter can display totalized quantity, instantaneous quantity and output quantity, etc.
The meter can display daily, shift totalization and monthly totalization for 2 years.
More than 20 kinds of working status and error status indication
Manual and automatic control functions
The instrument can output PID control signal and instantaneous flow current signal.
Standard RS-485 computer communication interface.