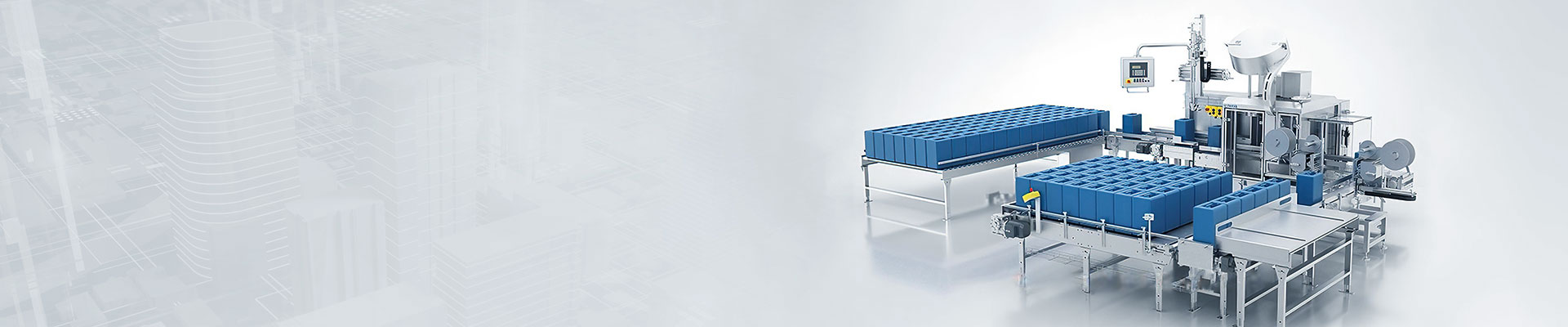
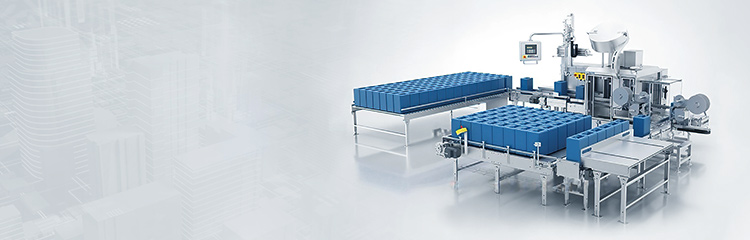
自动配料系统将秤量斗及给料机构作为整个秤体,通过称重仪表或上位机不停对秤体进行重量信号的采样,计算出重量在单位时间的变化比率作为瞬时流量,再通过各种软硬件的滤波技术处理,得出可以作为控制对象的“实际流量”。然后FC通过PID反馈算法,进行逼近目标流量的控制运算,输出调节信号去控制变频器等给料机控制器。

配料机通过RS485通讯方式检测到螺旋秤的流量,并根据配比值给出电机、非离子泵的控制电流。电子秤PLC输出控制电机、变频器,使粉体出料随螺旋秤的流量变化,电机配比控制为PID调节控制。辅料秤的流量通过通讯采集到控制主机。根据工艺要求配比,计算出相应的跟踪流量传给PLC。PLC给出控制电流,控制辅料秤的变频器,使相应的配料流量控制在跟踪流最范围。通过启停按钮实现设备的启停控制,也可操纵人机界面后配工艺上的启停按钮。通过控制PLC实现启停。
自动配料系统将料斗秤及给料机构作为整个秤体,通过称重仪表或上位机不停对秤体进行重量信号的采样,计算出重量在单位时间的变化比率作为瞬时流量,再通过各种软硬件的滤波技术处理,得出可以作为控制对象的“实际流量”。然后FC通过PID反馈算法,进行逼近目标流量的控制运算,输出调节信号去控制变频器等给料机控制器。
报警事件
自动称料开始时,如果某个放料阀未关,称重终端或配料检测不到放料阀关闭信号,称重系统会发出报警声响,暂停称重仪表的称料过程,并使运行指示灯闪烁。出现报警,自动放料不会进行,待消除故障或认为产生的报警原因不影响放料,按复位按钮后,再按“放料”按钮,则继续放料。
切换报警
自动放料开始时,首先检查每种原料切换是否到位,如果切换不到位或切换不一致,报警系统开始报警,自动放料就不能进行。通过检查,认为可以放料,按复位按钮后,再按“放料”按钮,则开始放料。
2.3.3反应釜满报警如果反应釜中已配原料浆未放出,仍往该锅放料,产生报警信号,自动放料就不能启动。待检查确认可以放料,按复位按钮,再按“放料”按钮,则开始进行自动放料。
急停
称料过程中,由于紧急情况需要停止称料,按下自锁“称料急停”按钮,各个秤的进料阀就全部关闭,电子秤停止称料。需要重新开始称料时,旋起“急停”按钮,再按“启动”按钮,则重新开始称料。自动放料时,按一下“放料急停”按钮,系统会关闭所有放料阀,停止放料、搅拌和输送。
人机界面
主站和从站的人机界面采用组态王组态软件加VB开发的通讯程序,由前配工艺、后配工艺、前配配方、参数设定、历史曲线及报警信息等组成。配料主菜单由一系列按钮组合而成。当鼠标停留在菜单按钮上时,按钮凸起,单击不同的按钮可进入不同的画面。操作的功能画面主要有两类,一类是显示操作画面,即显示数据(显示方式为数字、曲线、历史趋势等)、供操作人员进行操作的功能软开关和软按钮等;另一类是工艺流程画面,显示设备的工艺布置、工艺流程及相应的检测数据。