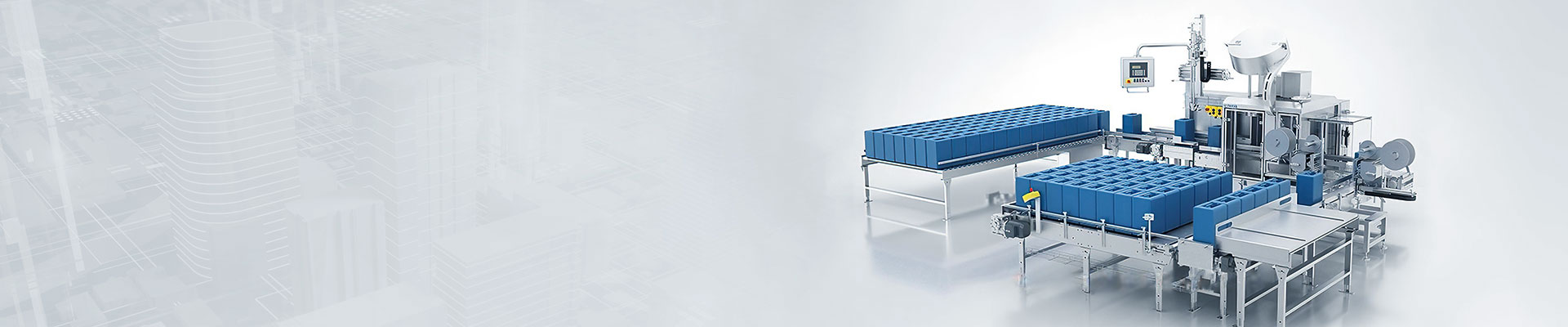
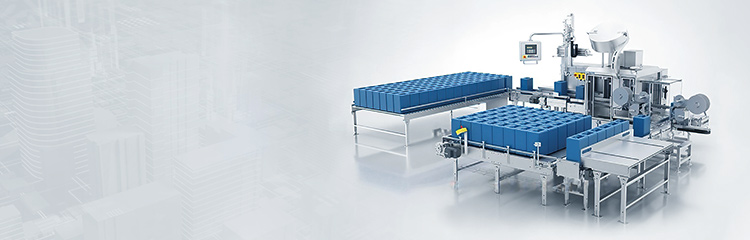
Vertical reactor is an automatic production line for conveying, proportioning, heating, mixing and packaging of different types of materials (solid or liquid). It adopts PLC control mode and novel frequency conversion speed control feeding mechanism, which can realize the functions of material transmission, dosage control, formula design and production data management with the dosage control software package. And can realize the aggregate control of multiple batching systems through the network.

Vertical reactor is an automatic production line for conveying, proportioning, heating, mixing and packaging of different types of materials (solid or liquid). It adopts PLC control and novel frequency conversion feeding mechanism, together with batching control software package, to realize the functions of material transmission, batching control, recipe design and production data management. And can realize the aggregate control of multiple Batching systems through the network.
The weighing control system adopts Advantech industrial machine as the upper computer and Siemens S7-300 PLC as the lower computer, the upper computer adopts WinCC6.0SP3 to write the interface, and the operating system is WindowsXPSP2; the lower computer adopts STEP75.3SP3 to program. The upper computer is a human-machine interface (HMI), and the lower computer is the executive part of the Dosage system. The control of the whole electrical equipment is centrally controlled by this PLC system, and all kinds of on-site analog and digital signals are centrally processed by the PLC, which collects and sends these data to the computer through the communication with the upper computer and displays them through the HMI. The operator can also send commands through the host computer, the PLC receives the commands through a series of programming work, signal processing to control a variety of operations.PLC uses the local master station connected to the field Electronic scales. The PLC uses a local master station to connect to the on-site electronic scale, and the communication between the master station and the on-site electronic scale uses Profibus-DP fieldbus. The master station is S7-300PLC, which is composed of power supply, CPU and Ethernet communication module, and its CPU module adopts CPU315-2DP, which has built-in MPI communication to support multi-point communication. The whole dosage system has simple wiring and more reasonable structure. The upper computer communicates with PLC through Ethernet interface, which is easy to expand.
The dosage system can meet many requirements for monitoring and controlling the production process as well as archiving and processing the production data. The user interface drawn by WinCC is easy to operate and has a good human-machine interface, which can dynamically display the running status of various devices on site and various parameters of the dosage system. The operator can also flexibly control the starting and stopping of the field equipment and change the operating parameters of the dosage according to the needs. Configuration of the main control process written for WinCC. According to the statistics of points to be monitored and controlled by the batching, it has strong control function and strong arithmetic ability.
Technical parameters:
Design volume: 50L-10000L (volume can be designed according to requirements).
Electric heating power: 6kw-700kw (depending on the volume of the equipment and materials required for the process).
Reaction temperature: room temperature-300℃ or higher, depending on the working conditions.
Reaction pressure: -0.1-0.3Mpa.
Material: SUS304 stainless steel, SUS321 stainless steel, SUS316L stainless steel or Q235-B carbon steel.
Stirring form: paddle type, anchor paddle type, frame type, screw belt type, turbine type, dispersing disk type, combined type, etc.
Heating method: electric heating, steam heating, water bath heating.
Heat conduction medium: thermal oil, steam, hot water, electric heating.
Heat transfer structure: jacket type, outer half-pipe type, inner coil type.
Stirring speed: the selection of stirring speed depends on its material mixing needs to be selected; conventional liquid material polymerization reaction, the speed of 85r/min; containing powder materials and liquids need to be mixed to achieve the effect of dispersion, the speed of 0-1500r/min; containing oil and liquids or two kinds of incompatible liquids need to be mixed to achieve the effect of emulsification, the speed of 0-2800r/min. The rotating speed is 0-2800r/min.
Working principle: put the reaction solvent into the inner layer for stirring reaction, and the sandwich layer can be connected with different cold and hot sources (freezing liquid, hot water or hot oil) for circulating heating or cooling reaction. Through the middle layer of the reaction kettle, the constant temperature (high or low temperature) hot solvent media or cooling media can be injected into the reaction kettle, so that the materials in the reaction kettle can be heated or cooled at constant temperature. At the same time, the reaction can be stirred under atmospheric pressure or negative pressure according to the requirements. The materials are reacted in the reaction kettle, and the evaporation and reflux of the reaction solution can be controlled. After the reaction is finished, the materials can be released from the discharge port at the bottom of the kettle, which makes the operation extremely convenient.