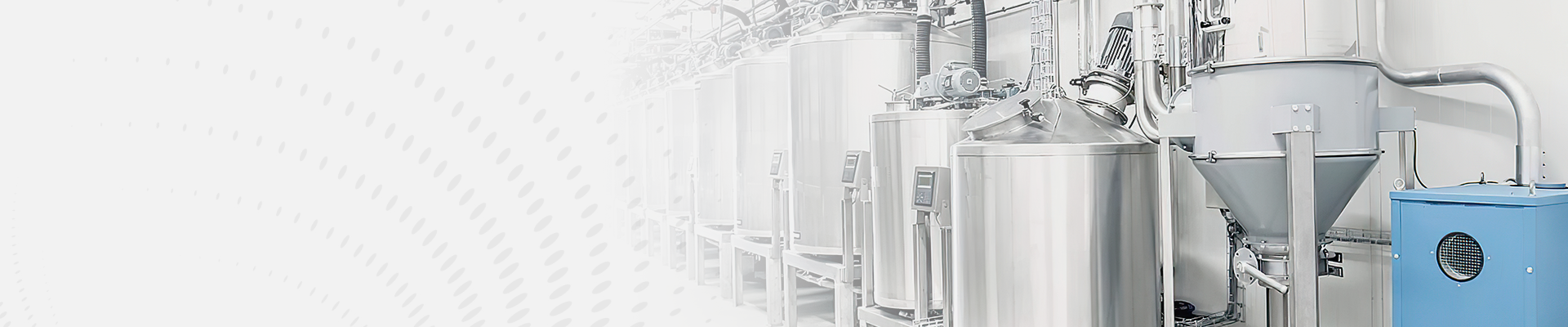
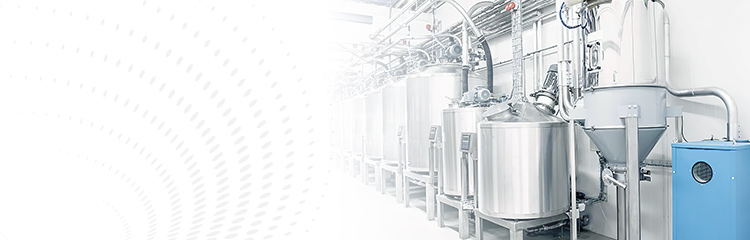
Automatic batching system in the field of powder processing and handling, the leading technology of powder processing equipment will be absorbed and optimized in the weighing and mixing machine on the basis of adhering to the optimization of the equipment, effectively help our customers to solve the difficult problems in the process of production and processing, so that our series of equipment not only has a high cost-effective, but also in the field of pharmaceuticals, food, fine chemicals and other fields are very well used.
Batch feeding systems are mostly used for the formulation of components for various polyurethane applications, where polyols need to be mixed with liquid additives (catalysts, stabilizers, etc.). Automated mixers consist of a pre-mixer for small amounts of additives and a main mixer for the base polyol. Optimized design of the components allows a high degree of dosage accuracy, and both mixers are fitted with load cells for precise weight control. The mixers are easy to operate and all related processes (e.g. feeding of the raw material into the mixing tank, dosing, stirring, spillage prevention, temperature control, discharge, etc.) are highly automated. Blended polyol mixtures can be transferred to intermediate tanks, tankers or into drums and other containers by means of liquid fillers. The batch control program allows an easy control of the management of the recipes, recording all the parameters of the process, with separate switching devices for each key component, in case of change of the corresponding parameters. Depending on the formulation of the product, modular and programmed control of the individual production steps is possible. The innovative inventory control program allows to record and view all raw material consumption processes, so that the customer can accurately plan the replenishment of raw materials.
Dosing system features:
1, to avoid human error: production instructions and formulas need to be reviewed, otherwise it can not take effect, feeding to identify the correct material, otherwise it can not be put, the dosage process is fully automated, no need for human operation.
2、No dust leakage during the working process, meanwhile avoiding the contamination of drugs: adopting dustless feeder to avoid dust escaping when feeding, adopting vacuum feeder to convey the materials to the silo in airtight condition, adopting airflow sealing when metering and feeding.
3、Equipment structure and material comply with FDA regulations and health standards to ensure thorough cleaning and avoid cross-contamination.
4、With on-line cleaning function, on-line drying function and quick-loading structure, easy to clean and maintain.
5、Adopting high-precision weighing module and many kinds of anti-interference technology, the weighing data is accurate and reliable.
6、Adopting advanced control algorithm and high-performance actuator, high positioning accuracy, high metering accuracy and high output.
7、Adopting PLC and touch screen technology, reliable performance, simple operation, with production data report, archiving, recording and tracking functions. It can communicate with the upper computer and exchange data.
8、System alarm and self-checking function to ensure smooth production.
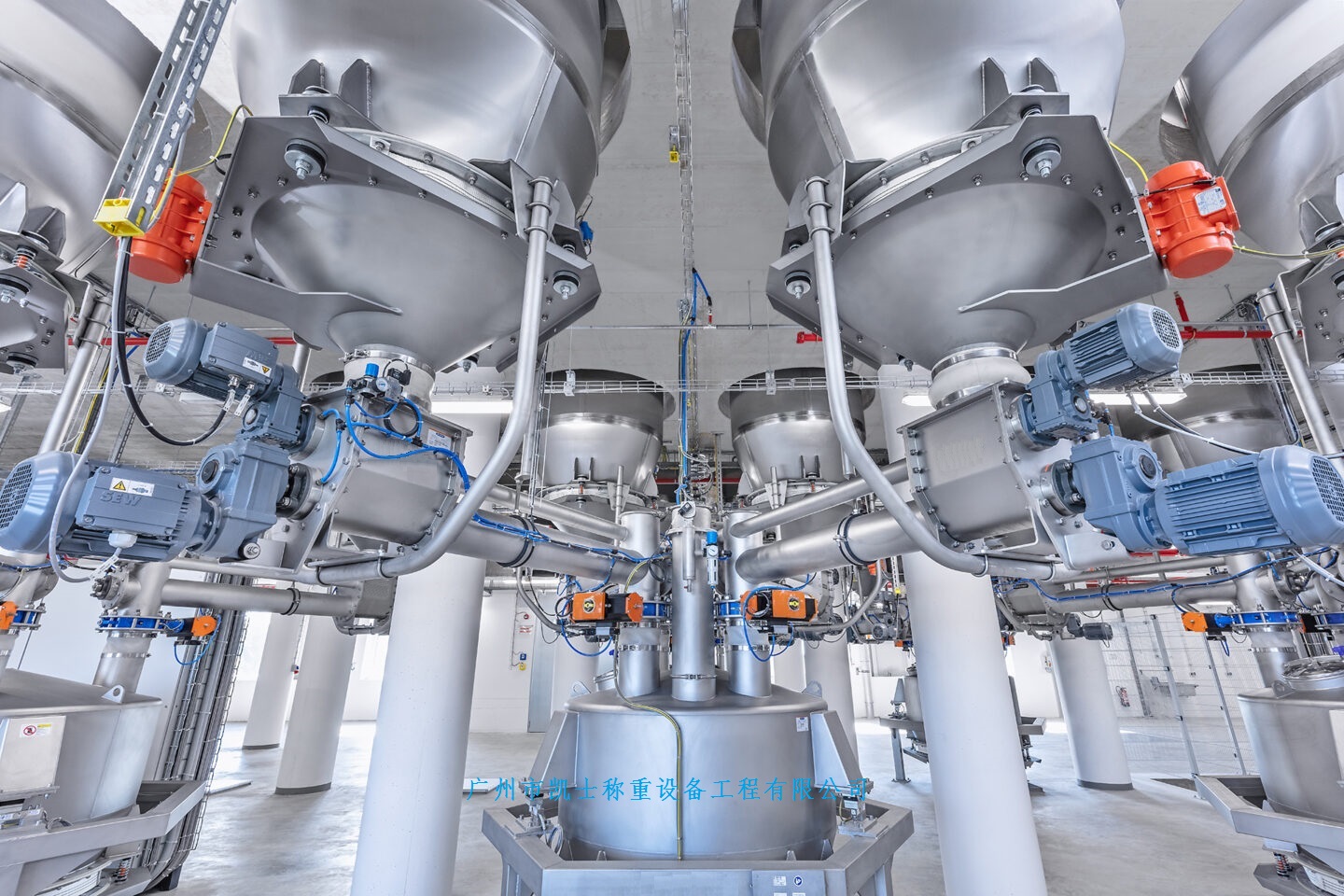
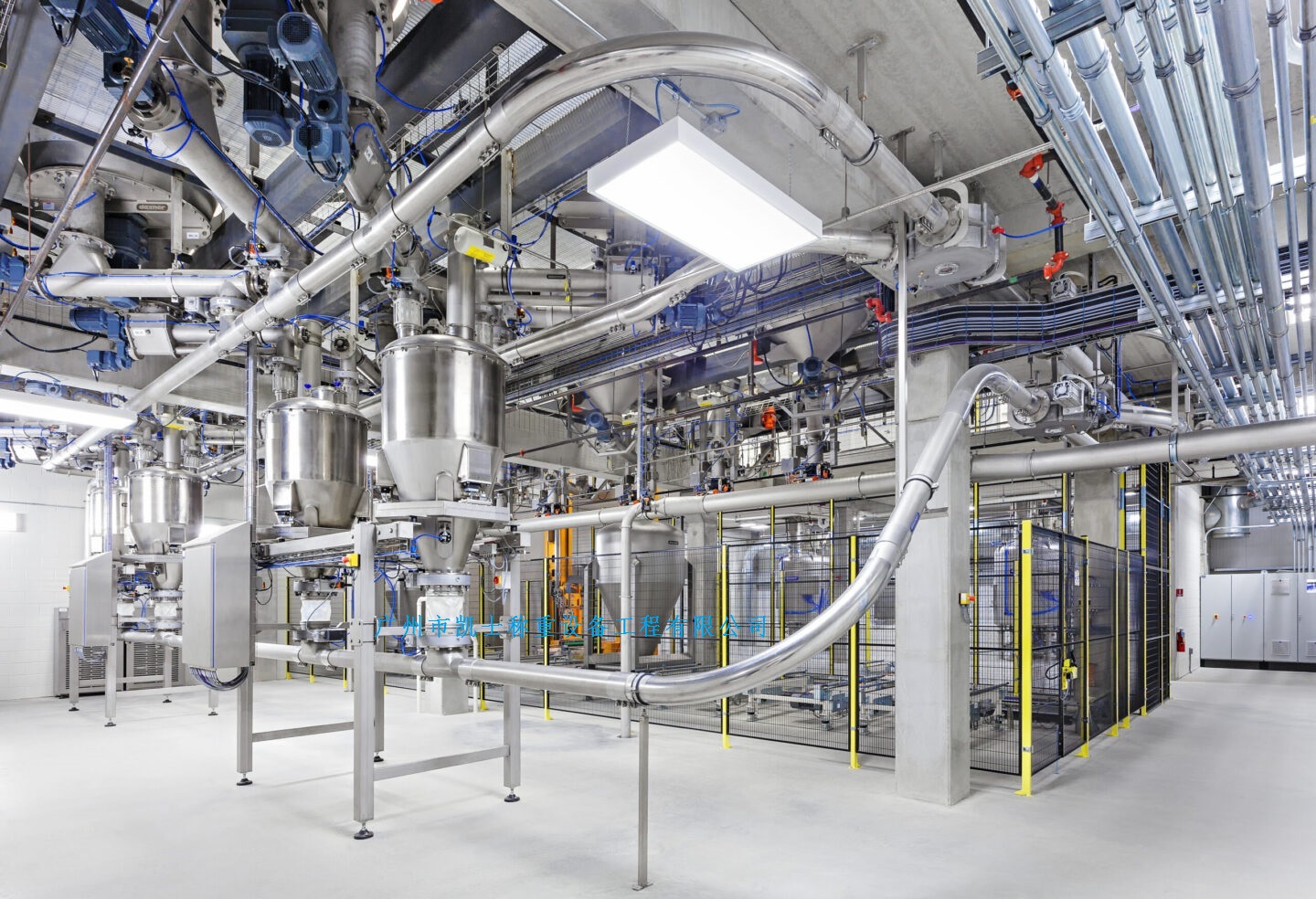
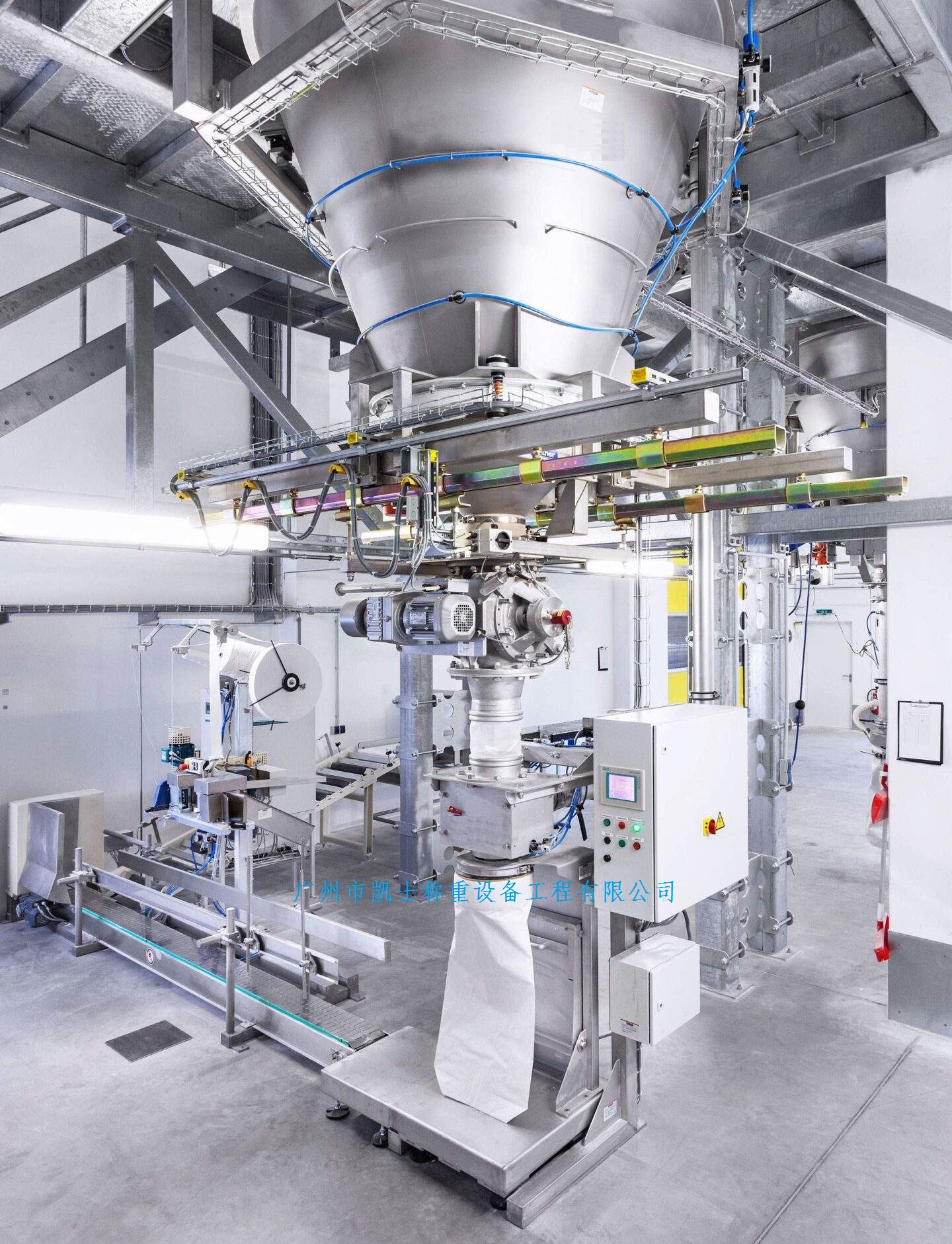
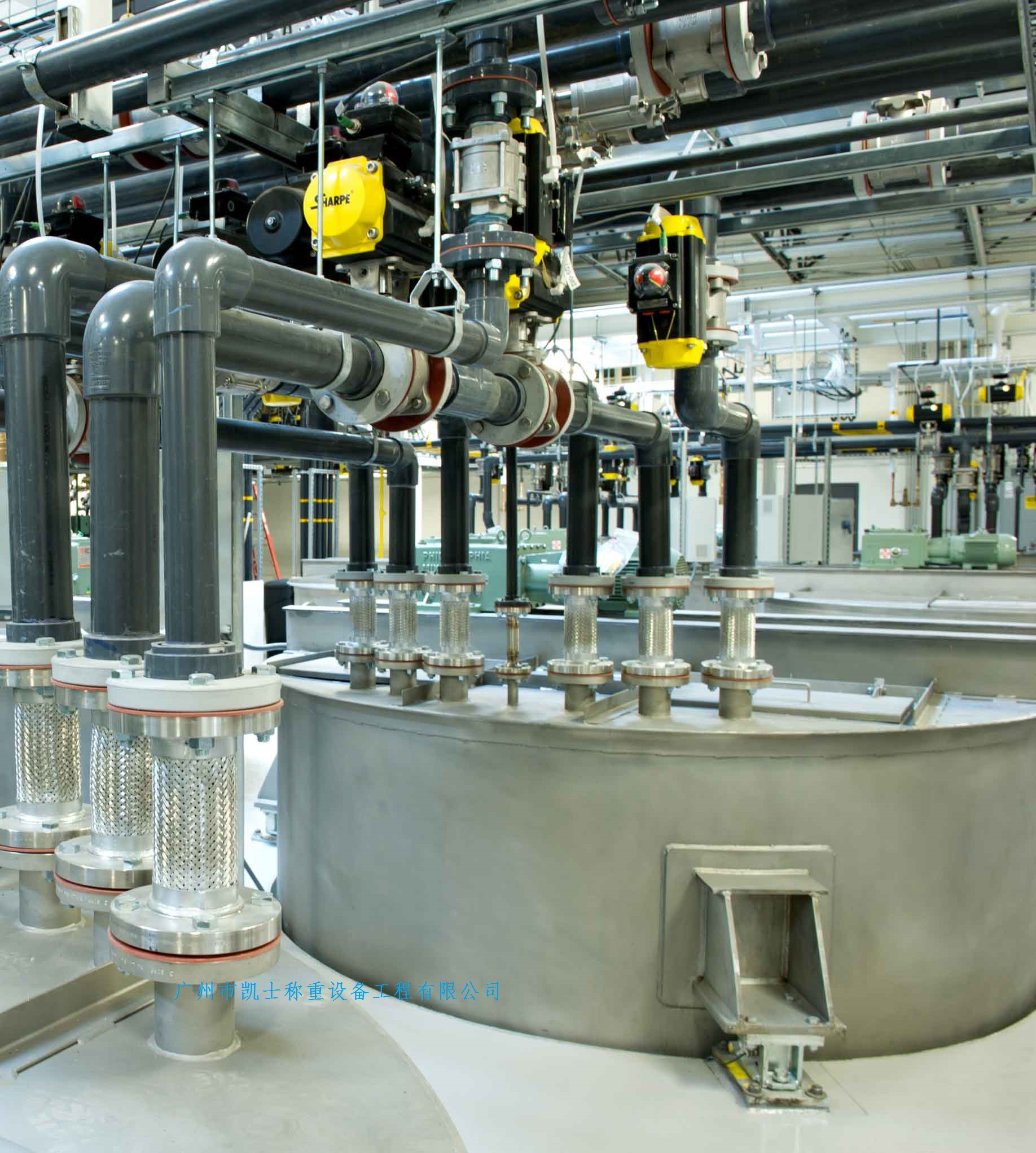
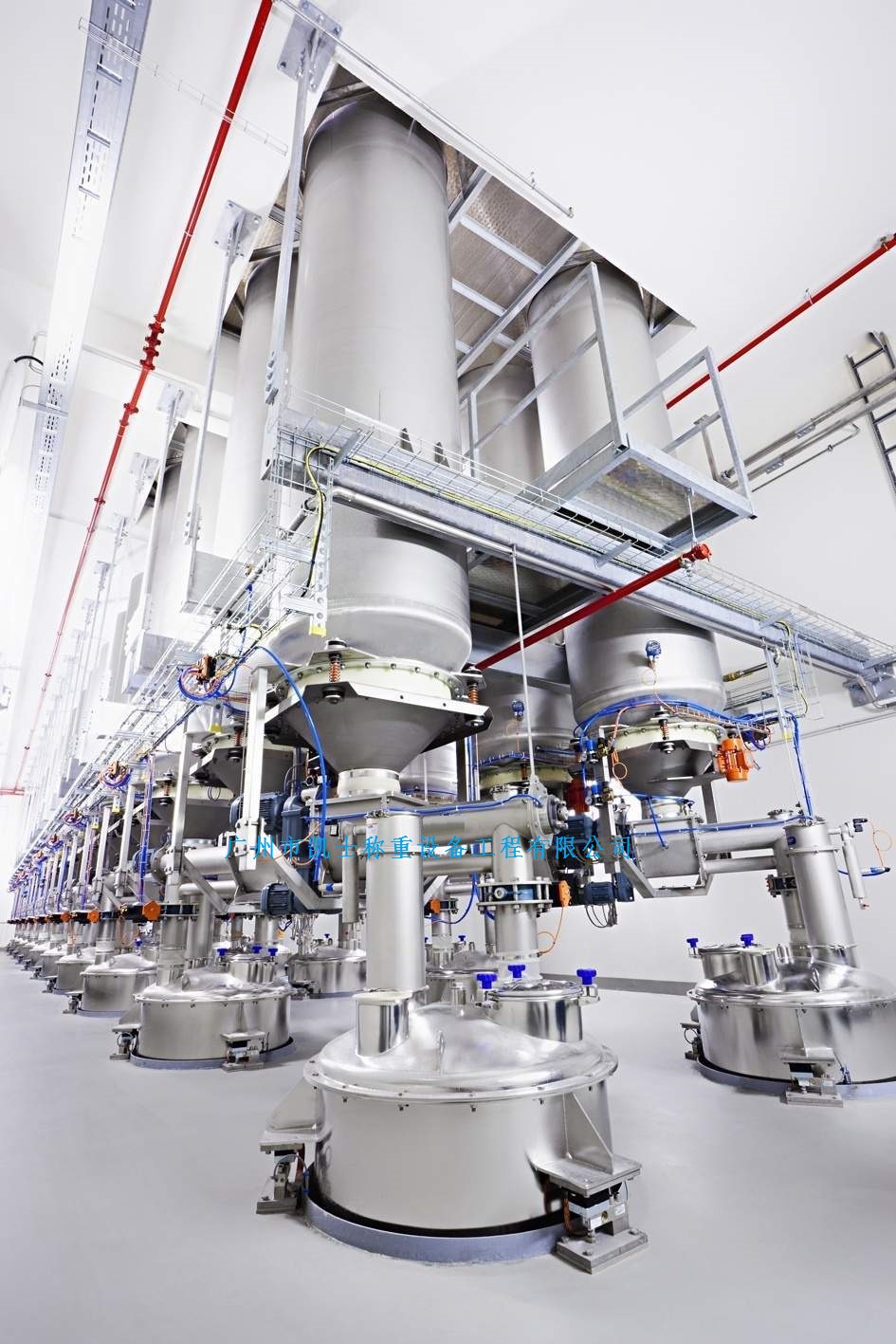
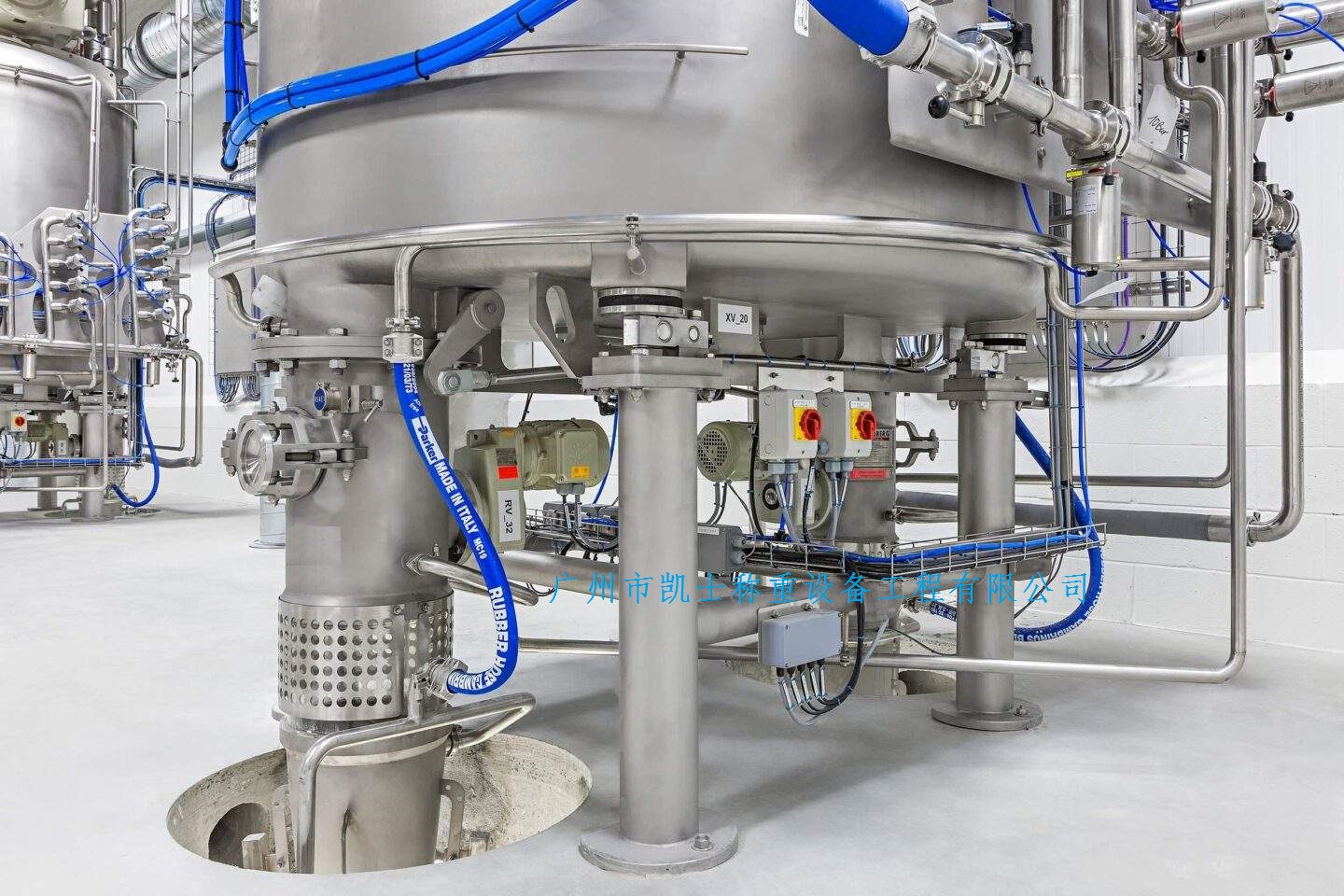