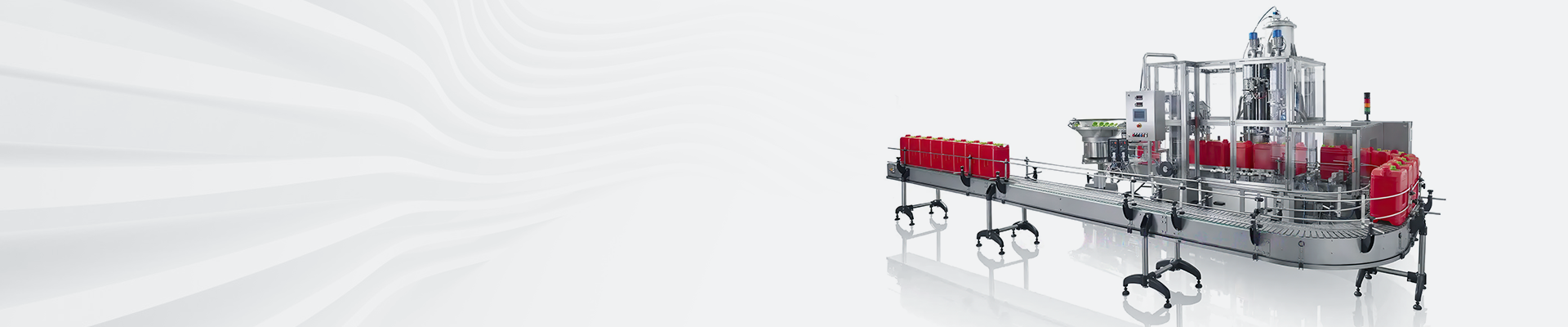
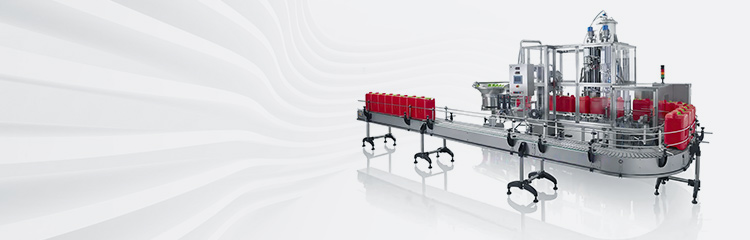

Summary:In the artificial board weight reduction method of sizing measurement and monitoring process, the use of computer technology and PID control method, to complete the system configuration, design, control, management and other functions. The dosage system transforms the difference between the front and rear weights of the materials in a unit of time into an instantaneous flow signal, which is used to participate in the flow regulation and control as well as the management of the material accumulation and accumulation. It is characterized by high measuring accuracy, good repeatability and stable control. In the transformation of the sizing system adopts the weight reduction method, the application of computer technology to complete the system design and monitoring functions.
I. Overview
Domestic manufactured wood-based panel production line, the process of adhesive, waterproofing agent, additives, the amount of application control, most of the open-loop manual control, the formation of the main raw materials and adhesive, waterproofing agent, additives, the proportion is not appropriate, resulting in the quality of the product is unstable, and the current international advanced measurement and control method is to use the weight loss method of sizing and metering dosage system. Weight loss metering is a new type of weighing flow measurement, which transforms the difference between the front and rear weights of the materials in unit time into an instantaneous flow signal, which is used to participate in the flow regulation and control, and to carry out the management of the cumulative accumulation of materials. With high measurement accuracy, good repeatability, stable control and other characteristics. In the transformation of sizing system adopts the weight reduction method, the application of computer technology to complete the system design and monitoring functions.
Feeding system is mainly designed to complete the glue storage tanks, curing agent storage tanks, hot water tank level automatic measurement and control, hot water tanks, paraffin melting tanks, temperature measurement and control of circulating water, glue, paraffin, curing agent intermediate tank metering control, glue, paraffin, curing agent applied amount of the weight loss metering control, as well as the various valves, the program control of each motor, we boldly adopted the control technology in the automatic regulation and control technology. Achieve very good results.
Second, the system composition and function
In the use of computerized feeding system, the use of hierarchical distributed structure, that is, by the equipment control level, process monitoring level and production management level. Utilizing PLC has the advantages of dustproof, fatigue resistance, high temperature resistance, anti-interference and so on, as the field control. Adopting industrial control machine as computer workstation, each workstation adopts configuration software to monitor the system in real time, and through the real-time database directly from multiple nodes, to obtain and store high-resolution process history data to form process monitoring. Through the real-time database client tools, real-time data and historical data analysis, the use of network publishing tools, the enterprise and production information through the network of the enterprise intranet interconnection to each user.
1. Equipment control level
The dosing equipment control level is directly connected to various devices (such as transmitters, actuators, weighing instruments, etc.) in the field to monitor and control the connected devices, and is also connected to the computer on the upper level to accept the management information from the upper level and to transmit upward the characteristic data of the devices and the real-time data collected. In this system, the controller is an S7-314 programmable controller. Its main function is to realize the liquid level control of hot water tank and glue tank, temperature control of paraffin tank, rotational speed control of glue pump, paraffin pump and curing agent pump, as well as logical sequence control of each motor and valve.
Analog I/O module mainly completes the acquisition of analog signals such as pressure, temperature, weight, flow, frequency and PID control output. Digital I/O module mainly completes the acquisition and control output of self-locking, starting, stopping and other signals of the equipment. In order to ensure the reliability of the whole system, the input and output channels are left very redundant.
The interconnection between PLCs is through the MPI interface to form a PLC network. The MPI network is used for global data communication by means of global I/O, and the MPI conforms to the RS-485 standard.
2. Process monitoring stage
The process control stage is a Siemens industrial controller, which is connected to the PLC through PROFIBUS fieldbus. Due to the system's reliability, real-time and openness requirements, each workstation using WINDOWSNT4.0WORKSTATION operating system platform Wonderware's Intouch configuration software to run. Intouch configuration software to achieve the following functions:
(1). Communication with the lower machine Siemens PLC: Intouch provides a wealth of I/O service programs, can be easily connected with Siemens programmable controllers, fast and reliable communication.
(2). Switching of process graph: The monitoring program provides process-related graphical interface. Through the button can be switched to a different screen to show the production of each production process part of the production of the actual situation and related information.
(3). Control mode selection: The control system provides two remote control modes, automatic control mode and manual control mode. They can be set by pressing the selection knob on the interface of the monitoring program.
(4). Manual operation of equipment; set the remote manual start/stop function of single equipment in the monitoring program. Manual operation mode as a supplement to the automatic control mode of operation for the control system to provide flexibility for human intervention. Through the mouse to select the device to be manually started and stopped, click the manual start and stop button to complete the manual operation of the device.
(5). Communication with the real-time database: the control system through the Ethernet and the real-time database to transfer data regularly, the real-time database as the Intouch history database and I/OSERVER. Intouch and IndustrialSQLServer communication is based on the TCP/IP and Windows NT.
The communication between Intouch and IndustrialSQLServer is done by Suitelink, a real-time communication protocol based on TCP/IP and implemented on Windows NT.
(6). Parameter setting: According to the requirements of production process changes, online flexible adjustment of process parameters, motor speed, and control algorithms.
(7). Alarm processing: When the equipment fails, the system will prompt the operator through the alarm screen, record the detailed fault information in the alarm window, and print out the information at the same time. Alarm is divided into: current alarm record, historical alarm record.
(8). Display the running status: The monitoring program displays the working current value of the running equipment, the instantaneous flow value and cumulative value of the applied glue, paraffin wax and curing agent, the rotating speed of the motor, the temperature, the pressure and other running status in real time for the operator to understand the running status of the system.
3.Production management level
The production site industrial control machine is networked with the company's CIMS through Ethernet, and the administrator can access the control station through password, and can quickly browse the production process, energy consumption, quality and other conditions, which is convenient for the modern management of production.
Third, the application of PID technology
Feeding system in the control process due to the complexity and variability of the working conditions, fiber measurement with non-linear characteristics, so the use of PID technology. The working process of the controller can be described as follows: first of all, the controller's input is transformed into a quantity for the logical decision-making system, the decision-maker according to the control rules to determine the relationship between the application of logical reasoning algorithms to derive the controller's output, and finally by accurate calculation to obtain the precise control value to control the object to be controlled. The core of the controller design is the establishment of the control rule base, the establishment of the rule base commonly used method is based on input and output data to establish the object model, and then according to the model to extract the corresponding control rules, and at the same time, drawing on the operating procedures, that is, the operator's experience of the summary, and make appropriate changes. The basic control principle is to ensure that the output of the controller must be able to make the system output response to the dynamic and static characteristics of the best.
In the process of wood-based panel production, glue, paraffin wax and curing agent are applied to fibers, and it is necessary to ensure that three delivery pumps accurately track the fiber quantity and add it accurately in proportion to ensure the product quality. So the designed controller should have high control accuracy and tracking performance. When we use the controller, we must take more language values for language variables, that is, the classification is finer, and the amount of calculation and the number of rules need to be increased. Moreover, the increase of the number of rules sometimes does not make the control performance increase linearly.
IV. Concluding remarks
In a word, in the weight-loss sizing metering and batching system, we adopted a hierarchical and distributed structure, selected mainstream PLC and industrial computer hardware, selected Intouch configuration software, and adopted PID control algorithm technology for overall design and reference. After more than two years of operation in the production site, the control effect was good and the expected effect was achieved.