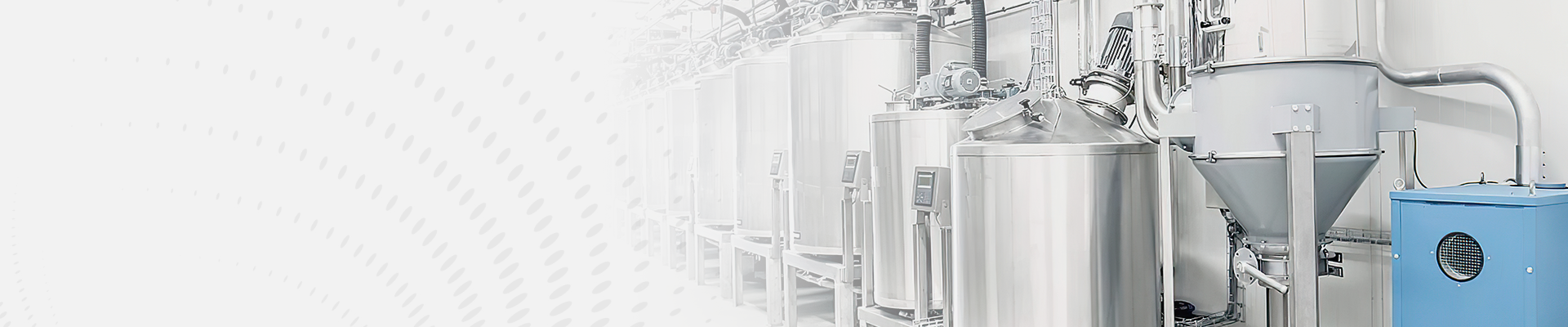
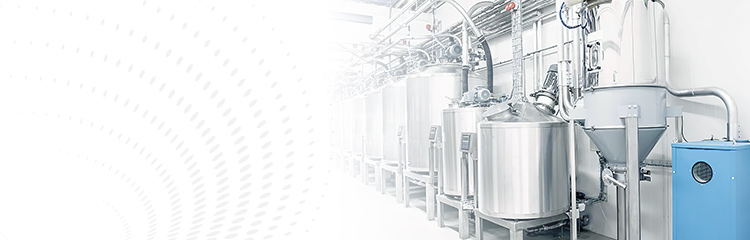
Automatic dosage system is based on human control instructions and settings, through the microcomputer control to achieve the purpose of automatic dosage and automatic weighing and counting, according to the nature of the raw material is mainly divided into large material weighing, small material weighing and micro-material weighing, of which the small material weighing is the most complex and most important in the three kinds of weighing. Weighing system is the core part of the mixing system, good or bad design will directly affect the quality of the entire mixed dry mix, thus affecting the performance of the product (such as color abnormalities, dimensional instability of the finished product, extrusion process is unstable, unstable mechanical properties, etc.). The control of automatic weighing accuracy is the key to the control of the entire weighing system, if the automatic weighing accuracy is not high or unstable will directly lead to the inaccuracy of the actual weighing and the formula of the proportion of the distortion, which directly affects the stability of the quality of the dry mix and the quality of the finished product.
Weighing process control
1、Process control
Weighing of small materials, micro-feed weighing, weighing of large materials, a generalization of the process control, curvilinear, typical, the weight gradually increases over time until it reaches or close to the set value, and finally unloaded to return to the whole process of 0, which represents the weighing system of a raw material of a single batch of the weighing process control, if the continuous weighing will be a repetition of the process. The entire weighing process can basically be divided into two weighing stages, respectively, by two speed control of the material, the speed of the cut-off point by the pre-set two values of G rainbow, G2 decision, G rainbow, G Fei corresponding to different raw materials are different. Generalization of the parameters used in the mixing system of different manufacturers, for different systems and different specific conditions of use, the weighing process control of the specific time parameter settings will be changed, but the magnitude of change is not large.
2, the composition of the measuring chain
Composition of the entire weighing and feeding system of the measurement chain mainly consists of the following parts: sensing elements (sensors), connecting components (such as shielded cables, etc.), A/D converter (the input side of the amplification, with a touch screen), metering control, formula input control, control unit (metering device). Where the A/D converter on the input signal has an amplifying effect, the input analog signal into a digital quantity and feedback to the PLC or a higher level of control system to achieve closed-loop control.
3, process control analysis
The entire weighing control system can be divided into small material weighing, large material (PVC) weighing, microfeed weighing (working principle is similar to small material weighing). The weighing process can be divided into automatic weighing and manual weighing.
When the system is in the automatic state, the first from the PC to enter the formula, different formulas correspond to different numbers, enter the formula number to the corresponding menu to be produced. The operation procedure of production is to select the corresponding production line, then activate StartRecipe, the system will start weighing automatically. Before the automatic weighing, the system automatically detects the weight parameters on the scale to be weighed to see if they exceed the values pre-set in the system. Since under normal circumstances the weighing system is continuous weighing, and each batch of material is absolutely under the net is impossible, coupled with the scale around the interference and failure and other reasons, should be based on the actual use of each scale of the 0 reference point (unloaded weight parameter) to set a positive and negative deviation, in the range of the deviation will be the default for the scale is unloaded, the system can start weighing normally. If the weight parameter on the scale exceeds the deviation range, it will not weigh, and the system alarm prompts that the scale is not empty. At this time, it is necessary to check whether it is because the raw materials in the scale are not finished, or the scale is malfunctioning, or the parameter setting is unreasonable, or the scale needs to be re-calibrated for reasons such as its reference point.
Because a formula system of PVC profile must contain large material weighing and small material weighing, when the system is in automatic state, start the formula weighing system, large material weighing and small material weighing at the same time to start the weighing process is independent of each other, but only two kinds of weighing all complete to be counted as a batch of material weighing is complete, there can be a signal for the next material. Large material weighing only a PVC component, weighing the component is considered to be large material weighing is complete, and then the system will automatically detect the weighing accuracy (weighing error) is in the pre-set range (<+0.5%), if out of the set range, the system will be alarmed to indicate the actual error value for emergency treatment (manual feeding or discharging). Under normal circumstances, the small material consists of several raw materials, the system automatically weighing will be strictly in accordance with the formula system set in the order of weighing one by one, each component weighing between the delay interval of 5?10s. Under normal circumstances, the weighing process of each ingredient is first high speed, then low speed. High-speed weighing when the fast material, weighing the proportion of the ingredients accounted for most of the ingredients; low-speed weighing when the low-speed material, weighing the proportion of a very small, mainly to control the accuracy of weighing. Weighing needs to be set in advance in the menu parameters and programs for high and low speed weighing conversion of the slitting point Gi and the size of high and low speed. For different raw materials, high and low speed weighing conversion of the cutting point and the size of the high and low speed may be different, depending on the specific circumstances. After weighing the raw materials of each ingredient should be tested to determine whether the weighing accuracy (weighing error) in the pre-set range (W ± (0.2?0.3)%), the normal continuous weighing of the next ingredient, if out of the set range, the small scale will be alarmed, suggesting that the actual error value, for emergency treatment. When the big material, small material weighing are completed, the scale body only under the material, under the material, the system will also automatically detect the weight of the scale body whether the weight parameters exceed the pre-set parameters of the unloaded weight to confirm that the material on the scale body is under the end of the material. For various reasons the weight parameter on the scale is not necessarily zero when unloaded, the unloaded weight parameter is set according to the specific situation. If the actual weight parameter is greater than the set value, the scale will remain in the unloaded state until the weight parameter on the scale is within the set range, then the unloading is complete and the next batch of material can be weighed.
When the system is in manual state, all the weighing and discharging have to be done manually, step by step. Before weighing, the system does not detect the weight coefficients on the scales; when weighing, select the scale to be weighed in the SelctionMenue menu, set the value of the weight to be weighed, and then select the corresponding canister (raw material). Activate startWeighing, the system will automatically complete the weighing of the raw material, after weighing the system to detect the actual weighing weight, if the weighing error exceeds the set range then the system alarm and prompts the actual error value for manual replenishment or unloading of excess material. Under manual condition, the weighing of each kind of raw material is carried out according to this program, when all the weighing is finished to be discharged, it is also necessary to select the corresponding mixer and activate the Discharge menu to start discharging the material, and after discharging the material, the system should detect whether the material in the scale body is discharged cleanly or not, the same as in the case of automatic weighing under the same principle of detection.
The detection of the weight parameters of the whole weighing control system is realized through the measuring chain. According to the pre-set parameters in the PLC program, the frequency converter is driven to adjust the size of the speed, and then the frequency converter drives the screw speed motor or the high-speed rotary valve to achieve the purpose of controlling the feeding.
Although the process of weighing small materials and large materials is independent of each other, all materials must be weighed before there is a signal for discharging. This requires the design of the weighing system and set specific parameters to be considered as a whole, not only to consider the weighing accuracy of the respective weighing, but also to consider the consistency of the two weighing process, that is, the two weighing process time to be close. Reduce the weighing process due to a party weighing fast, a party weighing slow caused by waiting for each other to extend the entire weighing process time. At the same time, in the design of the weighing system and set specific parameters should also be considered when the weighing system is a component of the mixing system, not only to consider the weighing capacity and mixing capacity of the matching, but also to reasonably design the entire weighing process, do not cause the weighing process is too fast to affect the accuracy of the weighing and benign operation of the system, and the waiting time is too long. Because when the mixer hot mix of materials, even if the weighing system has been all weighing, the dosage system will not issue a material signal, you must wait for the hot mix of materials in all under the material will be under the material signal. In addition, the weighing process can not be too slow, although the weighing process is slow to help improve the weighing accuracy, but this may cause the mixer to wait for the weighing of the material after the mixing machine, wasting mixing time, affecting the mixer mixing ability to play, affecting the production capacity of the entire mixing system.
Weighing error analysis
1, the composition of the dosage accuracy
Weighing system of the system affects the individual accuracy of the factors is also the main reason for the system to produce error. For small materials. Large material weighing can be divided into positive pressure conveying weighing and negative pressure conveying weighing, small material weighing is through the PLC to control the frequency converter, so that the speed motor drives the metering screw to run according to the set speed of the material. In the current automatic weighing system, the vast majority of the weighing process is divided into two stages of coarse feeding and fine feeding, so whether it is a large material weighing or small material weighing, involves a coarse feeding (high speed feeding) and fine feeding (low-speed feeding) of the cut-off point setting problem.
The weighing setpoint is a cut-off point between high and low speeds, as shown in Figure 4, and this value is pre-entered into the PC before weighing. Coarse charging stage of the charging speed is howl, which can reduce the weighing time, but also weigh the whole weight of the majority; to reach the cut-off point, stepped into the fine charging stage, the charging speed is howl, so that you can weigh the remaining small portion of the raw material, but also to control the accuracy.
Weighing system error analysis is the core of the whole system control, it determines the reliability and accuracy of the weighing system, which will affect the production quality and production capacity of the whole mixing system, so it is to ensure that the product performance and stability of the source. There are many reasons for the system error, such as the accuracy of the sensor, the composition of raw materials, the environment, the design of the program, set the parameters of the factors.
2、Slitting point setting
System accuracy is divided into feeding accuracy and static weighing accuracy, feeding accuracy is subdivided into weighing accuracy and system impact on two aspects, while the measurement of accuracy will affect the weighing accuracy, due to space limitations, this paper only analyzes the impact of measuring accuracy of a key factor: slitting point setting. In the profile industry, PVC accounts for about 80% of the entire formula system, known as the big material, Ti () 2, CaCC) 3 and other auxiliary raw materials are said to fully explain the weighing process of time, weight, speed of the interrelationship between. However, in practice, the setting of the slitting point and the size of the high and low speeds are related to many factors, such as scales, raw materials, screws, the environment, etc., while also taking into account the consistency of the large and small material scales in the working process, as well as the matching of the weighing system with the entire mixing system. Therefore, from the overall design requirements of the system, the system should be experimented and optimized to determine the appropriate and correct speed slitting point, such as the slitting point is set incorrectly, it will be an important factor affecting the accuracy of measurement, but also can not guarantee the coordination between the three speeds, accuracy, production capacity. There is also a high-speed stage using a uniform feeding method, in the low-speed stage of the gradual reduction of speed feeding method, the operation is not very convenient, but can be adjusted to a high degree of accuracy. Due to the application is not very wide, will not repeat here.
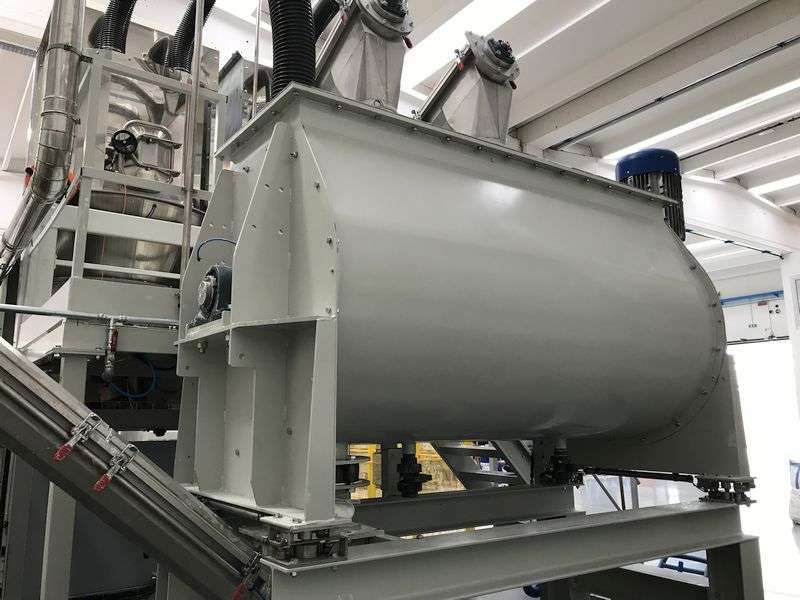

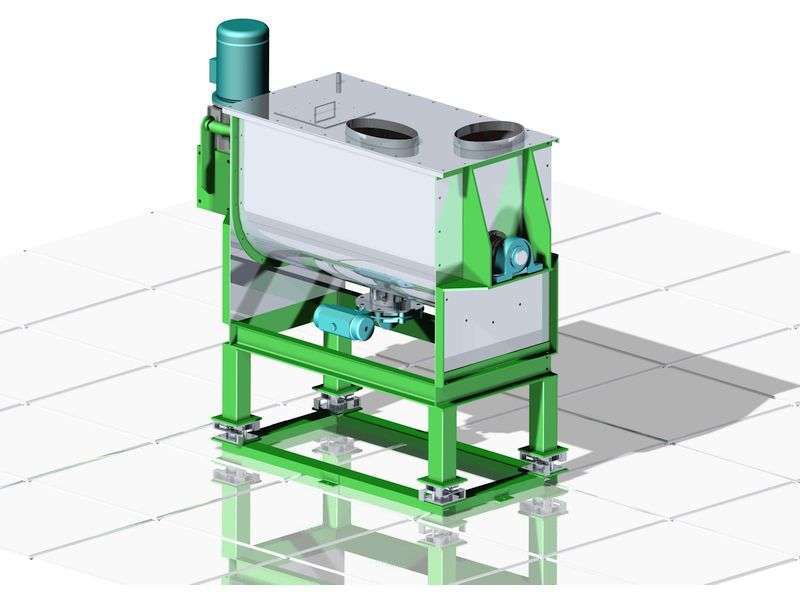