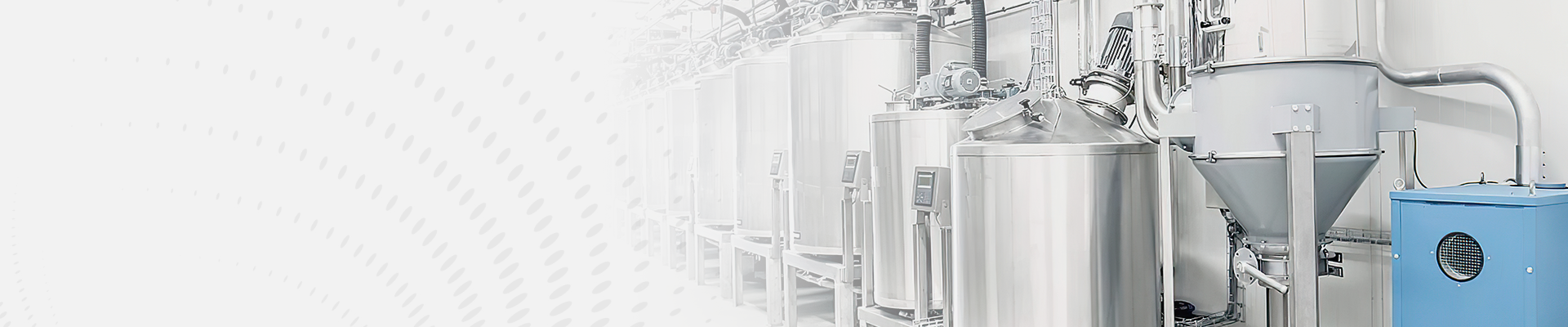
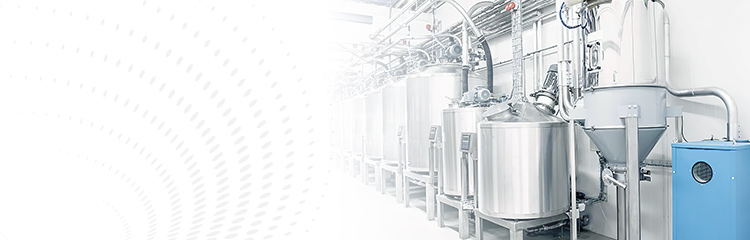
自动配料系统就是根据人为的控制指令和设定,通过微机控制来实现自动配料和自动称量计重的目的,按照所称原材料的性质主要分为大料称量、小料称量及微料称量,其中小料称量是三种称量中最复杂最重要的。称量系统是混料系统的核心部分,设计好坏将直接影响整个混出的干混料的品质,从而影响产品的性能(如颜色不正常、成品的尺寸不稳定、挤出工艺不稳定、机械性能不稳定等)。自动称量精度的控制又是整个称量系统控制的关键,如果自动称量精度不高或不稳定将直接导致实际称量的不准确和配方的配比失常,直接影响干混料质量的稳定性和成品的质量。
称量过程控制
1、过程控制
小料称量、微料称量、大料称量的工作过程控制的概括,曲线化,具有典型性,重量随时间逐渐增加变化,直至达到或接近设定值,最后卸掉恢复为0的全过程,它表示的是称量系统对一种原料的单批称量过程控制,如果连续称量将是该过程的重复。整个称量过程基本上可分为二个称量阶段,分别由二种速度控制下料,速度的分切点由预先设定的二个数值G虹、G2决定,G虹、G妃对应不同的原材料是不同的。对不同生产厂家的混料系统中所使用参数的概括,针对不同的系统和不同的具体使用条件,称量过程控制中有关具体时间参数的设定会有些变化,但变化幅度不大。
2、测量链的构成
构成整个称量投料系统的测量链主要有以下部分组成:传感元件(传感器)、连接成分(如屏蔽电缆等)、A/D转换器(输入端有放大作用,带触摸显示屏)、计量控制、配方输入控制、控制单元(计量装置)。其中A/D转换器对输入信号有放大作用,把输入的模拟信号转变成数字量并反馈至PLC或更高级别的控制系统实现闭环控制。
3、过程控制分析
整个称重控制系统可分为小料称量、大料(PVC)称量、微料称量(工作原理与小料称量相似)。系统称量过程又可分为自动称量和手动称量。
当系统处于自动状态下,首先从PC机上输入配方,不同的配方对应不同的编号,输入配方编号到要生产的相应菜单上。生产的操作程序为选择好相应的生产线,然后激活StartRecipe,系统就自动开始称量。在自动称量前,系统要自动检测将要称量的秤体上的重量参数,看是否超出系统中所预先设定的值。由于在正常情况下称量系统是连续称量,且每批料绝对下净是不可能的,加上秤体周围的干扰和故障等原因,应根据实际使用情况对每个秤的0参考点(空载重量参数)设定一个正负偏差,在偏差范围内就默认为秤是空载,系统可以正常开始称量。若秤上的重量参数超出偏差范围则不称量,系统报警提示秤体未空,这时需要检查是否是因为秤体内的原料未下完,或秤体故障,或参数设置不合理,或秤体需要重新校准其参考点等原因造成的。
因为PVC型材的一个配方体系中必须含有大料称量和小料称量,当系统处于自动状态下,启动配方称量体系时,大料称量和小料称量同时开始,称量过程互相独立,但只有两种称量全部完成才能算一批料称量完毕,才能有下料信号。大料称量只有一个PVC成份,称完该成份就算大料称量完,然后系统将自动检测其称量精度(称量误差)是否在预先设定的范围内(<+0.5%),若超出设定范围,系统将报警提示实际的误差值,以供紧急处理(手动加料或放料)。正常情况下,小料由几种原料成份组成,系统自动称量时将严格按照配方体系中设定的先后顺序逐一称量,每个成份称量间有5〜10s的延时间隔。正常情况下,每种成份的称量过程都是先高速、后低速。高速称量时快速下料,称量的比重占成份的大部分;低速称量时低速下料,称量的比重很小,主要是控制称量精度。称量时需预先在菜单参数和程序中设定好高低速称量转换的分切点Gi及高低速的大小。针对不同原料,高低速称量转换的分切点及高低速的大小可能都不一样,这要视具体情况而定。每种成份的原料称完后都要检测其称量精度(称量误差)是否在预先设定的范围内(W±(0.2〜0.3)%),正常则连续称量下一种成份,若超出设定范围,小料秤将报警,提示实际误差值,以供紧急处理。当大料、小料称量都完毕,秤体才下料,下料后,系统还将通过自动检测秤体的重量参数是否超出预先设定的空载重量参数来确认秤体上的料是否下完。由于种种原因空载时秤上的重量参数不一定为0,空载重量参数要根据具体情况而设定。如果实际重量参数大于设定值,秤将保持下料状态,直到秤上的重量参数在设定范围内,才能算下料完毕,才能进行下批料的称量。
当系统处于手动状态下,所有的称量和下料都要人为一步一步地操作,称量前系统不检测秤上的重量系数,称量时在SelctionMenue菜单中选择要称量的秤,设定要称量的重量数值后,选择相应的料罐(原料)。激活startWeighing,系统就自动完成该种原料的称量,称量后系统要检测实际称量重量,如果称量误差超过设定的范围则系统报警并提示实际误差值,以供手动补齐或卸掉多余的料。手动情况下,每种原料的称量都是按此程序进行,当全部称完要下料时,也必须选择相应的混料机,激活Discharge菜单,才开始下料,下料完成后系统要检测秤体内的料是否下净,同自动称量情况下检测原理一样。
整个称重控制系统重量参数的检测是通过测量链来实现的,根据PLC程序中预先设定的参数驱动变频器来调节速度的大小,由变频器再驱动螺杆调速电机或高速旋转阀,达到控制下料的目的。
小料称量和大料称量虽然过程互相独立,但必须全部称量完才能有下料信号。这就要求在设计称量系统和设定具体参数时要整体考虑,既要考虑各自称量的称量精度,又要考虑二者称量过程的一致性,即二者称量过程的时间要接近。减少称量过程中因一方称量快,一方称量慢造成相互间等待而延长整个称量过程时间。同时,在设计称量系统和设定具体参数时还要考虑称量系统是混料系统的一个组成部分,既要考虑称量能力与混料能力的匹配性,又要合理设计整个称量过程,不要造成称量过程过快影响称量精度及系统的良性运行,而等待时间过长。因为当混料机热混内有料时,即使称量系统已全部称好,配料系统也不会发出下料信号,必须等热混中的料全部下完才会有下料信号。另外,称量过程也不能太慢,虽然称量过程慢有助于提高称量精度,但是这样可能造成混料机下完料后等待称量,浪费混料时间,影响混料机混料能力的发挥,影响整个混料系统的生产能力。
称量误差分析
1、配料精度组成
称量系统的系统影响各个精度的因素也是系统产生误差的主要原因。为小料。大料称量可分为正压输送称量和负压输送称量,小料称量则是通过PLC来控制变频器,从而使调速电机带动计量螺杆按照设定的速度运转下料。在当前的自动称量系统中,绝大多数的称量过程都分为粗加料和精加料两个阶段,所以无论是大料称量或小料称量,都涉及到一个粗加料(高速加料)与精加料(低速加料)的分切点设定问题。
称重设定值是高速和低速的一个分切点,如图4所示,此数值在称重前已预先被输入在PC机里。粗加料阶段的加料速度是吼,这样既可以减少了称重时间,同时也称重了整个重量的大部分;到达分切点时,步入了精加料阶段,加料速度是吼,这样既可以称完剩下的一小部分原料,同时也控制了精度。
称量系统的误差分析是整个系统控制的核心,它决定称量系统的可靠性和精度,从而会影响整个混料系统的生产质量和生产能力,所以它是确保产品的性能和稳定的源头。系统误差产生的原因很多,如传感器的精度、原料成份、环境、设计的程序、设定的参数因素。
2、分切点设定
系统精度分为加料精度和静态称量精度,加料精度又细分为称量精度和系统影响两个方面,而计量精度的高低将影响称量精度的高低,由于篇幅有限,本文仅分析影响计量精度的一个关键因素:分切点设定。在型材行业里,PVC大约占整个配方体系的80%,被称其为大料,Ti()2、CaCC)3等辅助原料被称其充分说明了称重过程中时间、重量、速度之间的相互关系。然而在实际应用时,分切点的设置和高低速的大小与许多因素相关,如秤体、原料、螺杆、环境等,同时还要考虑到在工作过程中大料秤和小料秤的一致性,以及称量系统与整个混料系统的匹配性。所以从系统的整体设计要求出发,要对系统进行实验和优化来确定合适正确的速度分切点,如若分切点设定错误,它将是影响计量精度的一个重要因素,同时也不能保证速度、精度、生产能力这三者之间的协调。还有一种在高速阶段采用匀速加料的方式,在低速阶段采用的渐减速度加料的方式,操作起来不太方便,但却可以调高精度。由于应用不是很广泛,这里不再赘述。
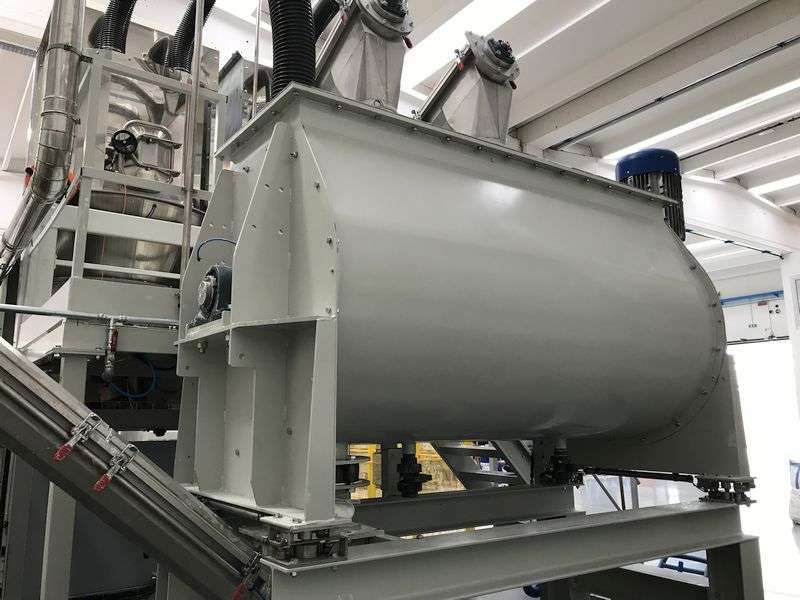

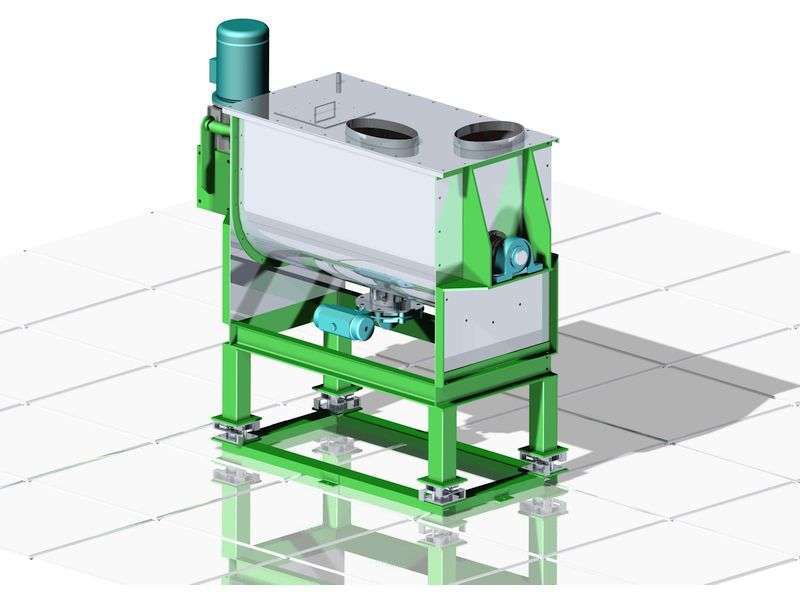