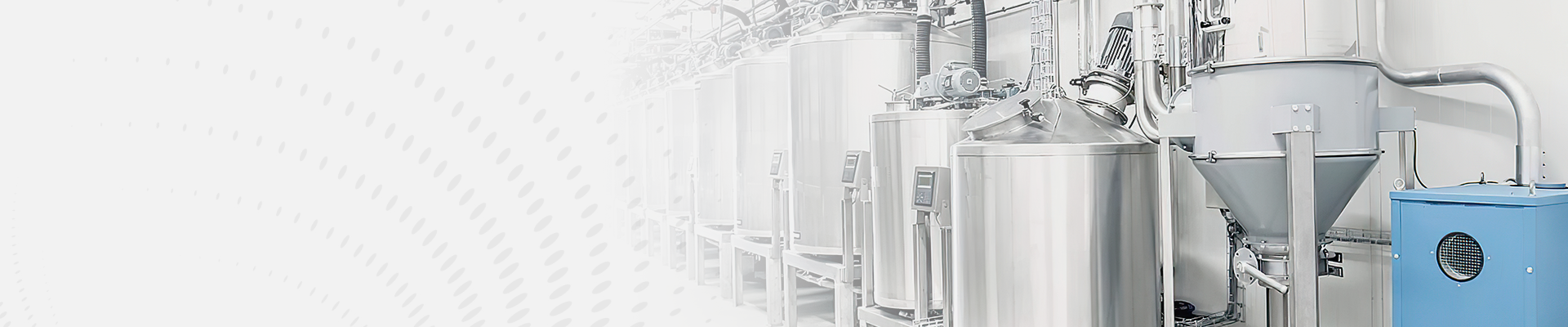
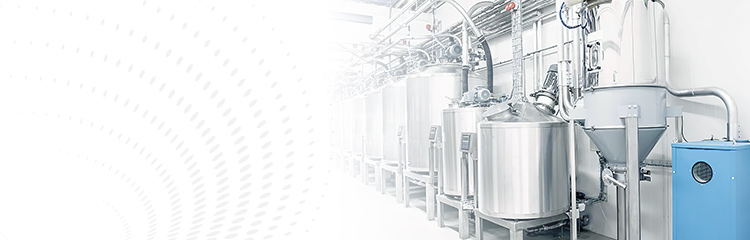
胶水自动配料系统生产线的主要工艺设备由储备反应罐(包括淀粉、碱液、树脂三个反应罐)、反应釜(包括硼砂、碱液、树脂三个反应罐及其共用的称量装置)、一个主反应罐及其称量装置和四个成品反应罐及其计量装置组成。
本胶水自动配料系统生产线设有化碱系统(采用碳钢反应罐体)、搅拌装置、电子地磅,碱液反应釜以及管道均采用不锈钢。片碱化成液碱后,贮存在碱液贮槽里。碱液反应釜的液位可以由PCC自动控制,当低于设定低限时,将自动启动碱液泵从碱液贮槽进行补给。
淀粉贮反应罐为碳钢反应罐体,配备了螺旋输送机、振动给料器,装设了高、低料位传感器。主反应罐装备了蒸气加热装置和自动温度控制系统,配置有温度检测元件、二次温度仪表和蒸气切断阀,并采用PCC来控制温度。
各用胶点贮反应罐设有液位检测和搅拌装置。各胶水储反应罐的胶水重量可以在制胶房的触摸屏上实时显示和监视。
工艺流程概述
首先从硼砂、树脂以及碱液的存储反应罐往反应釜加料:上述三个反应釜都固定在由称重模块支撑的架体上,它们共用一套称量装置。常温下树脂和碱液均为液体,它们的中转储反应罐都设有最高位和低位浮球。第一次只加树脂,当其液位到达高位浮球位置时停止加料,此时反应釜称量仪表显示的重量就是树脂的重量,也是其最大值。第二次同样也只加碱液,当其液位到达高位浮球位置时停止加料,此时仪表显示的重量减去第一次加的树脂的重量,即为碱液的重量。把这个计算出来的值保存为碱液当前重量。硼砂是固体,采用人工将硼砂加入到硼砂反应釜中,但也以同样方式计量。在淀粉的储蓄反应罐中,设有高、低料位传感器和振动器,当到达高料位时,不能再往储反应罐中加淀粉,低料位信号则提示加料。振动器的功能是把淀粉振松,振散,防止淀粉架桥。低于最低料位置时,会自动启动振动器将反应罐壁附着的淀粉振动下来。
生产胶水时,除需先后分数次往主反应罐中加入一定比例的清水和淀粉作为基料以外,其它主要就是加入硼砂、树脂和碱液。这三种配料,都是单独添加,如果当前在加碱液,反应釜的重量会变小,这个差值就是注入主反应罐中的碱液的重量。而反应釜中当前的碱液重量就是原来的重量减去注入主反应罐中的碱液的重量。保存这个值为当前的碱液重量。
其它两种物料也以同样方式加入主反应罐。
每一条纸板生产线其实只需要一种规格配方的胶水,不同的纸板生产线所对应的配方也不一样。目前该胶水设备配设了4个成品反应罐(带有蒸汽加热装置),每个成品反应罐中胶水的配方都不一样,这4个反应罐分别位于不同的纸板生产线旁,与主反应罐通过管道连接,并通过空气泵把加热后的胶水从主反应罐中吸到相应的成品反应罐中。
该系统设有配方自动修正功能,当加料时,可以通过屏幕监视加料过程中的偏差,并自动根据配方的比例修正后面的加料比例,以保证配方的准确性;可以与用户的生产管理系统实现数据通讯,通过参数设定,自动根据待生产的定单情况来确定制胶量,以减少胶水的浪费;在初次输入配方后,当用户需要调整配方的时候,无需再去计算物料的变化,只需直接输入胶水的变化结果,程序即可自动修改配方;设有自动吹胶功能,当每反应罐胶水输送完毕以后自动吹胶并复位系统,以避免胶管堵塞。
控制系统的构成与配置
称重系统构成
该配料系统以的B&R2003系列PCC为核心,采用触摸屏为人机界面,与梅特列-的PANTHER称量仪表、主反应罐温控仪表以及加水控制和淀粉输送控制装置等结合而组成。此外,该系统还配备了一些泵、切断阀、液位和料位传感器。
计量系统配置
该PCC配置了1块BP704(4槽底版),其CPU安装在底板的最左端,选用带24VDC电源的双宽度模块CP476,该模块上附有RS232和CAN接口各一个,并有状态指示灯,同时还有4个旋入式模块的插槽,需要扩展时将旋入式模块插入到插槽中并用紧固螺丝固定。旋入式模块可以是模拟量或数字量模块,也可以是通讯扩展模块。
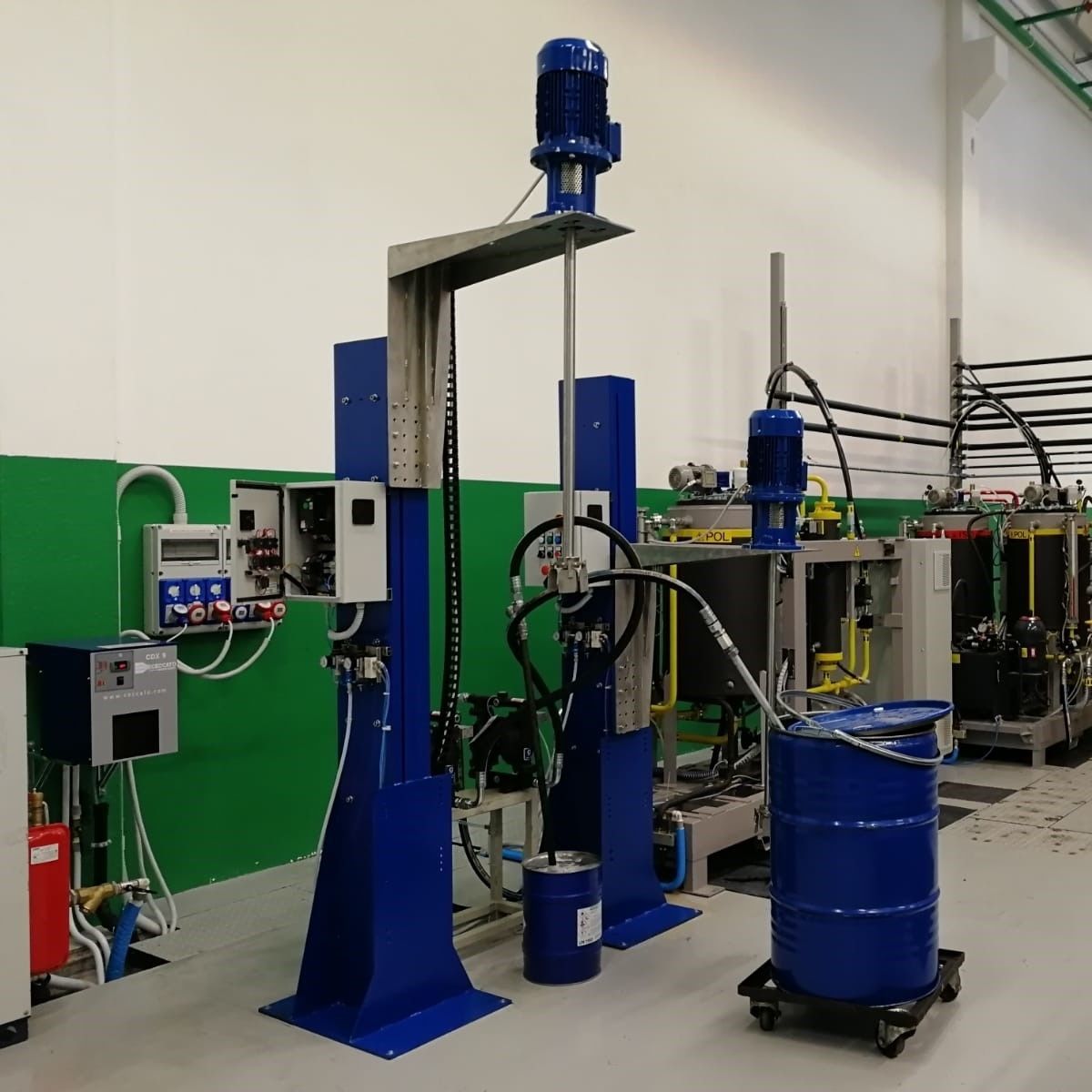
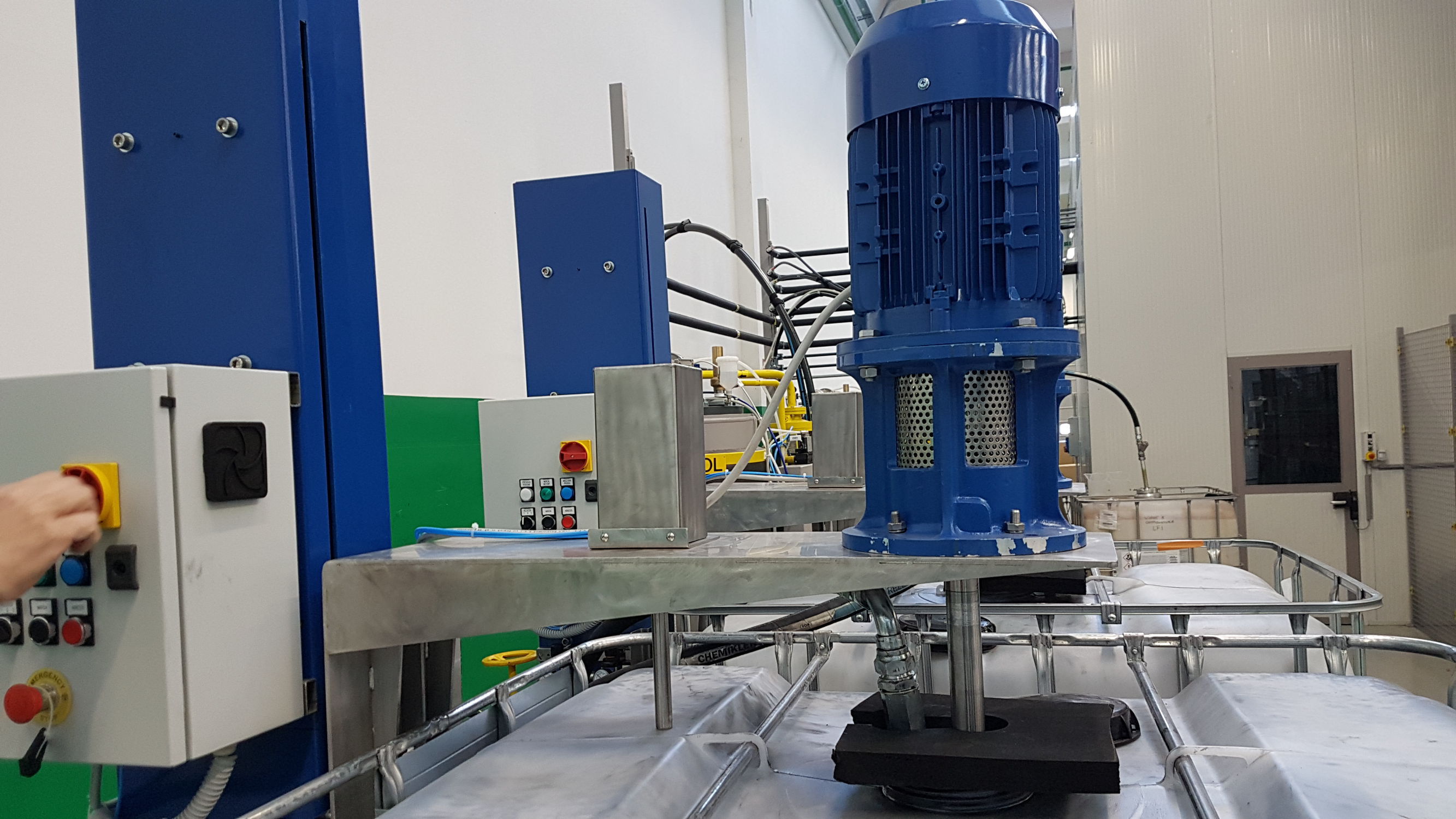
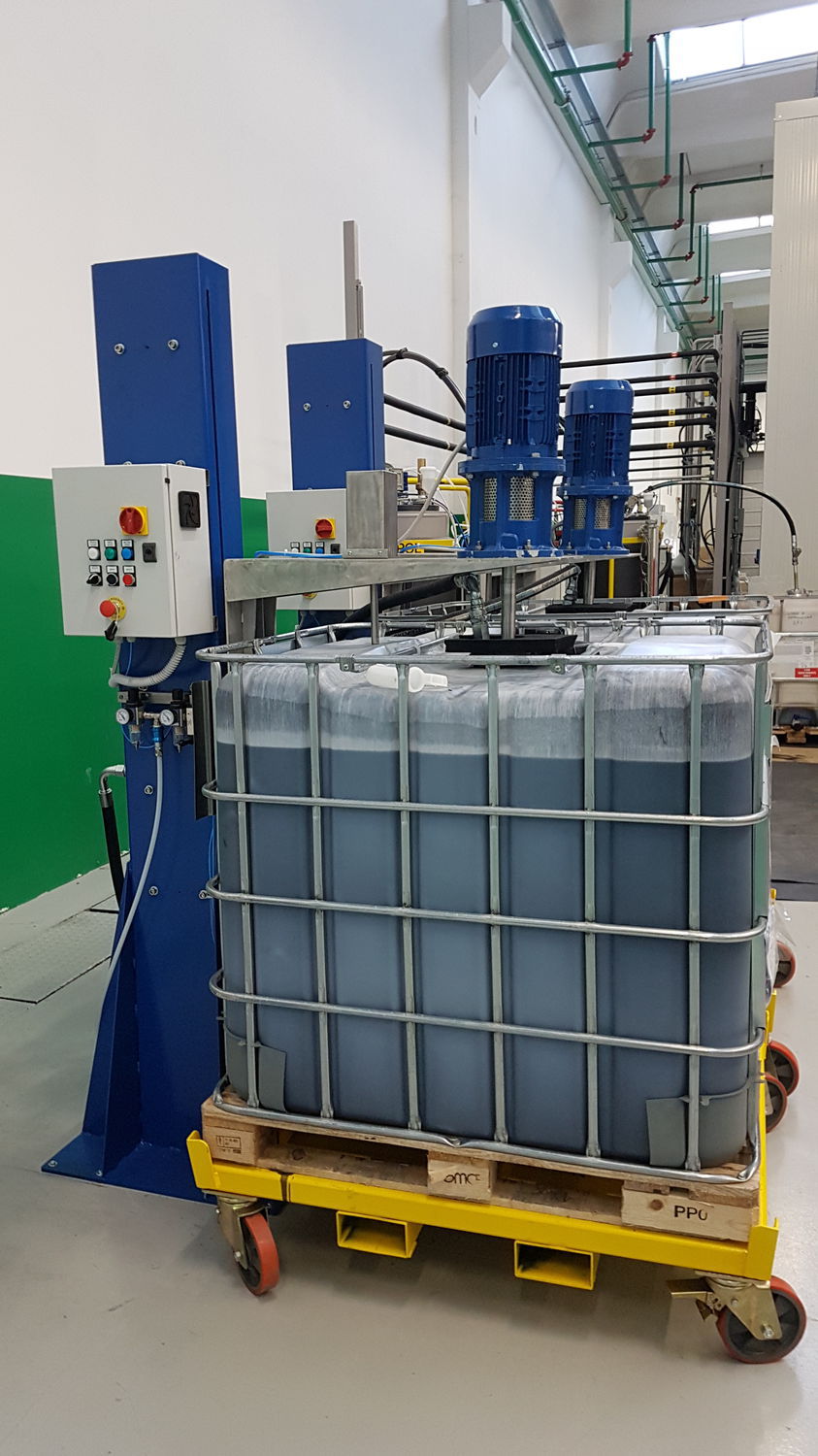
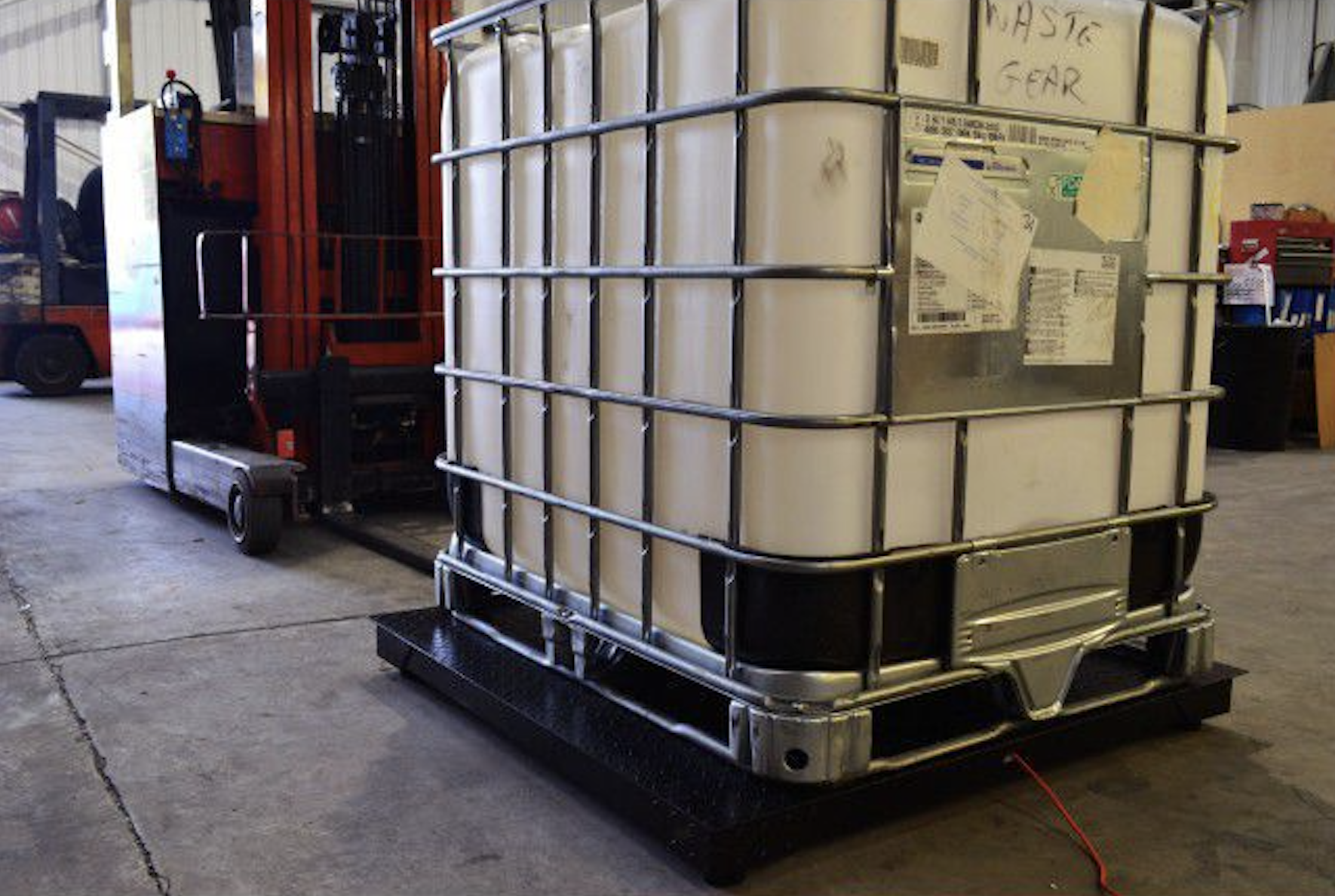

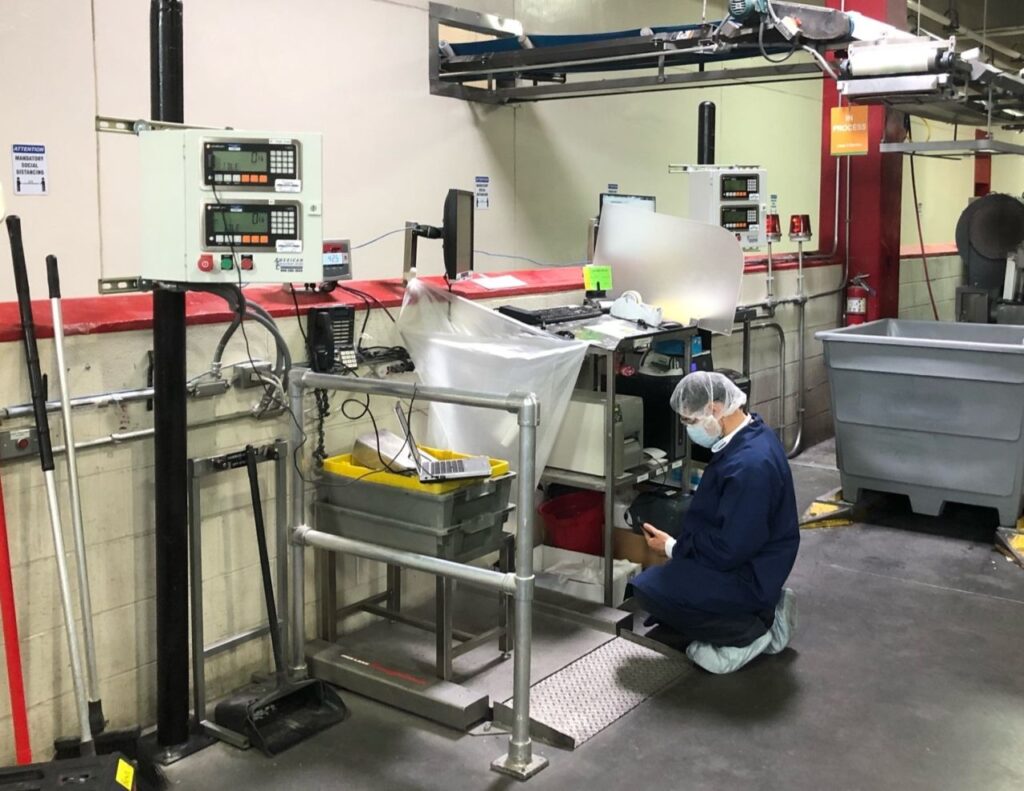