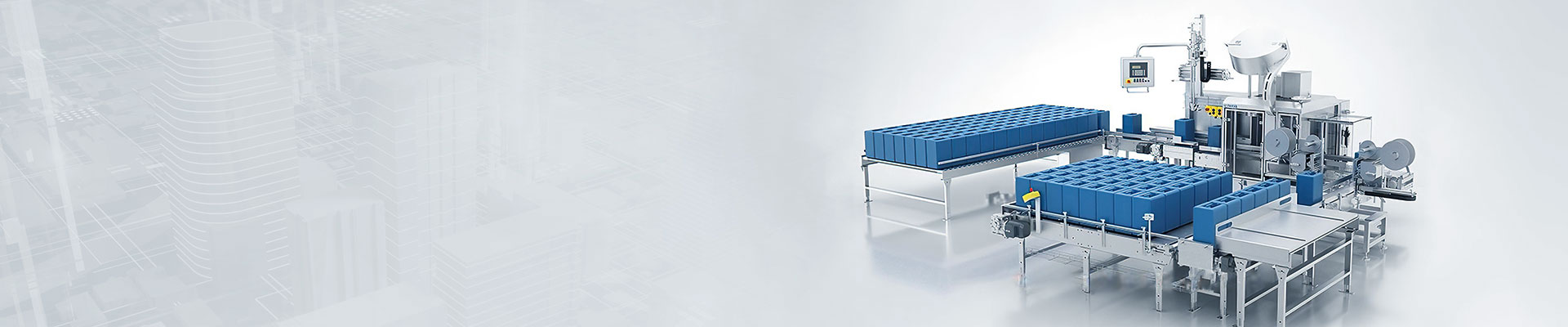
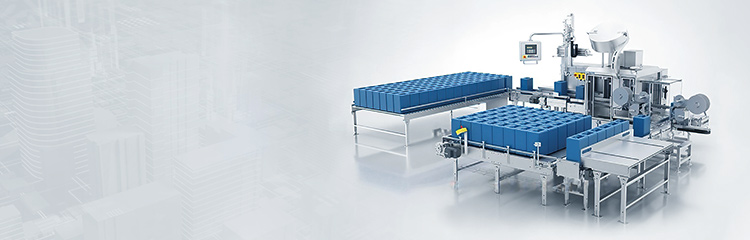

配料控制系统包括原料的储存、输送、称重配料、除尘、物料混合、包装灌装等多种设备,涉及粉状、粒状、块状、片状及液体等多种物料;其中称重配料系统可根据行业特点及工艺要求,结合物料特性,合理的选择单料配料、多料顺序累加、减重配料、失重秤配料、皮带/螺旋秤、散料秤等多种计量方式。
自动配料系统是精细化生产工艺过程中一道非常重要的工序,配料工序质量对整个产品的质量举足轻重。自动配料控制过程是一个多输入、多输出系统,各条配料输送生产线严格地协调控制,对料位、流量及时准确地进行监测和调节。系统由可编程控制器与电子秤组成一个两级计算机控制网络,通过现场总线连接现场仪器仪表、控制计算机、PLC、变频器等智能程度较高、处理速度快的设备。在自动配料生产工艺过程中,将主料与辅料按一定比例配合,由电子秤完成对输送的物料进行计量。PLC主要承担对输送设备、秤量过程进行实时控制,并完成对系统故障检测、显示及报警。
负压输送系统是输送颗粒型、粉状型、块状型物料的常用输送设备之一,易于取料,可用于从低... 在线咨询 产品详情 负压稀相气力输送系统系统输送管道配置灵活,可根据现场工况环境灵活布置,工艺流程更为合理,物料在密闭输送管道中输送,系统完全封闭,粉尘飞扬少,可实现环保要求,运动零部件少,维护保养简单方便,易于实现自动化,散料物料输送效率高,降低了包装和装卸运输费用。 系统简介 负压稀相气力输送系统是输送颗粒型、粉状型、块状型物料的常用输送设备之一,易于取料,可用于从低处、深处、狭窄取料点以及由多处向一处集中送料的场合,适用于取料不发尘的场合。山东拥有多年负压稀相气力输送行业经验,可针对具体气力输送项目做出精确的输送参数确定和管道优化设计,以降低气力输送中的各种气力输送因素影响。根据负压吸送气力输送系统的原理开发出多组分吸料计量称,满足不同客户的需求。
工作原理
负压气力输送系统主要由气力输送风机、取料装置、上料器、管道、卸料装置等结构取出,其工作原理:
1、负压气力输送系统主要采用罗茨风机或真空泵作为气源设备,气源设备装在系统的末端;
2、气力输送系统取料装置部件通常采用吸料枪、体积喂料机;
3、风机运转后,抽风整个系统形成负压,由管道内外存在的压力差吸入空气进入熟料管,物料和一部分同时同时被吸嘴吸入,并被输送到真空上料器中;
4、在真空上料器中,物料和空气分离,被分离出来的物料从真空上料器底部卸出;
5、未被分离出来的微细粉粒随输送气流进入排尘器中净化,净化后的空气经除尘器排入大气中。
系统优势
1、负压稀相系统具有气力输送量大、输送距离长、输送速度快等特点;
2、系统易于取料,适用于从低处、深处、较为狭窄的取料点取料,可用于要求取料不发尘的场合,可实现多出上料向一处集中供料。负压稀相气力输送系统适应性广,用途广泛,粉体、颗粒物均可顺利输送;
3、系统造价低,制造维护要求低,系统运行稳定、工人可操作性强、运行成本低、管路物料残留少,负压稀相气力输送系统尤其适用于一般气流干燥工艺过程中输送和食品行业的食品物料输送;
4、系统气源位于末端,润滑油或水分等不会混入被输送的物料中,负压稀相气力输送系统输送物料更清洁;
5、系统由于输料管内部为负压,因此及时系统管道产生磨损和存在间隙时,被输送物料也不会发生泄漏,此外,由于负压稀相气力输送系统内压力低于大气压力,水分更易蒸发,所以对水分多的物料较压送式更容易输送;
6、系统输送气体一般直接取自大气,气体的温度即为环境温度,因此负压气力输送系统尤其适用于对温度敏感的热敏性物料;
7、系统输送为连续式输送,亦可间断,管道内无物料积存,采用负压气力输送系统输送物料对环境污染小;