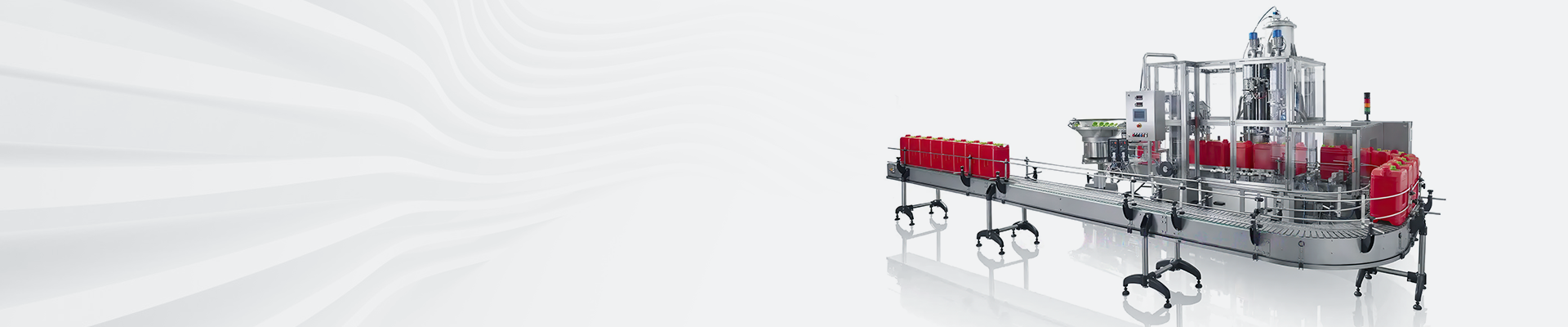
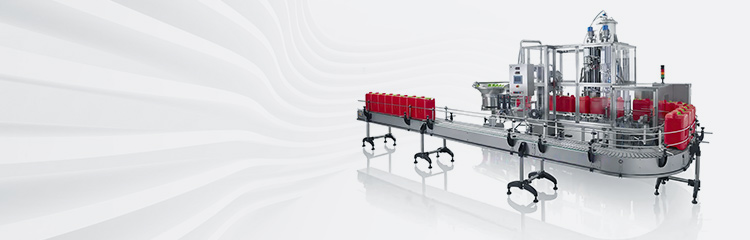
摘要:PLC对高料仓配料称量过程进行闭环控制,通过软件实行了称量参数的自动修正和称量误差补偿。
高料仓配料要求人工料仓称量准确、原料配比合理,但在高速上料的情况下,由于物料流动的不稳定性和机械惯性造成的纯滞后存在超调,给控制的精度带来很大困难。并且由于开环称重的误差是单向的,累积误差非常可观,这直接影响到料仓的控制和配料的成本。因此,本系统设计了一种控制方法,利用PLC对称重过程进行闭环控制,并通过软件自动校正称重参数和补偿称重误差。首先,它根据每次称重产生的最大误差值,即提前停止给料设备的时间,调整下一次称重的控制值。使实际装载尽可能接近设定重量,以减少每次称重产生的最大误差。其次,根据每次称重的误差值,修正下一次称重目标值并补偿称重误差。
1称量过程中的控制算法设计
(1)每次备料前自动计算计划重量和充满度控制值。
料斗秤每次配制前,根据料斗的设定重量(该值由高料仓工长根据配料流程计算,并以物料清单的形式输入PLC)和上次称重误差需要补偿的重量(算法由PLC自动计算),计算出计划配制的重量。
为了减少由机械惯性和给料设备的残余振动引起的装载偏差,PLC必须通过提前发送满信号来停止给料设备,该信号在料斗秤的重量达到满控制值w时发送。只有这样才能确保称重误差最小化。
(2)每次秤斗放空料后自动计算出实际净装料量和装料偏差。
当料斗秤装满物料时,准备过程结束。当进料程序选择要卸料的料斗时,称重漏斗闸门打开卸料,电子称重量自动跟踪。当料斗清空时,会发出清空信号,称重漏斗闸门关闭。在卸料过程结束时,测量电子秤中剩余悬挂物料的重量,即称量料斗的空重。当称量斗装满物料时,可以测量称量斗的全部称量重量。因此,可以计算净装载重量和装载偏差。
(3)自动优化下次料满提前量。
为了减小误差补偿的幅度,关键是选择合适的满料提前量,使每次称重产生的误差尽可能小。在称重结束时,可以计算装载偏差,并且装载偏差可以用于校正每种材料的下一个材料充满提前量。如果由于偶然的非正常因素导致偏差超出正常允许范围,那么上一次垫款仍将作为下一次垫款。
在实际生产中,视不同设备、不同品种而不同,可以手动设定。这样,就可以利用这种装载偏差来修正下一次物料准备的提前满载物料,以便更合理准确地计算出物料满载控制值,从而使实际装载的物料量接近计划装载的物料量。下面的公式是计算物料全额预付的公式。
校正系数的值越大,校正的速度越快,但过大则容易出现振荡现象;该值越小,校正速度越慢。校正系数值的大小与原料颗粒的大小、进料速度、进料设备、物料的残余振动量、物料的冲击大小有关。如果原料颗粒大,进料速度快,冲击力大,该值宜取小一些,反之则取稍大的值。一般取值在60~90%之间,视不同类型的材料略有不同。
(4)自动计算出下次补偿量
在每次料斗秤斗放空,装料结束后,自动计算积累误差,根据积累误差计算下次补偿量。原则是本次的称量积累误差应尽量从下次称量中得到补偿。但一次补偿量过大,可能会超过料斗称所允许的极限装料能力,并且在工艺上也不允许,遇到此种情况时,先按最大补偿量(可人工预先约定的值)进行,而剩下的(称之为欠补值)从以后各秤中逐称补偿回来。
综上所述,各种因素所形成的误差,通过以上的补偿和控制措施,便能达到所需要的称量精度。若干次装料后形成称量误差累计量等于最后一秤的称量积累误差。
因此,随着称量次数的增加,其总的称量误差不会越积越多。通过不断优化料满提前量,准确计算装料控制值,使每次的称量偏差降低到最低限度,对产生的误差及时予以补偿,从而达到了自动称量补偿的目的,保证了连续称量的精度。
2称量过程的PLC软件程序实现
当料斗被认为是空的时,由称重仪表和料斗的卸料门发出的零位信号确定料斗关闭。振动筛或电磁给料机由PLC控制打开料斗进行给料(同时相应设备同时动作,如皮带等。).当物料达到预设值时,PLC控制停止进料。当料斗处于满载状态时,根据程序控制指令,如果需要物料,通过PLC控制打开闸门,启动物料输送系统向中间仓进料。当材料为空时,闸门关闭,进料停止。
称量过程按工艺顺序可分为备料过程和放料过程,这里分别对这两个过程的程序设计作一介绍。
(1)备料过程
开始备料过程的条件:料斗秤已清空,闸门已关闭(卸料过程结束)。根据算法,计算出本计划的备料重量和物料全量控制值,然后发出启动投料设备的命令。进料设备工作,料仓中的原料不断装入料斗秤。当料斗秤的重量达到或超过物料满控制值时,程序会发出“物料满”信号。停止给料设备,延迟几秒钟,当给料设备停止且残余振动结束时,此时将称量斗重量读入称量斗满称量寄存器,结束备料过程。
(2)放料过程
备料过程结束,称量斗已满,投料设备已停止工作。根据进料程序,轮到料斗秤卸料。程序发出打开料斗秤闸门的命令,驱动外部控制电路打开闸门。料斗秤中的原料通过闸门或通过给料皮带直接装入给料小车,料斗秤的重量继续下降。当称量斗重量达到或低于空料控制值(该控制值为常数,手动设定并输入PLC寄存器)时,程序发出“空料”信号,延时数秒,关闭称量斗闸门。此时,称量斗已经清空物料,称量斗重量为空称量重量。然后根据上述算法计算下一次全提前量、累积误差和下一次补偿量。
3结语
通过设计PLC软件程序,实现了对上料系统称量补偿的工艺改进,具有实际应用的现实意义。