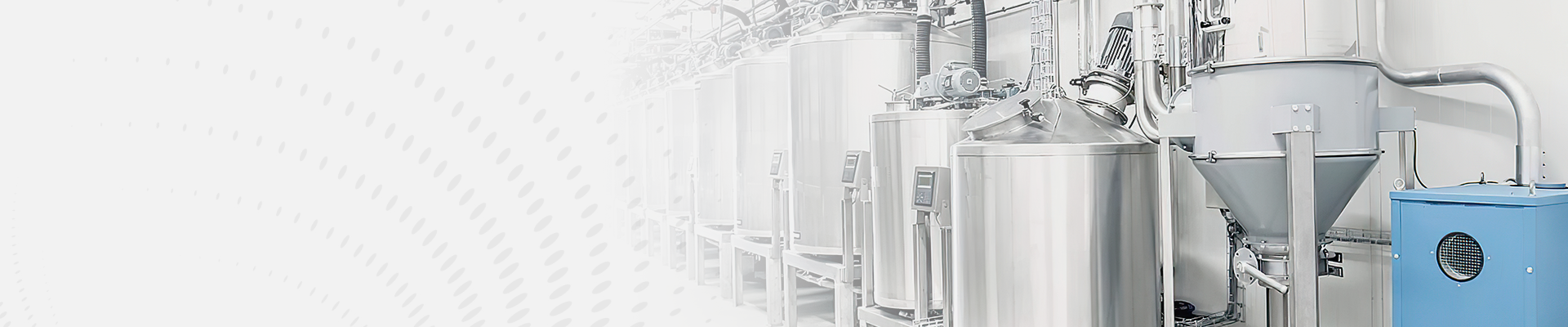
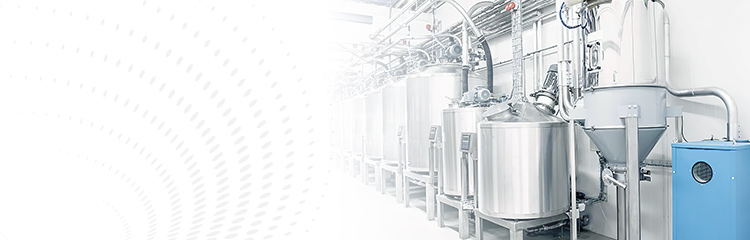
引言
反应釜是化工生产过程中关键配料设备之一,由于反应釜内部化学反应机理较为复杂,外界条件、原料添加数量的变化、加热及冷却水温度的变化等对系统影响较大,使系统本身具有较大的时变性、非线性和时滞性,因此,受到过程控制领域的研究所关注。在此,以某中日合资企业防锈油(蜡)项目为背景,结合目前国内外先进的自动配料系统技术,在反应签的进料控制中,提出了质量计量的控制方案,取得了理想的控制效果。
1控制方案的确定
1.1工艺要求
日方公司提供的工艺为典型的精细化工过程,原料配比>反应过程>计量包装,此工艺自动配料控制系统过程中涉及多个控制回路,主要包括原料配比控制回路、反应过程中温度控制回路及成品计量包装控制回路。项目选用蒸汽加热反应釜来完成工艺过程的反应。工艺添加原料的顺序为:先将液体反应物料加到反应釜中,再把介质温度加热到稍高于反应温度或固体反应物的熔点;在不断搅拌的情况下,慢慢添加固体反应物,让它不断反应或溶解避免发生沉淀。由于配方的不同,每种产品需要液体原料4种左右,固体原料2种左右,配料比要求达到0.1%。
1.2原控制方案分析
日方公司原控制方案为4个储罐通过泵向反应釜内加料,主要配比通过齿轮流量计流量计量、温度补偿、密度标定实现对原料质量的测量,在每根管线进反应釜处设置一台切断阀与流量进行联锁,每个反应釜的流量计采用4~20mA标准信号进人控制室的PLC内,控制室内PLC根据设置的配方比例控制实现进料的自动计量。
研究发现,原控制方案存在如下缺点:
1)因输送原料需要蒸汽伴热(原料凝点较低),输送管线较长,含有较大的固体颗粒,导致流经流量计的液体密度不稳定,流量计内部元件磨损率较大,无法实现工艺的0.1%精度要求;
(2)罐区到生产广房有一定距离,在北方地区寒冷季节蒸汽伴热无法使管道内介质温度均匀,不能确定具有代表性的温度检测位置,这种情况下流量计量的控制方案得出的质量误差更大;
(3)流量计的日常维护需要耗费较多的工时。
1.3改进的控制方案
针对上述方案缺点,在对工艺过程论证、方案投资比较的基础上,提出质量计量的控制方案,即称重配料系统的应用。
称重投料系统主要通过称重仪表实现。由于称重仪表带有定值比较功能,可以直接用于物料自动分拣、筛选、散料定量包装、生产配料、灌装、物流进出货等过程控制,已被广泛应用于医药、原材料加工、石油、化工等领域。
2称重系统方案的实现
2.1称重控制系统硬件组成
2.1.1称重模块
为了精确地反映质量的变化,改进方案称量模块采用某公司的高端过程FWC系列计量模块。传感器由承压头和现场接线盒组成。承压头安装在反应釜侧面成120°分布,反应釜的重量均匀压在每台承压头上。3个传感器以MV的形式进入到现场接线盒中,现场接线盒把3台传感器信号进行累加转换成标准的4~20mA标准电流信号送到称重仪表中。2.1.2称重仪表
为了更好地满足现场恶劣的工业环境运行的要求,称重仪表采用PANTHER称重终端,PANTHER称重终端所具有的TraxDspTM数字滤波专利技术能够实时地得到稳定的重量值且具有金属外壳,可以安全地应用于反应釜使用条件,满足现场安装要求。通过称重终端可以在现场完成称重值的校零、校满、去皮重等功能。另外,仪表选配Profbus-DP现场总线接口,与控制室的PLC高速通讯,把重量数据送到PLC中去参与计量控制。
2.1.3输送泵和计量控制间
输送泵采用密闭式电机,通过PIC自动控制输送泵的启动和停止。计量控制阀选用调节阀,通过PLC发出4~20mA标准电流信号控制调节阀的开度。当信号为4mA时,阀位为全关状态;当信号为20mA时,位为全开状态。阀位的开度控制设计根据进料余量的大小采用自适应的控制策略。当进料接近结束时,阀位可以适当关小,当达到设定质量时全部关闭,保证进料的精度。
2.1.4可编程控制器(PLC)
控制器选用三菱的0系列中型PLC完成对反应釜的进料称重控制。PLC选用4种模块:开关量输人模块,接收现场称重开始指令、急停指令和泵开启状态;开关量输出模块,发出启动输送泵指令和现场计量指示;模拟量输出模块,调节计量阀的开度;Profibus-DP通讯模块,主要与称重仪表通讯,采集仪表质量。
2.1.5工业计算机
工业计算机通过RS232口与PLC通讯完成称重配方的设定、整个配料系统状态的监控、计量数据的保存和打印,实现控制室内完成进料自动计量。
2.2称重控制系统软件实现
2.2.1PLC软件编程
PLC通过专用编程软件GXDeveloper对其编程控制逻辑用梯形图写入PLC中进行运算控制,其逻辑结构:开始>载入配方>设定进料值>设定值为零>按进料控制钮>打开进料泵>延时打开进料泵>到关闭进料泵值>关闭进料泵>到关闭进料阀>延时等待放料结束>记下实际放料值。
2.2.2Profibus-DP通讯软件
Profibus-DP通讯协议具有通讯速度快,抗干扰能力强,有纠错能力的特点,并且三菱PLC和PANTHER称重终端都具有符合Profbus-DP通讯协议的接口。现场设有5台PANTHER称重终端,分别设定1~5地址号,在PLC中Profbus-DP接口设定0地址,通讯波特率位1.SMBP,保证数据刷新周期小于0.1s.2.2.3友好界面编程。
(1)工业计算机通过RS-232口的形式与PLC交换数据包括计算读取PLC中的现场设备控制状态,进料计量的进程,故障报警等;计算机把控制数据送到PLC中,如计量质量、阀关闭质量、泵关闭质量。
(2)现场设备状态显示。现场运行状态采用动态时时跟踪,可以直接监视反应釜的质量、输料泵的运行状态、计量控制阀的开度、已经进料状况等,图5为现场显示示意图。
(3)配方编辑。工人可以完成对配方的新建、修改、删除、调人等操作,设定计量料的质量值。每个配方可包括料的名称和设定质量,即方便工人设定质量又不容易操作错误。
(4)计量质量打印。当全部配方进料结束后,打印全部的设定质量和实际放料质量。
(5)数据保存。方便查看历史配料记录,以便子跟踪质量。
运用称重上料系统方案的效果
采用称重控制方案,在减少温度补偿、密度标定两个环节的同时,完成添加剂小质量的添加也通过质量控制实现,使原料配料精度提高到0.8%o,完全满足工艺要求;每个反应金减少了3台切断阀,节约了投资;总线方式保证控制室内与现场仪表无偏差,并且不受其他信号干扰。该控制方案受到日方专家认可与肯定,日方表示要根据此方案对日现有生产线进行部分改造。
4结论
该项目提出的称重模块喂料系统进入反应釜的进料控制方案,完善了整个工艺系统的运行能力和水平,提高了控制系统完全集控运行的能力和可靠性,确保了产品的高品质,研究与工程应用有较强的实时性和稳定性,对类似化工企业的生产过程控制有一定的借鉴意义。
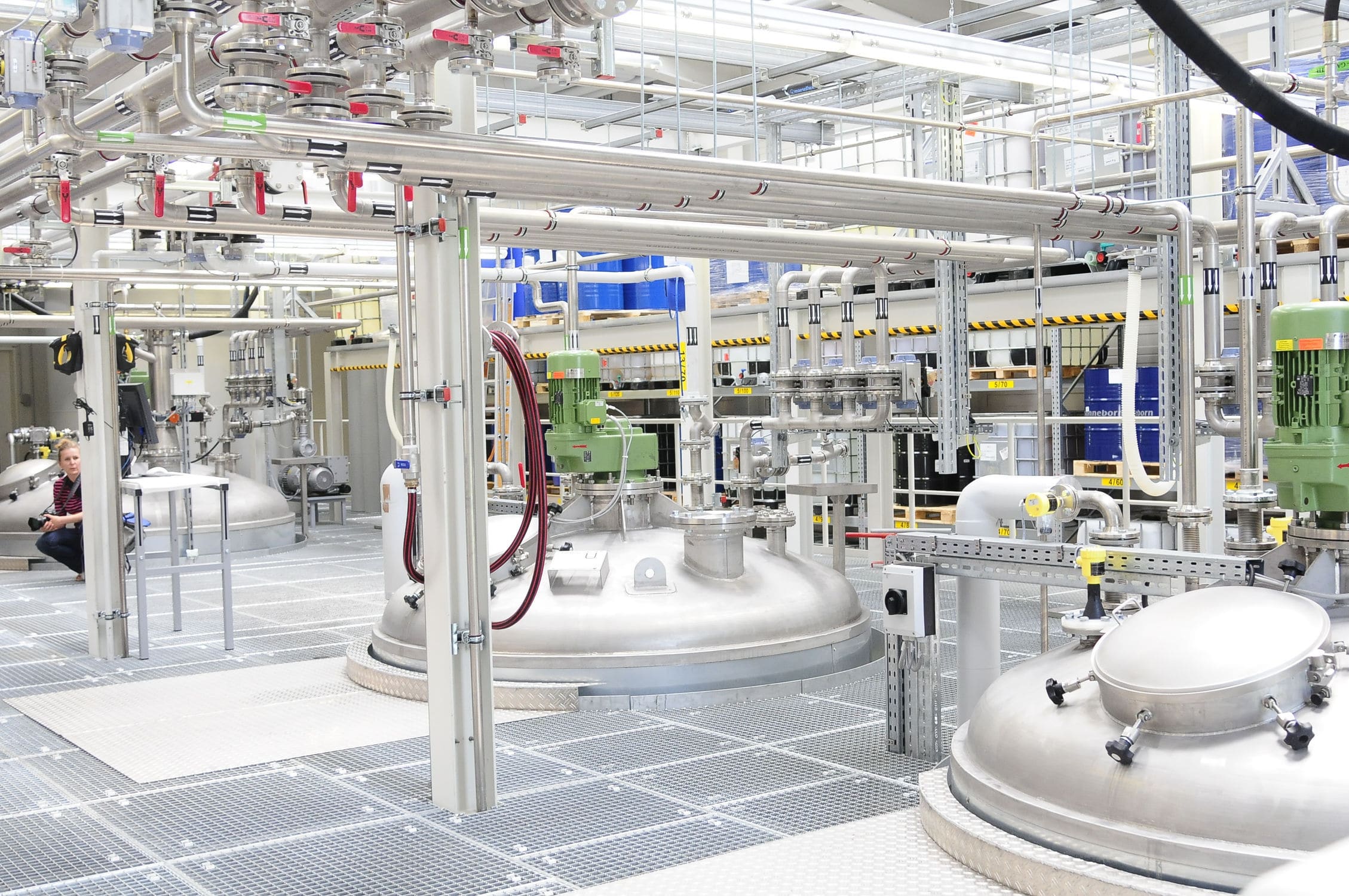
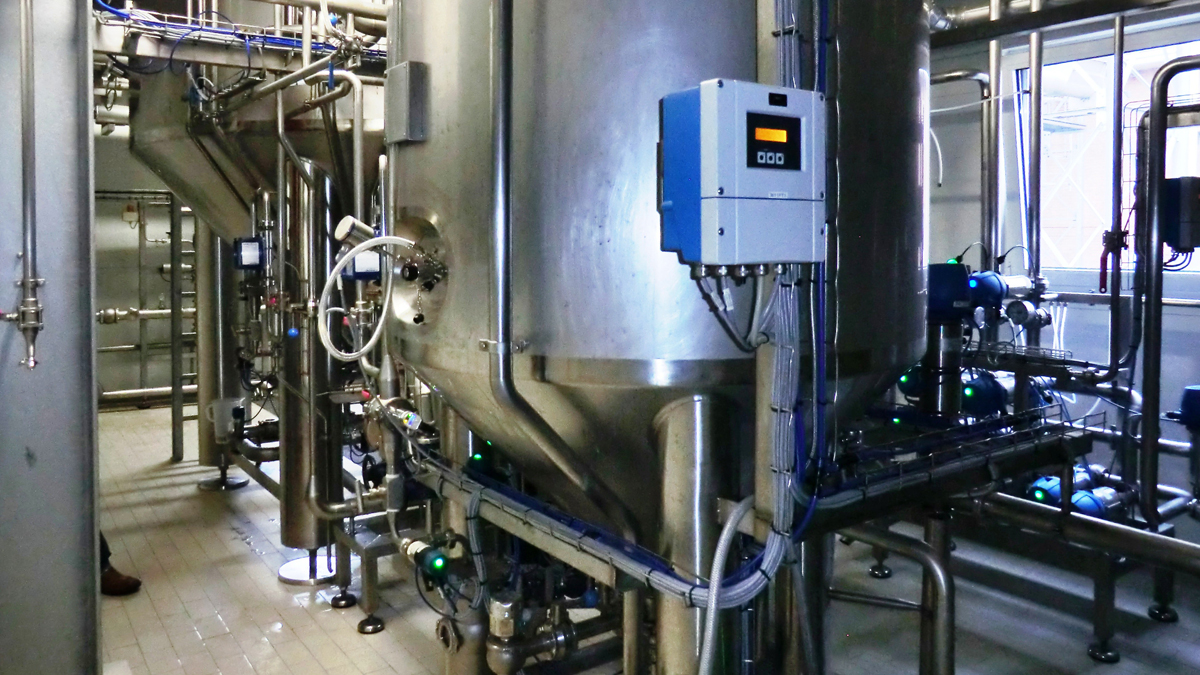
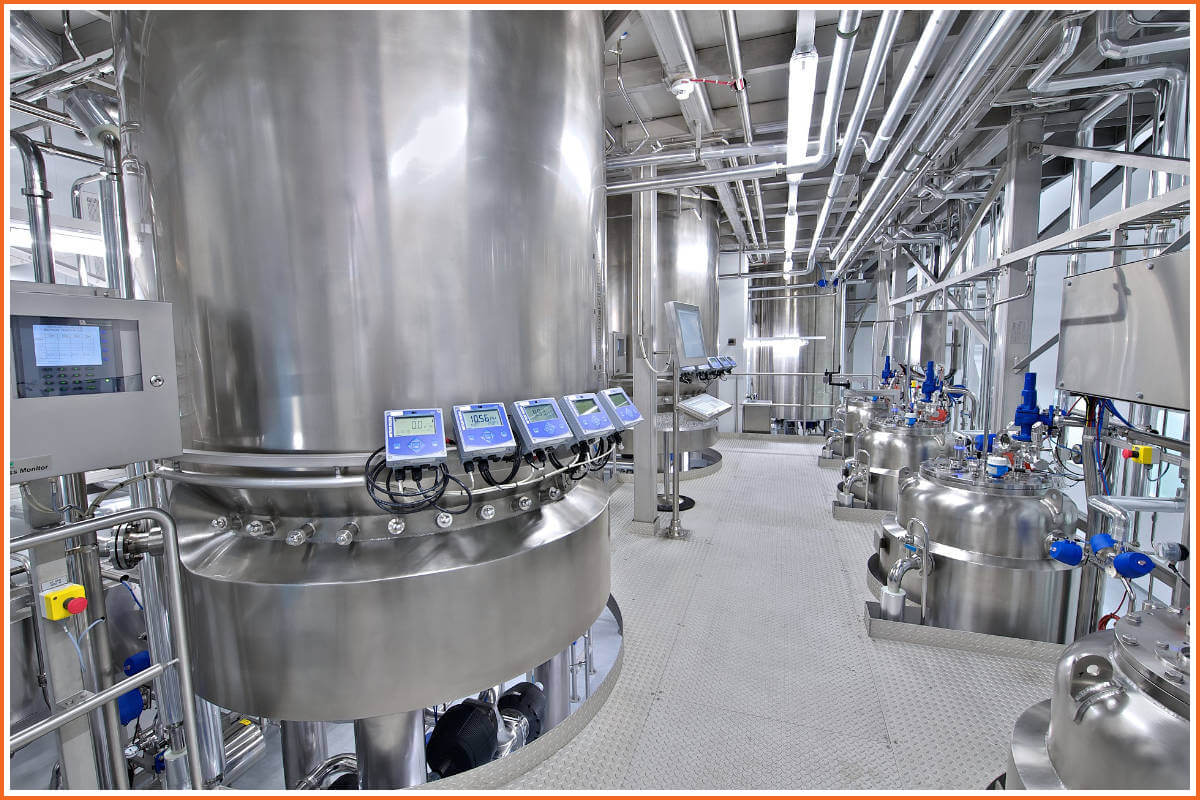
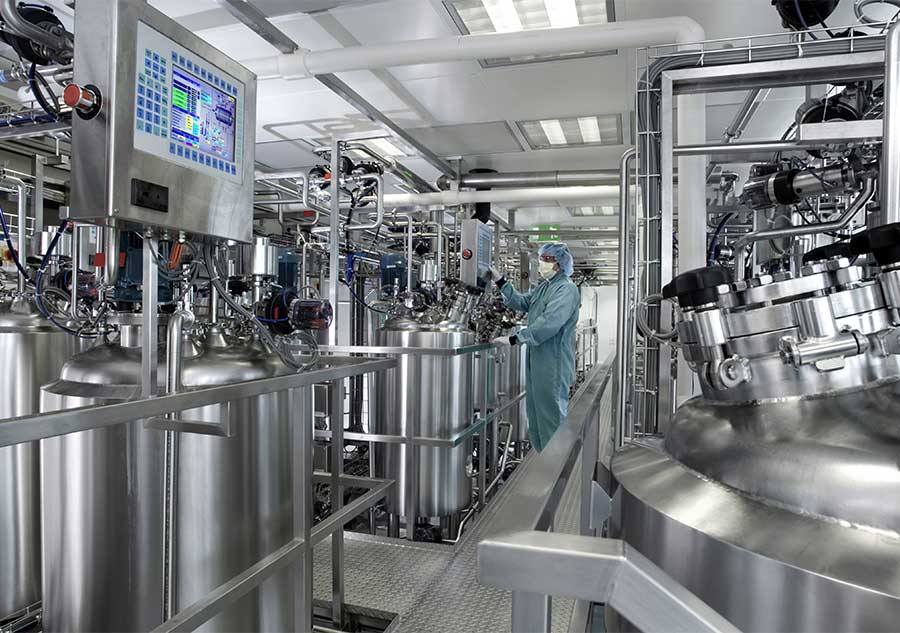
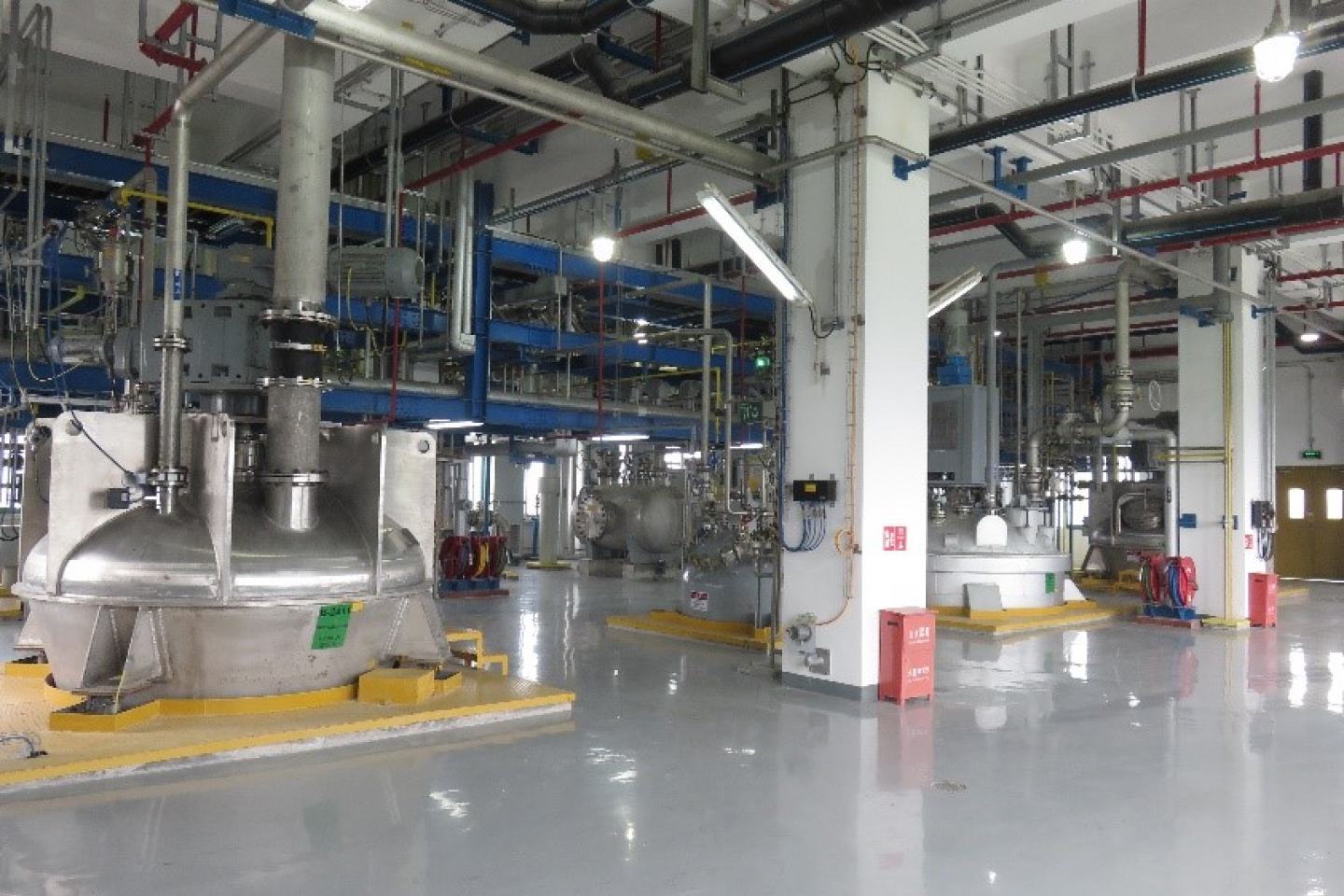
