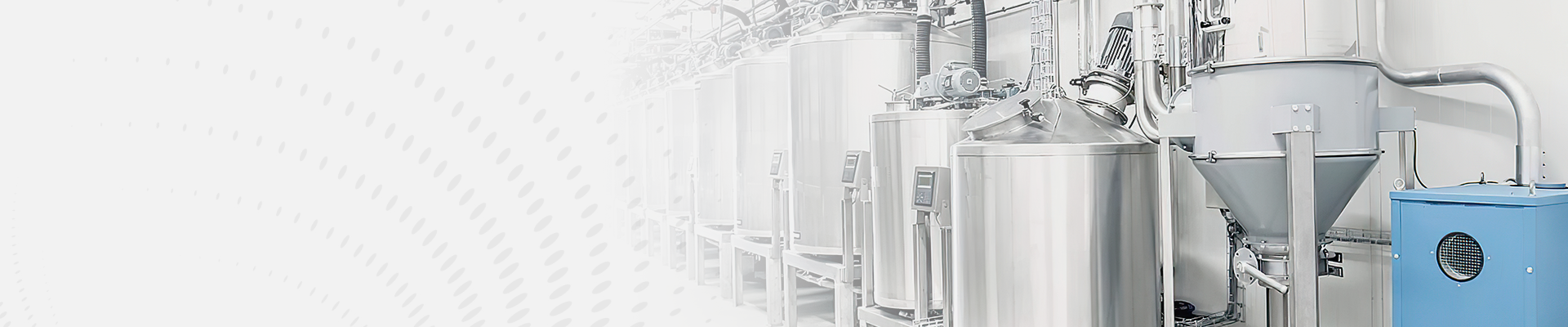
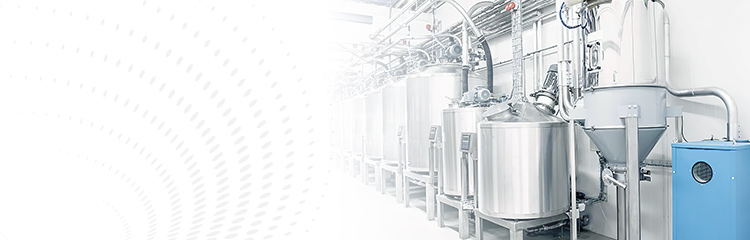
The main process equipment of the glue automatic batching system production line consists of reserve reaction tanks (including three reaction tanks for starch, lye and resin), reaction kettle (including three reaction tanks for borax, lye and resin and their common weighing devices), one main reaction tank and its weighing device and four finished product reaction tanks and their measuring devices.
This glue automatic batching system production line is equipped with alkali system (using carbon steel reaction tank body), stirring device, electronic weighbridge, lye reactor and pipeline are stainless steel. After the flake alkali is turned into liquid alkali, it is stored in the lye storage tank. The liquid level of the lye reactor can be automatically controlled by PCC, when it is lower than the set low limit, the lye pump will be automatically started to replenish from the lye storage tank.
The starch storage reaction tank is carbon steel reaction tank body, equipped with screw conveyor, vibrating feeder, and high and low material level sensors. The main reaction tank is equipped with steam heating device and automatic temperature control system, equipped with temperature detecting element, secondary temperature meter and steam cut-off valve, and adopts PCC to control the temperature.
Each glue point storage reaction tank is equipped with liquid level detection and stirring device. The weight of glue in each glue storage reaction tank can be displayed and monitored in real time on the touch screen in the glue making room.
Process Overview
First the reactor is charged from the storage tanks for borax, resin and lye: the three reactors are fixed on a frame supported by a weighing module and share a common weighing device. The resin and the lye are both liquids at room temperature, and their transit storage reactors are equipped with the highest and lowest floats. The first time only add resin, when its liquid level reaches the high float position to stop adding, at this time the reactor weighing instrument shows the weight is the weight of the resin, but also its maximum value. The second time also only add lye, when the liquid level reaches the high float position, stop charging, at this time the weight displayed on the meter minus the weight of the resin added for the first time, that is, the weight of the lye. Save this calculated value as the current weight of lye. Borax is a solid and is added to the borax reactor manually, but is measured in the same manner. In the savings reactor for starch, there are high and low level sensors and a vibrator, so that when the high level is reached, no more starch can be added to the storage reactor, and the low level signal prompts the addition of starch. The function of the vibrator is to vibrate the starch loosely, vibration, to prevent the starch bridging. When it is lower than the lowest material position, it will automatically start the vibrator to vibrate down the starch attached to the wall of the reaction tank.
Production of glue, in addition to the need to successively add a certain proportion of water and starch to the main reaction tank as the base material, the other main is to add borax, resin and lye. These three ingredients, are added separately, if the current lye, the weight of the reactor will become smaller, the difference is injected into the main reaction tank in the weight of the lye. The current lye weight in the reactor is the original weight minus the weight of the lye injected into the main reactor. Save this value as the current lye weight.
The other two materials are added to the main reaction tank in the same way.
Each cardboard production line actually requires only one type of glue, and different cardboard production lines have different formulas. At present, the glue plant is equipped with 4 finished reaction tanks (with steam heating device), each of which has a different formula of glue. These 4 reaction tanks are located next to different cardboard production lines and are connected to the main reaction tank through pipelines, and the heated glue is sucked from the main reaction tank to the corresponding finished reaction tank by an air pump.
The system is equipped with automatic formula correction function, when adding materials, you can monitor the deviation in the process of adding materials through the screen, and automatically correct the ratio of the latter according to the ratio of the formula, in order to ensure the accuracy of the formula; you can realize the data communication with the user's production management system, and through the parameter setting, it automatically determines the amount of glue according to the order to be produced, in order to reduce the waste of glue; after the initial input of the formula, when the user needs to adjust the formula, there is no need to calculate the change of materials. After the initial input of the formula, when the user needs to adjust the formula, there is no need to calculate the change of the material, just directly input the result of the change of the glue, the program can automatically modify the formula; with an automatic glue blowing function, when each reaction tank after the delivery of the glue automatically blowing and reset the system to avoid clogging of the hose.
Composition and configuration of control system
Weighing system composition
The batching system is composed of B&R2003 series PCC as the core, adopting touch screen as the human-machine interface, combined with PANTHER weighing instrument of METROPOLIS, temperature control instrument of the main reaction tank as well as water adding control and starch conveying control device. In addition, the system is equipped with a number of pumps, shut-off valves, liquid level and material level sensors.
Metering System Configuration
The PCC is equipped with a BP704 (4-slot backplane), the CPU of which is installed at the leftmost end of the backplane, and a double-width module CP476 with 24VDC power supply is selected, which is equipped with one RS232 and one CAN interface and a status indicator, and there are also four slots for screw-in modules, so that the screw-in modules can be inserted into the slots when expansion is required and fixed with fastening screws. The screw-in modules can be analog or digital modules or communication expansion modules.
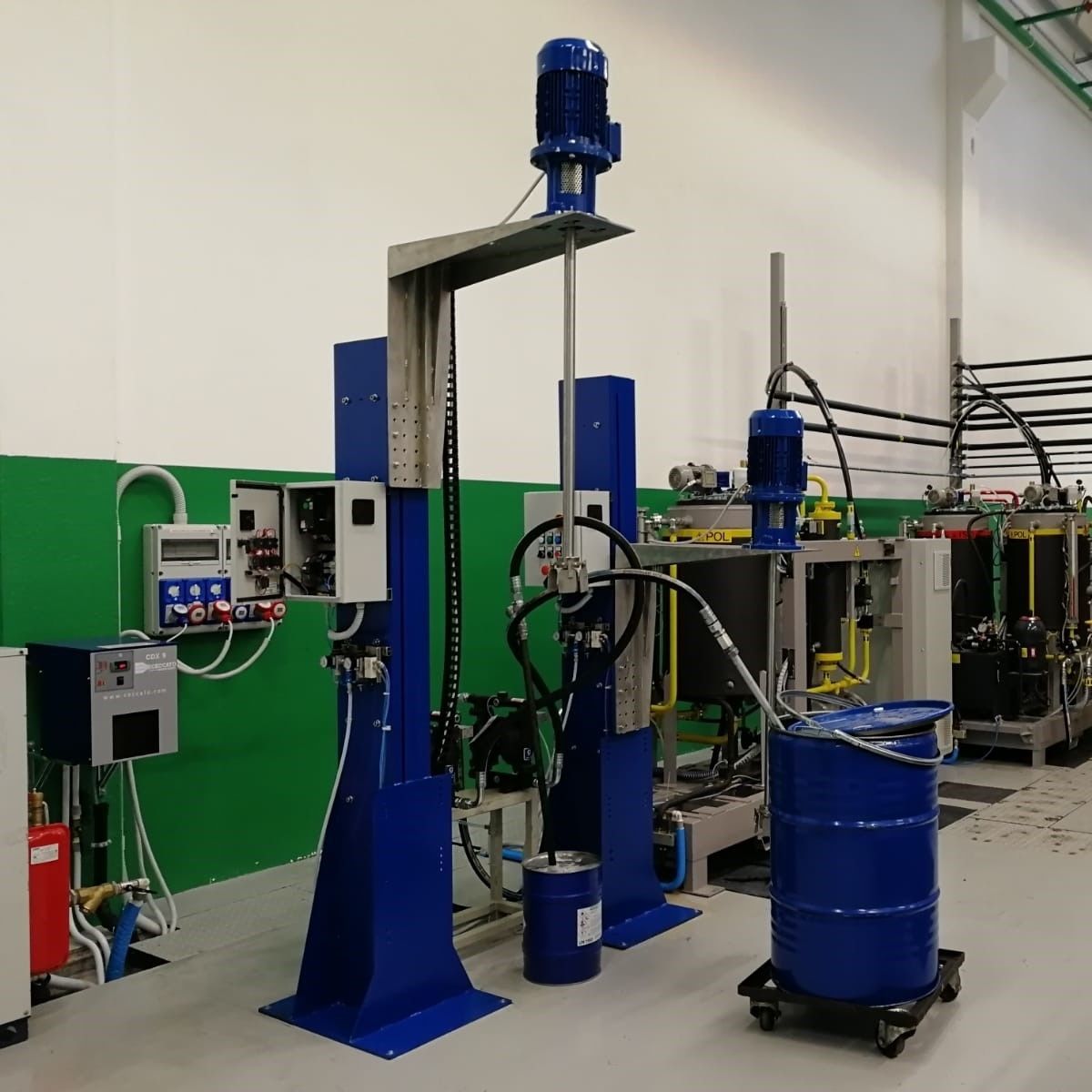
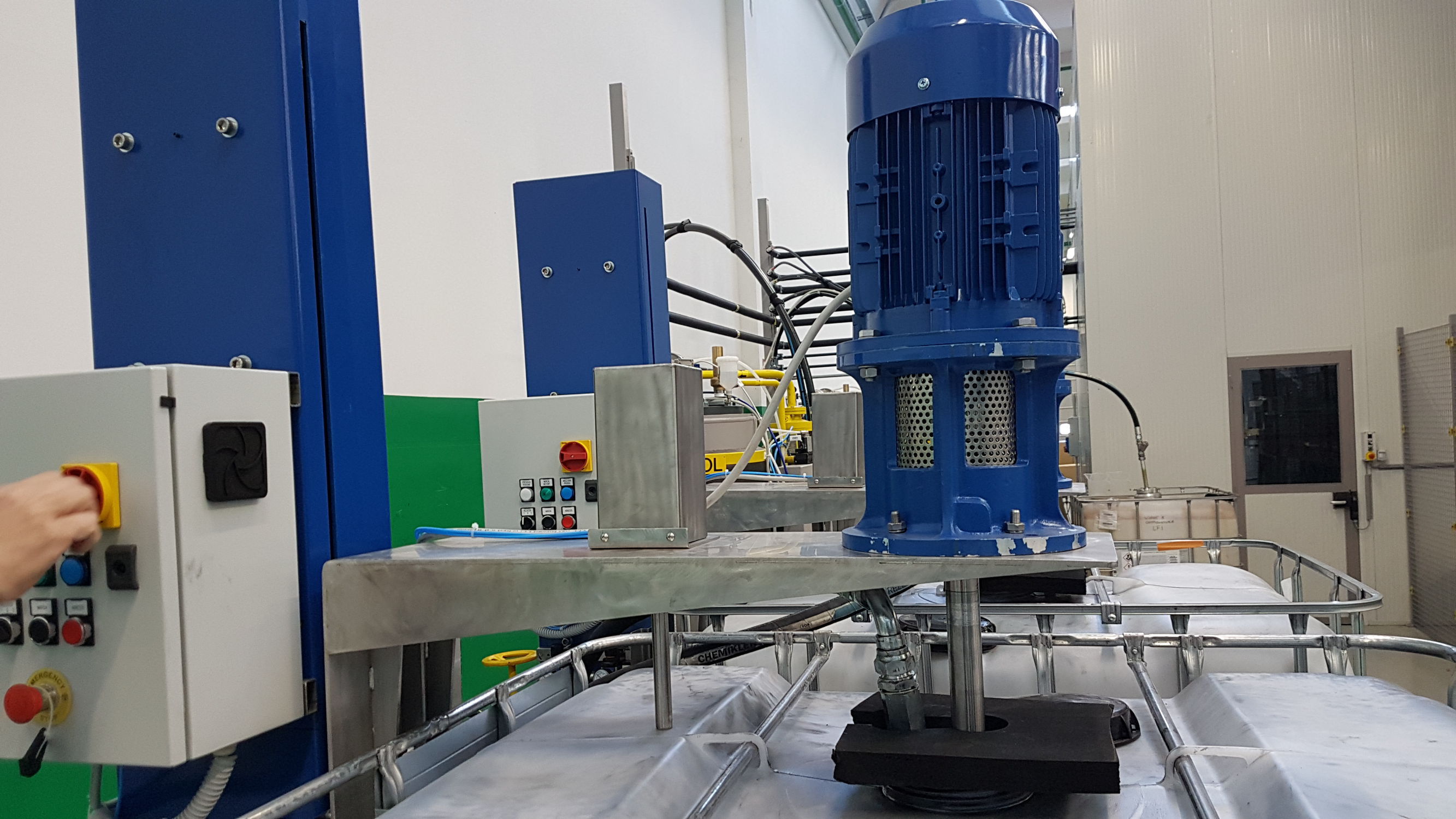
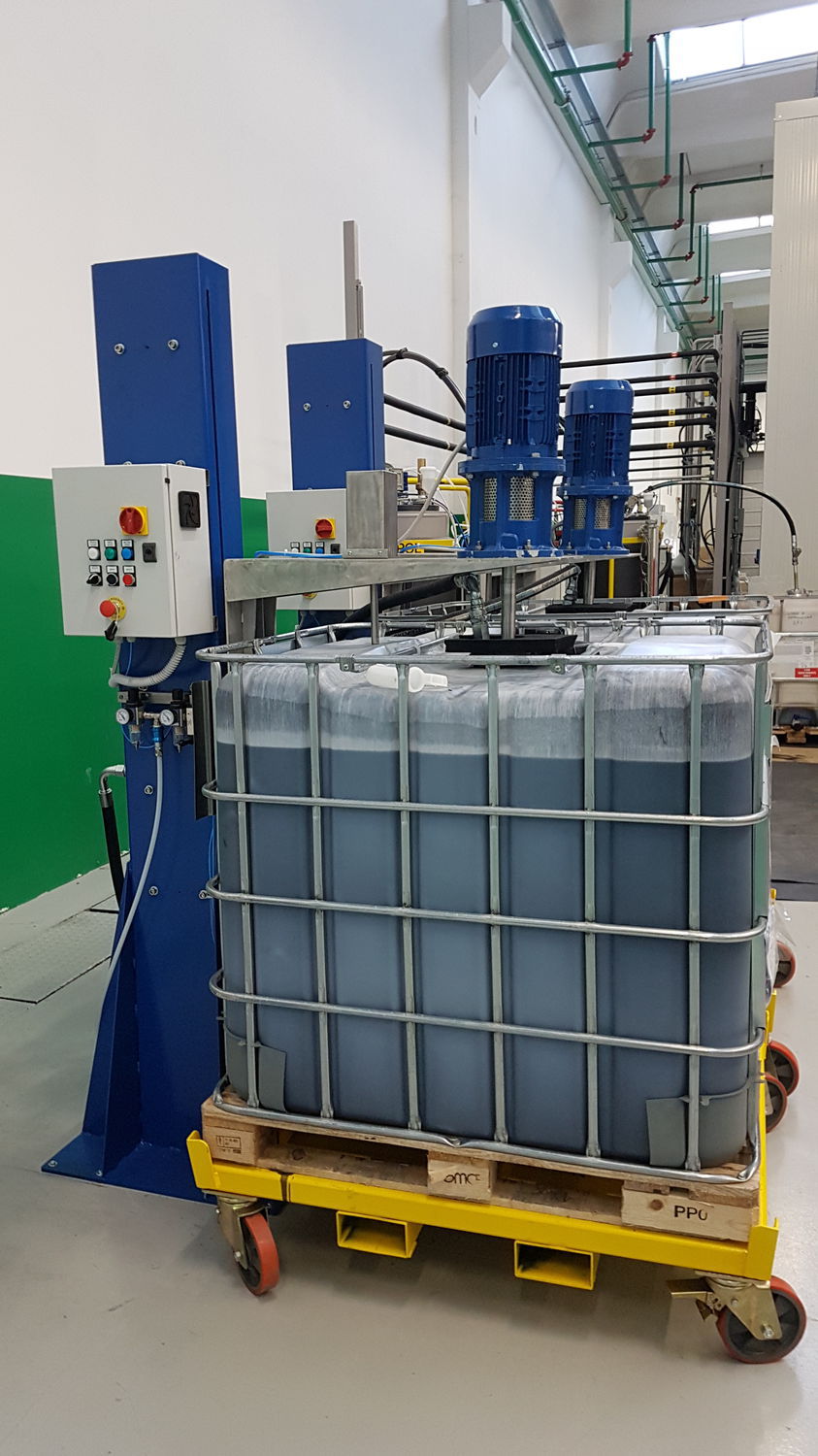
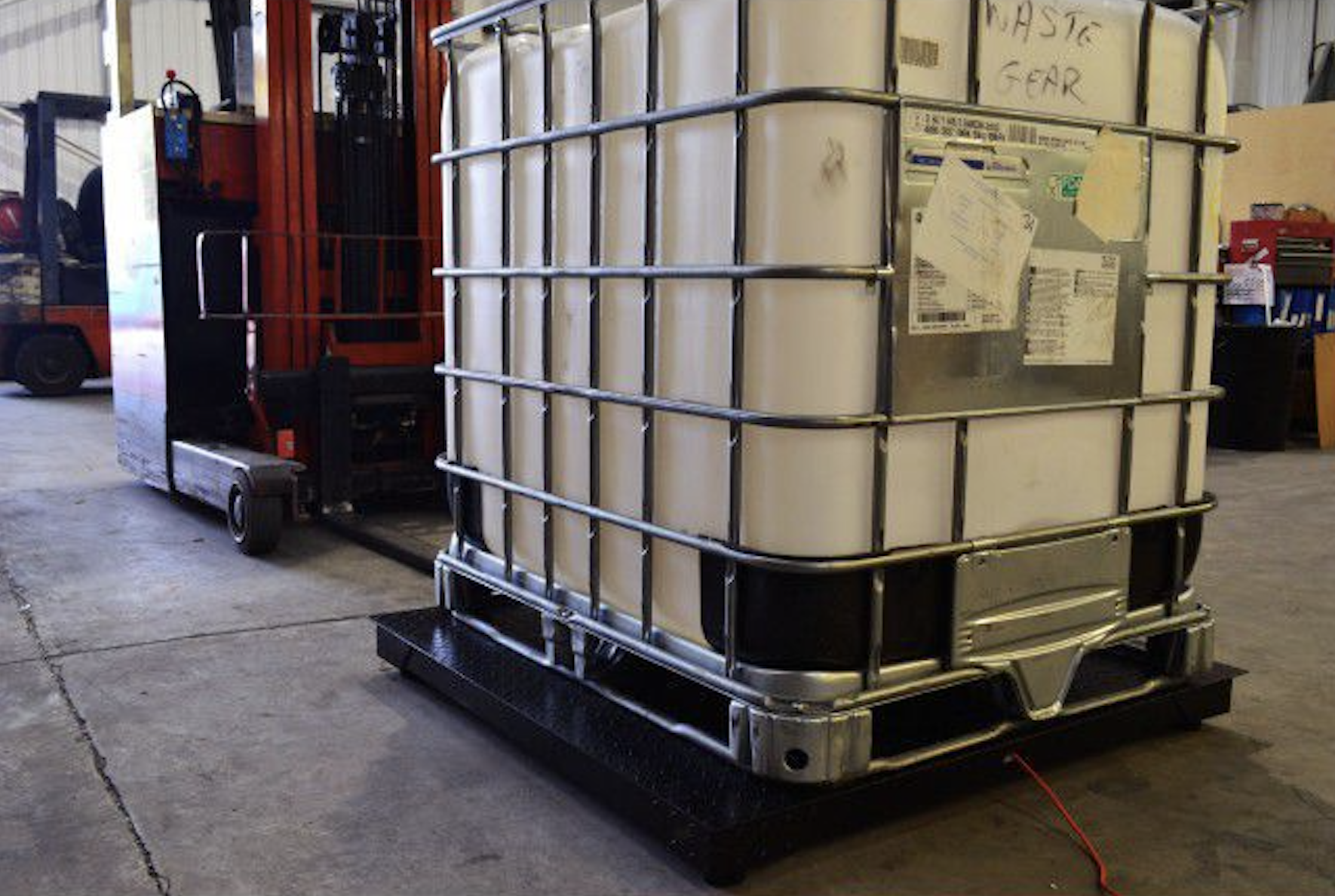

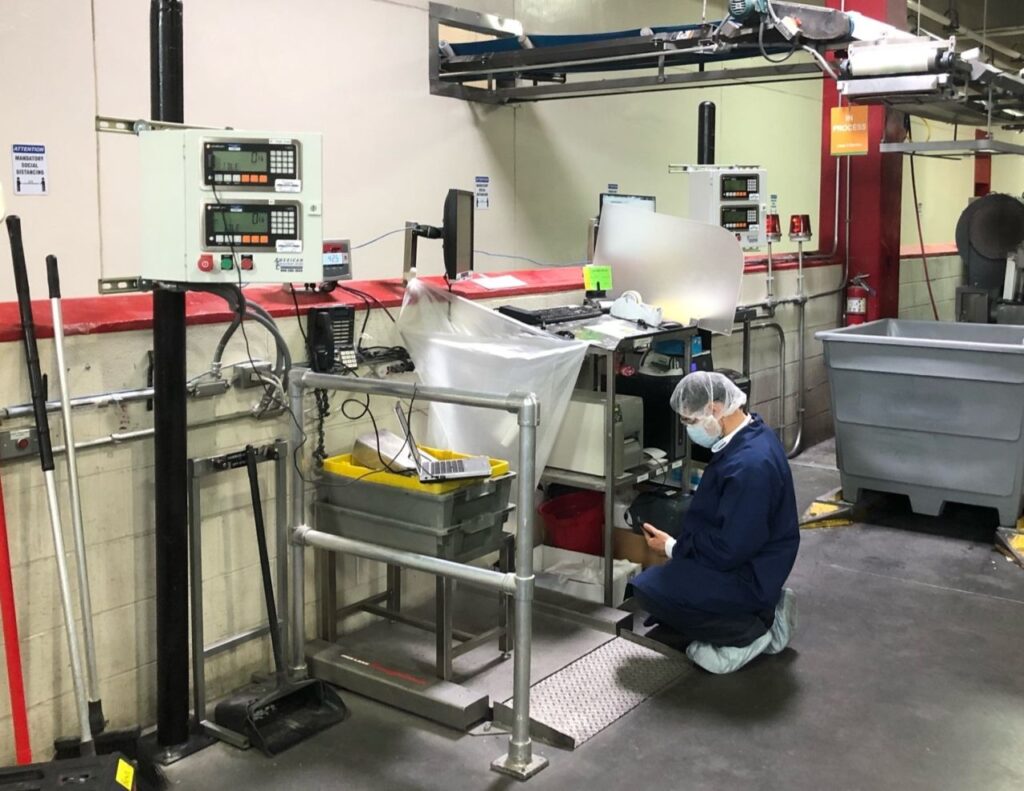