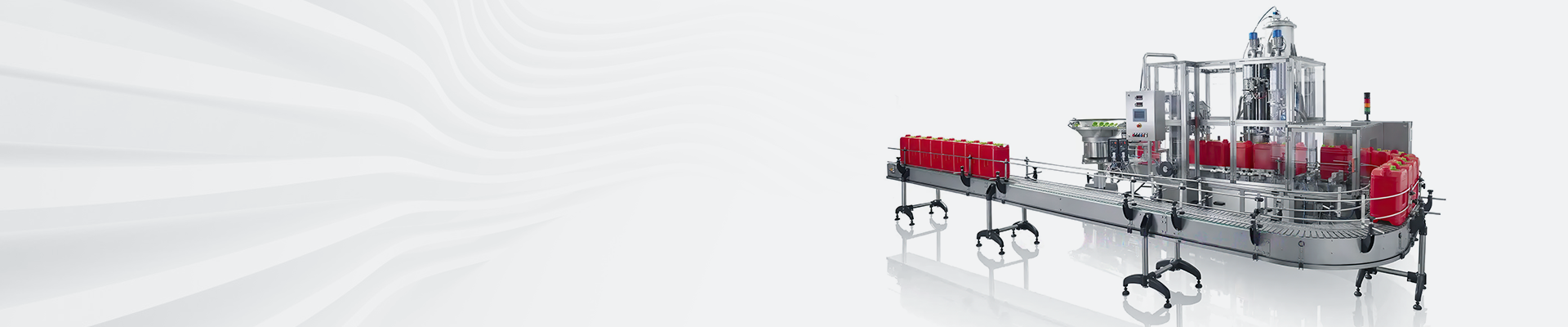
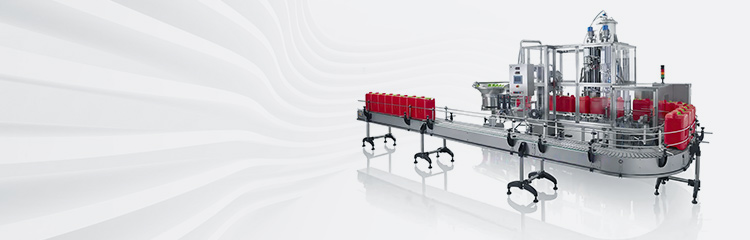

Summary:The DCS batching system automatically adjusts according to the originally set proportions so that the proportions of each material remain unchanged. It can control multiple belt conveyors at the same time. It has a mechanism for computers and weighing instruments to monitor each other and a variety of alarm mechanisms.
In the rubber industry, DCS system adapted to the batching site production environment is harsh, dusty, weighing requirements of high precision, weighing range, and some raw materials are harmful to the human body. Therefore, the study of high-precision batching methods, so that the staff as far as possible without contact with the material, is to improve the labor intensity and the environment of the urgent need. In the past, the dosage, generally using two-speed feeding, that is, fast feeding, slow feeding, weighing accuracy by pre-close the door to ensure the value. As the material specific gravity and viscosity are affected by the ambient temperature and humidity, it is easy to caking and sticking, which has a great influence on the weighing accuracy, and it is difficult to guarantee the weighing accuracy. The main technical parameters of the system:
Technical index of dosing scale
Model: CS25L/CS210L/CS230
Weighing range: 0.05~5kg/0.1~10kg/0.3~30kg
Accuracy grade: 0.5/0.5/0.5
Graduated value: 1g/2 Development of mechanical system
The feeder is the main body of this feeding system, which is mainly composed of automatic weighing device for small materials, collecting basket conveying line, silo, unpacking room, dust removal device and so on. The design of the feeding system is mainly to fulfill the functions required by the production process and is characterized by durability, easy operation, reliable operation, high production efficiency and low environmental pollution. For the material characteristics and process formula requirements in the mechanical equipment on the following several difficulties.
(1) Aggregate basket conveying line, the requirements of a simple structure, accurate and reliable positioning, easy to control.
(2) High weighing accuracy, good anti-interference.
(3) In order to ensure accurate weighing, the material must be able to flow well, developed with a variety of arch-breaking form of the silo;
(4) in order to reduce environmental pollution and material loss, specifically for the feeding system developed a single material dust recovery device.
2.1 High weighing accuracy and fast weighing speed
(1) small materials on the weighing accuracy requirements are very strict, some small materials allow error within 1g, in order to meet this demanding requirements, we in addition to selecting high precision, good performance curve of the measurement module, according to different materials, in a set of systems, the design of different forms of feeder, so that fast feeding to ensure the weighing speed, slow feeding to ensure the precision of the weighing, the material of the special high-precision use of the The material of special high precision adopts "drop type" feeding method. This is the same kind of equipment at home and abroad do not have, from the introduction of foreign production lines, the accuracy is far lower than our dosage system.
(2) The mixer adopts the weighing method of single scale for single material and total scale calibration, so that each material in the formula can be weighed individually at the same time, and 2g/5g can be used to select the weighing module with small range to improve the rate of differentiation, i.e., to improve the precision of weighing and to ensure the speed of weighing.
2.2 Simple structure, reliable operation and accurate positioning of the conveying line.
Developed multi-position pneumatic closed-loop conveying line, with a cylinder can easily drive the operation of the conveying line, is the company's first patented product, and the domestic chain conveying line, foreign roller conveying line, compared with the smooth and reliable operation of the structure is simple, no noise, almost no need for maintenance, the design, the technical level of the level is much higher than the level of the domestic and the introduction of products.
2.3 Various forms of arch-breaking to ensure weighing.
In order to solve the problem of arching of small materials in silo, opening of bridge, sticking wall, balling and other domestic and foreign long-term difficult to solve, the domestic production and the introduction of equipment often need to manually knock the silo, thus reducing the performance of the equipment. We according to the nature of different materials, based on a large number of experiments, respectively, the use of pulse arching, special vibration silo arching, spiral leaf spiked arching and other forms of broken, and obtained good results, with arching device silo has also become another patented product of our company.
2.4 Single material dust recovery
In the weighing, unloading, unpacking, because most of the material is powder, dust flying more, the dust will pollute the environment, two will cause material waste. In order to reduce environmental pollution and material loss, each material has its own dust removal device, that is, to ensure the recovery of materials, improve economic efficiency, but also no pollution of the environment, so the dust in the dust is easy to fly place are configured with a dust removal device. Recovered materials are returned to the silo for reuse.
3 control system development
3.1 The structure of batching control system adopts multi-station and multi-scale working mode at the same time, which requires high real-time performance of control system. According to the operation of each batching station with the same action, it adopts three-level computer control program, i.e. equipment control level, system control level and management level.
3.2 Equipment control level
According to the characteristics of the process, each station moves and operates in the same way. It is reasonable to carry out dosage control according to stations. The equipment control level mainly completes all the actions of single material batching, and adopts intelligent batching controller, which mainly completes the actions of automatic weighing, feeding, arch-breaking, unloading, etc. The weighing can be set according to the recipe requirements. It can set the weighing quantity and allowable error according to the formula requirements, and can automatically complete the above actions according to the system control instructions. At present, there is no similar product at home and abroad which can fulfill the function of automatic dosing of single material and meet the requirement of mixer control level instruction, so the company has researched and developed according to the requirement of automatic weighing system for small materials.
Feeder through the understanding of weighing materials and experiments, the main factors affecting the weighing of the main factors are as follows:
1 the viscosity of the material: in the same environment and the same feeding device, different materials feeding speed is different, thus causing debugging difficulties, weighing accuracy is difficult to control.
2 Specific gravity of the material: due to the specific gravity of the material is different using the same device, feeding speed is also different.
3 the influence of the environment: the environment of the temperature, humidity changes will lead to material viscosity, specific gravity and other physical characteristics of the change. Mainly the viscosity of the material with the increase in temperature and increase, resulting in easy arching of the material, caking, weighing is not favorable.
4 Due to the nonlinearity of the control feeding device and control device, even under the same control method and control amount, the vibration force and feeding speed of each feeding device are different. Due to the above factors, in the previous two-speed feeding, each material has to be adjusted to the corresponding state in order to achieve the expected weighing accuracy. However, with the change of ambient temperature or different material batch number, the original feeding state often can not guarantee the weighing accuracy, need to be readjusted, thus reducing the production efficiency. This shows that it is very complicated to ensure accurate and fast weighing. In the previous two-speed feeding, vibration force feeding fast, but the accuracy is difficult to control; vibration force is small feeding slow, the accuracy can be controlled, but the weighing time is long, low efficiency. Based on the above analysis, a feeding speed control scheme is proposed. This control method uses closed-loop control, feeding speed as a control parameter, to overcome the above factors on the weighing accuracy and production efficiency. Changes in the above factors are overcome by changing the vibration force. This control method, although it overcomes the influence of the above factors on weighing speed and accuracy, but the control algorithm and control means are more complicated. Based on the speed given, in the weighing of the initial period, stabilized at the speed V0 is a fixed value adjustment system. As the weighing value approaches the set value, the set value of the speed decreases, thus the system is a follower regulation system. The previous segmented control is changed to continuous stepless speed regulation control.
3.3 System control level
The control level is the control core of the small material weighing control system, which adopts PLC commonly used in industry as the computer of DCS system to control the operation of the whole system and ensure the reliability of the control system. Each batching control monitor receives the instruction from PLC to operate, and each action and signal control is carried out by PLC to control the action of weighing, unloading, arch-breaking, alarming, conveying and so on.
In the whole control system, it is divided into automatic working mode and manual working mode. Automatic working mode, that is, all the actions of the whole system are completed automatically, that is to say, by the computer control to complete, so that the system to achieve the highest production efficiency. The automatic part has automatic weighing, automatic unloading, automatic conveying of the aggregate basket and automatic calibration. The action is accurate and continuous, strictly according to the process requirements. The manual working mode is mainly used during system debugging or system maintenance. Each action is controlled by an operating button, and each action corresponds to a control button.
Automatic mode and manual mode of work to achieve non-disturbance switching, to ensure the operation of the system, in the event of system failure can be converted to manual mode of timely processing. After processing, it can guarantee to continue to run in automatic working mode, which improves the operability of the system.
Automatic start and automatic stop is the key issue of this system, reflecting the level of the control system and the production efficiency of the small material dosage unit. That is to say, when the system is designed in general each part is working in parallel to improve the working efficiency. However, in the driving stage and parking stage, it should be put into automatic work gradually according to the conditions of system operation. That is to say, there are two main parts of the small material batching machine, i.e. the automatic weighing and the aggregate basket conveying line, which are operated in the sequence of aggregate basket conveying, automatic weighing and calibration. And every time the aggregate basket conveying line advances, there is a station put into automatic weighing, and it must make every part enter the working state when it can reach the simultaneous work. When driving and stopping, it is necessary to increase the judgment and control of the working state of the system, and this system well realizes the automatic driving and stopping. As far as the general control system is concerned, manual control needs to wait until the operation is stabilized before putting it into automatic operation.
3.4 Management level
DCS management level adopts powerful personal computer, and control level, batching equipment level through the RS485 bus constitutes a small computer management network. It mainly accomplishes formula management (including formula input, formula modification, formula printing, formula copying, etc.), formula operation (including formula download, parameter download, formula operation), data report (including daily report, operation record, material statistics, etc.), parameter setting (including production quantity and related parameters), and includes functions such as monitoring of system operation status, data collection, completion of production quantity, alarm of fault indication, alarm of low material level of material warehouse, etc. It also includes monitoring of system operation status, data collection, completion of production, fault alarm, low material level alarm, etc. Considering the convenience of system debugging and maintenance, the on-site control part is divided into two working modes: manual control and automatic control. Manual mode of operation is each action is completed by manual operation; automatic mode of operation is in accordance with the process of the prescribed sequence of action, by the computer automatic control is completed. Through the management computer can completely reflect the operation of the whole system.
3.4.1 Main functions and structure of the system management of the main functions of the formula and raw materials management, real-time monitoring of production and a variety of data summary reports.
3.4.2 Recipe Management
This function of DCS includes the functions of recipe creation, modification and printing, etc. Since the recipe data is relatively simple and consistent, it is easy to be processed by database, so all the recipe data is deposited into a form, and the recipe data is distinguished according to the different names of the recipes, and the recipes are queried and modified by adopting the standard SQL statement, so the recipes are easy to be modified and maintained.
3.4.3 Data Report
Due to the large amount of data collected, all data are stored in the database for easy analysis and processing. Each record includes information such as production time, production formula, number of bags, material, actual value, and error. Reports of running records, alarm records, recipes, etc. are available.