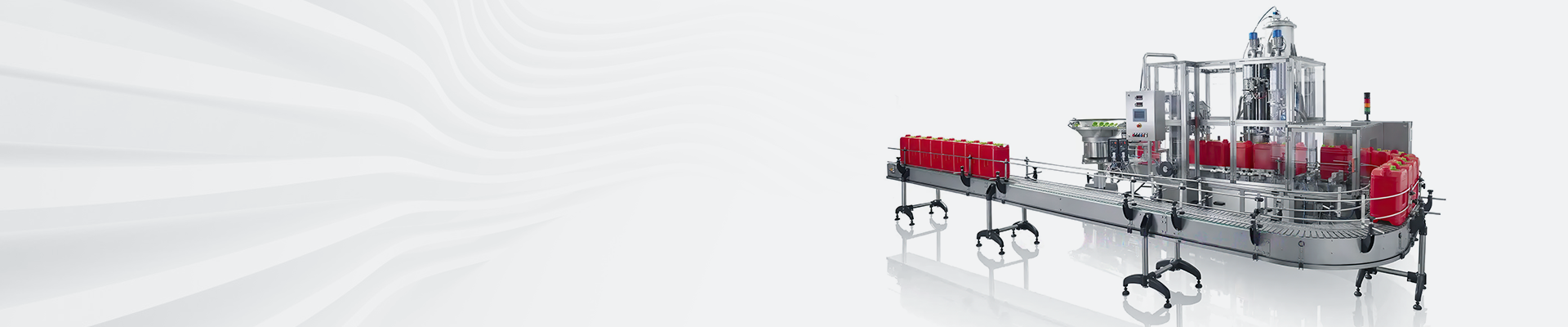
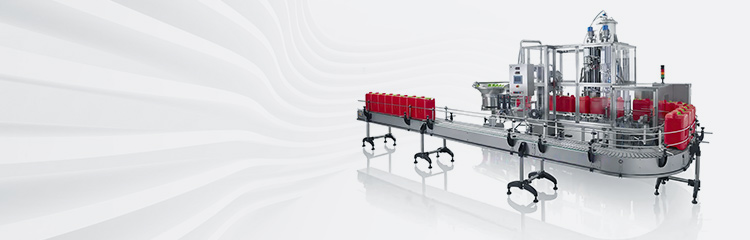

Summary:The filler is sent to the mixing barrel through the screw feeder and metering device, and the blanking amount is controlled by adjusting the rotating speed of the feeder. The water pipe is equipped with a flowmeter to measure the water quantity, and the water quantity is controlled by controlling the opening of the regulating valve. Water and cement are added into the mixing barrel according to a certain proportion to make cement slurry with a certain concentration.
With the development of the mining industry and changes in mining conditions, there are more and more mines using cemented filling in non-ferrous metal underground mining. The cemented filling mining method has the advantages of high recovery rate, low depletion loss, controlling ground pressure, protecting the ground surface, fireproofing and waterproofing. Filling is an important production link in this kind of mining, and the strength size of the filling body is an important index reflecting the effect of filling, and the main factor determining the strength of the filling body is the concentration of the cemented sands, so it is very important to ensure the stability of the concentration of the tailing sands cemented filling material. Once upon a time, the control of the filling process was mainly accomplished by manual operation. Manual control of the filling process, the labor intensity of workers, work boring, prone to work errors and large errors, difficult to real-time control of the concentration of filling material and gray sand ratio. Therefore, in order to ensure the quality of the filling material, the use of automatic control technology to prepare the filling material, improve the accuracy of the batching and process stability, reduce the labor intensity of workers is imperative.
1 Cemented filling process
Rod sand is transported to the horizontal sand silo plant by train and unloaded into the horizontal sand silo, which is transferred to the intermediate sand silo by the grab crane, and then unloaded to the belt conveyor by the disc feeder under the intermediate sand silo and screened to remove the large pieces; the belt conveyor sends the rod sand to the buffer sand silo, and then unloaded to the belt conveyor by the disc feeder under the buffer sand silo, and ultimately transported to the D2.5m mixing drum of the filling material. Bulk cement is transported to the cement silo by the cement transportation tanker, and then sent to the cement silo through the soot blowing pipe.
The cement is sent to the D2.0m cement mixing drum through the screw feeder at the bottom of the silo and the cement metering device, and then it is fully mixed with a certain proportion of water to make cement slurry. The mixed cement slurry flows to the D2.5m filling material mixing drum through the pipeline, mixes with the bar milling sand and process water, and then makes the cemented filling material which flows through the filling borehole to the underground quarry for filling operation.
2 Main measurement and control functions
2.1 Measurement and control of material level of buffer sand bin and cement bin
Continuous monitoring of the material accumulation height in the silo, reminding the operator to open the feeding system when the material level is low, and interlocking to stop the feeding belt conveyor when the material level is high.
2.2 Measurement and control of cement and water quantity in cement mixing drums
Cement is sent to the mixing drum through the screw feeder and metering device (weighing module), and the amount of material discharged is controlled by adjusting the rotating speed of the feeder. The water pipe is equipped with a flow meter to measure the water quantity, and the water quantity is controlled by controlling the opening of the regulating valve. Water and cement are added to the mixing drum according to a certain proportion to make a certain concentration of cement slurry.
2.3 Level measurement and control of cement mixing drum
The liquid level meter on the upper part of the mixing drum continuously detects the liquid level in the drum, and through controlling the opening degree of the discharge valve, the liquid level of the mixing drum is always maintained at a stable height, which not only can give play to the efficiency of the mixing drum, but also is conducive to the homogeneous mixing of the cement slurry in the drum, so that the feeding and discharging of the mixing drum is balanced, i.e., the quantity of the newly added cement and water are equal to the quantity of the discharged slurry and the cement slurry is always prepared steadily; it can also be calculated to make a certain concentration of cement slurry by adding the cement and water into the mixing drum. carried out; it is also possible to calculate the concentration of the cement slurry.
2.4 Measurement and control of bar milling sand and water quantity in the mixing drum of filling material
There is a measuring device (weighing module) installed on the belt conveyor at the bottom of the buffer bin, and the amount of material is controlled by adjusting the rotating speed of the disk feeder; the flow meter on the water pipe measures the amount of water, and the amount of water is adjusted by controlling the opening of the regulating valve. In this way, the bar milling sand and water are added to the mixing drum in a certain proportion. The ratio of bar mill sand to water depends on the amount of prepared cement paste to be added. In practice, the daily flow rate and consistency of the filling material and the ratio of rod milling sand to cement are determined in advance, so that the ratio of rod milling sand to water can be calculated.
2.5 Filling material mixing drum level measurement and control
There is a material level meter on the upper part of the mixing drum to continuously detect the material level, and by controlling the opening of the discharge valve, the material level of the mixing drum is always maintained at a stable height, which can not only give full play to the efficiency of the mixing drum, but also is conducive to the homogeneous mixing of the filling material in the drum, so that the feeding and discharging of the mixing drum is balanced, i.e., the amount of new bar milling sand, water and cement slurry added is equal to the amount of the discharged filling material. The amount of newly added cement slurry is certain so that the concentration of the filling material can be calculated.
2.6 Filling material concentration and flow rate measurement and control
According to the material level of the mixing drum, the concentration of the filling material can be known. The measured concentration value is compared with the concentration value calculated according to the proportion, and the proportion of bar milling sand and water is slightly adjusted to make the final concentration of the filling material more ideal, because the moisture content of the bar milling sand, grading, storage time, ambient temperature and so on may make the concentration of the filling material change. The flow rate is used as a real-time signal of whether the filling material is blocked or not, if the flow rate decreases, the staff should open the pipeline blowing device to clear the blockage.
3 Main instrument selection
Instrumentation selection should give full consideration to its reliability and practicality. Buffer sand silo, mixing drum and cement silo level selection of radar level meter; cement metering selection of rotor weigher; cement mixing drum and filling material mixing drum discharge valve selection of pneumatic slide valve; water flow control valve selection of pneumatic single-seat control valve; water and filling material flow measurement selection of electromagnetic flowmeter; filling material concentration detection selection of nucleon densitometer; bar milling sand metering using a quantitative feeder.
4 Control system structure and its function
Computerized batching control system includes UPS power supply (10kVA, 220V, 1h) and DC power supply (24V, 10A), monitor (ENS, OPS), printer. The control system continuously collects and processes various operating parameters under different working conditions in a timely manner, controls the operating status of the equipment, and has good interruption response. Through the monitor and the function keyboard, it provides the controller with all kinds of useful information under normal and abnormal working conditions of the process. Through the printer, it can complete the functions of printing and tabulation, switch jump and sequence record, accident memory, and CRT screen copy. Online performance calculation and economic analysis.
5 Technical features
The technical features of the filling control system are as follows:
(1) Rotor weighing and measuring cement quantity
Compared with the traditional punch plate flowmeter, the rotor weigher does not need physical calibration and has higher accuracy and reliability. The rotor weighing adopts the structure of balance, the zero point of the weighing machine will not change, and the rotor blade can still maintain balance when it is attached with a small amount of dust. The material inlet and outlet are in the same straight line with the bearing, so the impact of material will not affect the balance. The rotor blade adopts new non-rigid sealing material, no dead angle in the disk, to ensure that all the weighed powder is transported away, no measurement error, and effectively solve the flow of powder generated by the flow, wear and tear, to meet the process of powder materials continuous quantitative feeding requirements.
(2) Pneumatic slide valve regulates filling material
Slide valve shell and main parts are tight casting, solid construction, high strength, not easy to deform, the valve body has a beautiful appearance; conveying channel smooth and clean, smooth flow of materials, will not form a blockage; in addition, the valve plate adopts the blade type design, closed by the slanting surface of the force applied to the valve seat, sealing is good, and can be used as a switch or regulation; conveying high concentration and high abrasion of the material is highly reliable.
6 Conclusion
The success of the application of the automatic control system of cemented filling machine depends on two conditions: first, whether the control scheme formulated for the preparation process of filling material is feasible; The second is whether the selected measurement and control instruments and equipment are applicable, stable and reliable. Some mine filling control systems in China are not working normally, and most of them are not perfect in these two aspects. Therefore, the practice and research in this area should be strengthened.