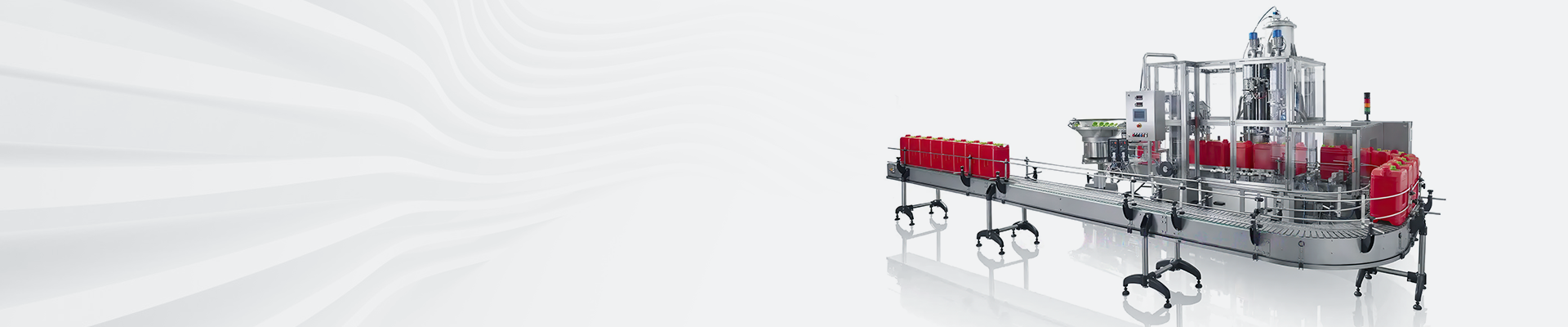
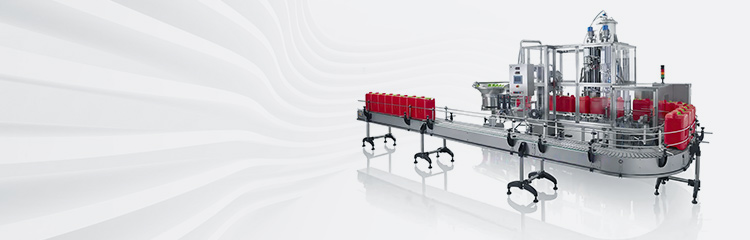

Summary:The liquid filling machine can control multiple filling machines at the same time, thus greatly reducing the cost of filling machines. It has the mechanism of mutual monitoring between computer and weighing instrument and various alarm mechanisms. Even in the case of computer crash, the filling system will not only send out alarm signals, but also continue to operate according to the original state.
1 Introduction
Packaging can be divided into two categories according to its nature: sales packaging and transportation packaging. Sales packaging can be divided into two categories according to the physical characteristics of the package: liquid (including low viscosity liquid, medium viscosity liquid and high viscosity liquid) and solid (including powder and granule). Due to the particularity of liquid (such as solubility, absorbability, convenience of production and transportation, etc.), the packaging machines for filling liquid account for a large proportion in packaging machinery. Research and production of novel special liquid packaging machine is still the development direction of packaging machinery industry in the future. It can be said that the filling machine is different because of the filling materials, technology, environment, production methods, supporting requirements and user needs. At present, the equipment manufactured by each manufacturer has its own emphasis, and the types of filling machines produced are varied and ever-changing, but none of them are exactly the same. Intelligent pneumatic liquid filling machine is a high-tech new product with intelligent mechanical and electrical integration, which is designed and developed by itself according to the needs of users, market information and the needs of chemical, food, pesticide, medicine and other industries, and puts forward new production requirements for filling equipment to be fully enclosed and matched with automatic liquid flow line, in order to simplify product structure, reduce equipment cost and expand adaptability to bottles of various shapes. It can not only intelligently and automatically manage the whole filling process of the filling production line, but also simplify the operation and facilitate users; It can also effectively prompt all kinds of mechanical, electrical and gas faults in the filling process, and shorten the time of fault identification and machine repair. It can effectively improve the production efficiency and utilization rate of the equipment.
2 Comparison of physical characteristics and quantitative methods of filling materials
Selective viscosity is the internal frictional resistance produced by fluid in flow, and its size is determined by the type, temperature, concentration and other factors. In general, liquids with low boiling point, low steam pressure and strong solubility generate low-viscosity solutions (such as acetaldehyde and ethanol). The filling material of automatic filling machine flows and measures in the filling, and the existence of internal friction resistance has certain influence on the performance, measurement, material, use and life of the designed filling machine. In order to better design, reasonably select and determine the structure and working principle of filling viscosity suitable for filling machine, it is necessary to scientifically classify viscosity. Due to the difference of physical properties and viscosity, there are great differences in the fluidity, internal friction resistance, power consumption, adhesion when metering, adhesion when discharging liquid and surface tension of liquid surface, so it is necessary to pay attention to the above differences in design. Generally, in order to ensure the filling accuracy and quality, one model can only be suitable for one type of liquid.
3 structure characteristics and working principle of filling machine
This filling machine is a production equipment that mainly fills low-viscosity liquid and uses the method of controlling liquid level to fill liquid materials into rigid (such as glass bottles) or semi-rigid (such as plastic bottles) containers. The filling machine mainly consists of frame, weighing and conveying platform, positioning mechanism, filling system, linkage compactor, liquid storage tank and control box.
Main working procedures and working principles: the conveyor belt on the feeding table conveys empty bottles at a speed of 1.2m/s, and when the first empty bottle is about to reach the predetermined position, the front bottle stopper in the positioning mechanism 4 pops up under the control of the front photoelectric head to block the empty bottles, so that the first empty bottles in each batch are in the accurate designated position; Set the batch number of the back photoelectric camera (the maximum number of this machine is 8); The rear bottle stopper is used as the isolation lever between batches, which ensures that the number of empty bottles to be filled in each batch (between the front bottle stopper and the rear bottle stopper) is the set batch number. When the rear bottle stopper extends in, the conveyor belt stops conveying to avoid the friction between the static bottle bottom and the moving conveyor belt surface during filling, to prevent unnecessary wear of the bottle bottom, and to ensure the stability of the filling bottle, which is beneficial to filling. After the conveyor belt stops, the liquid filling system inserts eight liquid outlets into eight empty bottles at the same time, and presses and seals with eight bottle mouths at the same time by virtue of the pressure and flexibility of the spring. The flexibility of the spring can effectively make up the error caused by the free height of eight bottle mouths, and improve the sealing adaptability of the filling machine to various filling bottles. At this time, the diaphragm pump starts to fill the eight empty bottles at the same time. With the continuous increase of the liquid level, the air in the bottles is discharged through the liquid return pipe. When the set control liquid level (filling quantity) is reached, the liquid return pipe starts to contact with the liquid level and start to return the liquid. Return the liquid higher than the liquid return nozzle to the liquid storage tank to ensure that the liquid level in the empty bottles is always the set value. When all eight empty bottles in the batch are filled and reach the set control liquid level height, the diaphragm pump will automatically stop running, the filling system will stop filling the empty bottles, adjust the pedestal to rise, and at the same time, eight liquid outlet nozzles will be lifted, so that the liquid outlet nozzles are completely out of contact with a batch of (8) filled bottles, and the conveyor belt will start to transfer the eight (1) bottles filled with liquid. The main working principle of the filling machine is to control the filling amount by controlling the liquid level in the bottle. The quantitative method of controlling liquid level is not only simple but also reliable, and is widely used in filling equipment. Controlling the liquid level position of the liquid level quantitative method is mainly realized by controlling the height of the liquid return port of the liquid return pipe. The height of the liquid return port of the liquid return pipe can be adjusted after calculation and determination according to the filling quantity, so as to meet the needs of filling bottles of various sizes.
This filling machine mainly has the following seven features:
1) adopting microcomputer control and mechanical and electrical integration technology, the equipment is intelligent, highly automated and has a large technical reserve space;
2) The quantitative method of liquid level control is adopted, so that the equipment has the advantages of simple structure, few faults, low production cost and fast operation speed;
3) The quantitative method of liquid level control is adopted, which makes the equipment easy to convert the information of liquid level height into digital information, increases the ratio of bottle capacity adjustment range, and can be adjusted steplessly, especially suitable for rapid filling of large-capacity containers.
4) Monorail linear conveying mode is adopted, which avoids the limitation of continuous motion mechanisms such as spiral conveying of bottles and positioning of bottle shifting star wheel on the shape of bottles, so that the machine has wide adaptability without changing any parts when changing the specifications and shapes of bottles;
5) By adopting microcomputer control and electromechanical integration technology, the equipment has the advantages of less and faster process parameter setting and simple operation;
6) By adopting microcomputer control and mechanical and electrical integration technology, the equipment has mechanical, electrical and gas fault display, thus shortening the time of equipment fault identification and machine maintenance and improving the production efficiency and utilization rate of the equipment;
7) Due to the above functional features, this machine can be used not only as a single machine, but also as a convenient match with other equipment for industrial automatic filling production line.
5 Design of main system of filling machine
The design of liquid level quantitative filling mechanism (filling head), the key part of filling machine, is the key to ensure that the filling machine can not only adapt to filling various containers (sizes and shapes), but also make the filling machine simple in structure, reliable in sealing and convenient to adjust.
The structure and working principle of the filling head: the filling liquid enters from the liquid inlet of the liquid inlet connector, flows through the liquid inlet conduit and enters the bottle through the liquid outlet nozzle; When the liquid level in the bottle reaches the plane of the liquid return pipe, the excess liquid will return to the liquid storage tank from the liquid return plane of the liquid return pipe, so as to ensure that the height of the liquid in the bottle is always the set value (filling amount). The gasket can not only ensure the sealing function of the bottle mouth; But also the liquid level height can be controlled by changing its quantity or thickness. The function of spring elastic compression is mainly to seal and make up the height error of each filling container, so as to ensure the reliability of work. In order to avoid the rebound of the inlet pressure and the influence of the wave on the liquid return plane, besides changing the orientation of the liquid inlet of the liquid outlet nozzle from vertical downward to uniform distribution of the liquid level circumference, and keeping a sufficient distance between the liquid inlet and the liquid return plane, the adjustment of the distance is realized by driving the liquid inlet joint by the filling system, and the periodic lifting of the filling system is realized by controlling the air cylinder by the computer.
6 design of distribution tank
The liquid of multi-head filling machine must be distributed through the pressure-stabilizing distribution tank before it can reach each outlet. Whether the pressure-stabilizing tank can distribute the liquid to each outlet at the same pressure is one of the keys to ensure the accuracy of filling machine. Only when the liquid level of the distribution tank is constant can the filling be stable and accurate. In order to achieve this effect, the feed pipe of the distribution tank adopts plug-in structure. In order to prevent the liquid level from being unstable due to the impact of the incoming liquid column, a buffer is set at the end of the plug-in pipe, which makes the liquid flow out from the small holes around the cylinder, and does not directly flush; The overflow downcomer is not directly connected in the direction perpendicular to the axis of the distribution tank, but a long and narrow opening is made on the side of the distribution tank, and an overflow liquid receiving tank is welded outside. The overflow downcomer is connected to the bottom of the overflow liquid receiving tank, so that the overflow shape is similar to a waterfall. The liquid level in the distribution tank is always kept almost flat during filling or intermittent filling, so that the hydrostatic head of the filling nozzle remains unchanged to obtain accurate filling quantity. When selecting the feed pump, the inlet of the distribution tank should be ensured. The discharge pipe of the distribution tank adopts an insertion structure to prevent the precipitated impurities in the tank from entering the discharge port. Because of this structure, the filling amount is quite stable in actual use and good use effect is obtained.
7 concluding remarks
Quantitative filling is an indispensable link in the production process. By adjusting different filling volumes through the regulating valve, one device can fill packaging cylinders with different capacities at the same time, which is particularly flexible to use. In addition, according to the size of output and the situation of operators, the number of filling nozzles is adopted, which is relatively flexible, and the volume can be adjusted according to different filling times and the materials of main parts can be accurately changed by measurement, which can be suitable for filling products with different properties.