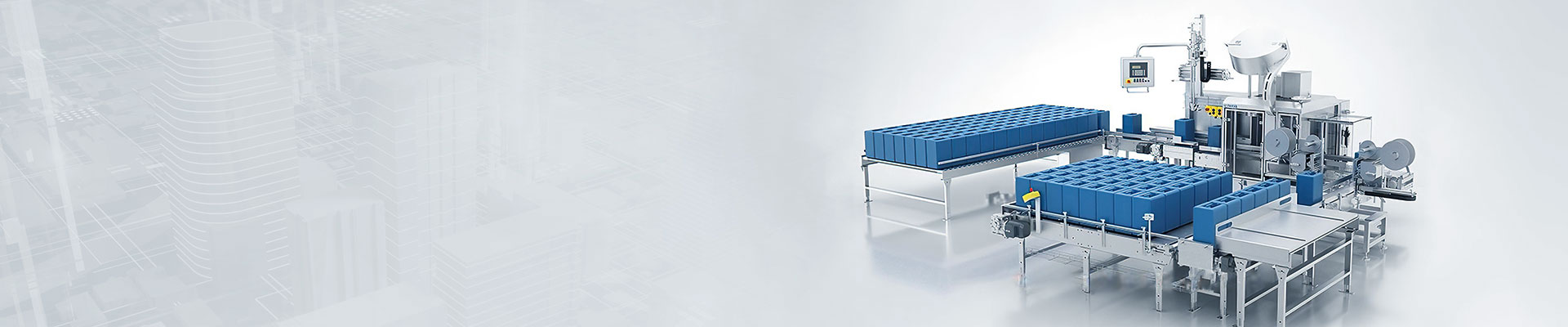
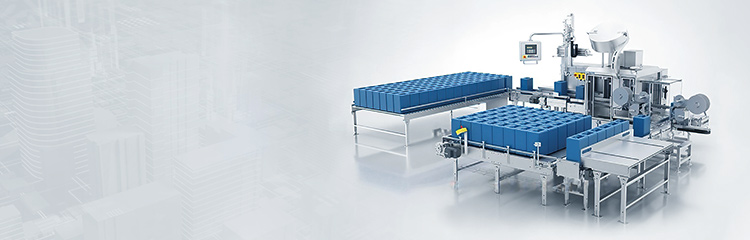
The ink filling machine uses the weighing module to connect with the data line of the weighing instrument, and controls the instrument to stop the pump and close the pneumatic valve when the preset quantitative weight is reached. Controlled by a PLC programmable device, the electric drum of the scale body runs simultaneously when the container is sent in, the photoelectric switch on the weighing module detects the signal sent by the passing container, controls the signal sent by the motor when the container reaches the filling position, and the electric rolling is stopped by the PLC and the skin is automatically peeled, the filling valve is driven by the stepping motor to reach the lower limit, and the well is sent by the travel switch. PLC control filling valve is fully opened for filling.

The automatic Filling machine utilizes the weighing module to connect with the weighing instrument with data line, and control the instrument to control the stopping of the pump and the closing of the pneumatic valve when the preset quantitative weight is reached. Controlled by PLC programmable, the container is fed into the scale body motorized drum running at the same time, the weighing module on the photoelectric switch detected by the container through the signal issued by the control motor to stop the container to reach the filling position signal issued by the PLC control of the motorized roller simple stop and automatic tare, filling valve driven by stepping motor to drop to reach the lower limit, well by the travel switch to send out a signal, the PLC control filling valve is fully open! Filling.
The automatic filling machine adopts LAN to realize the communication between the field computer and the filling equipment; it adopts the modular method to use VC++ to compile. Through the RS485 network can communicate with the control host. The use of multiple modules can easily form a RS485 distributed control system network. Each network can be connected to a maximum of 255 modules, the network can be connected to the control computer through the RS232/RS485 conversion.
Liquid filling machine adopts high-brightness low-angle LED array ring light source illumination, which can obtain high-contrast images and facilitate image segmentation processing. It consists of industrial camera, monochrome image acquisition card, high brightness low angle LED array ring light source, industrial control computer, driver, coordinate workbench LabVIEW and IMAQVision development platform. The CCD of the industrial camera takes the image of the inspected barrel on the scale of the weighing module in real time, and transmits it to the image acquisition card for storage in the memory of the computer through the PCI bus.
Basic parameters
Maximum weighing capacity: 30kg
Minimum Sensitivity: 5g
Filling range: 1-30kg
Filling error: ±10-30g (depending on flow rate and pulse force)
Power supply: AC220/50Hz Gas source: 0.5Mpa
Head material: SUS304 stainless steel (optional SUS316)
Applicable container: ≤Ф350xh450mm