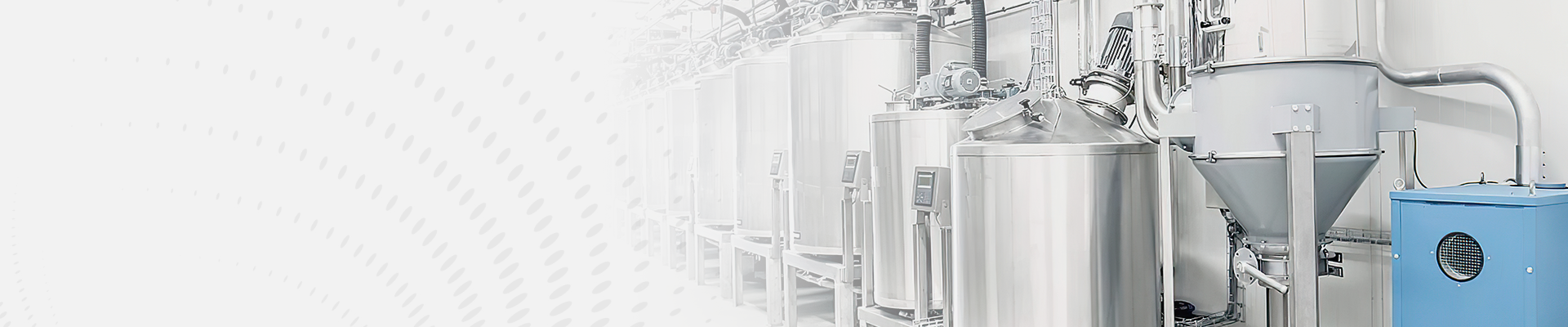
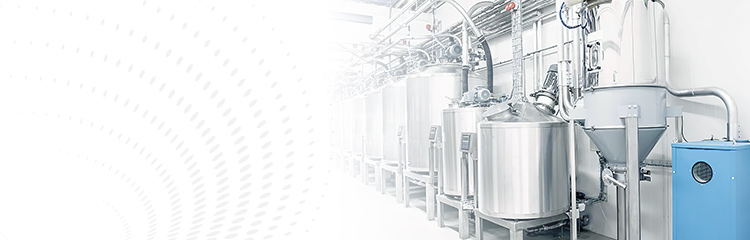
The liquid filling machine is mainly composed of seven parts, such as barrel separator, buffer roller table, flow controller of barrel selector, weighing system, capping machine and electrical control system. The electrical part consists of PLC, weighing instrument, man-machine interface and frequency converter. According to the user's personalized settings, the process of barrel feeding, barrel separation, barrel positioning, weighing and filling barrel conveying and capping can be fully controlled, and fast and high-precision multi-station filling can be realized (for convenience of description, 12-head filling machines are taken as an example). The automatic filling machine adopts 12 high-precision weighing instruments to synchronously control the filling process of 12 stations. The weighing instrument can conveniently set parameters such as target filling weight, large investment advance, investment advance and tare weight comparison value. The dynamic response speed is fast, the influence of environmental vibration can be automatically removed, and the requirement of filling accuracy can be fully guaranteed. Weighing and filling machine has humanized man-machine interface, and the design of man-machine interface is based on man-made operation habits. All modes have humanized operation interfaces, which provide convenience and also have various protection functions. Users can set personalized working parameters according to actual needs, and they can directly enter the working state after setting. The operation is simple and convenient, and there is no need to wait for complicated operations such as restarting.
The field management and control system of automatic filling machine based on single chip microcomputer, radio frequency card and network integration technology can control the filling of materials in real time and effectively. Realize the real-time detection of filling weight and the real-time opening and closing of solenoid valve in filling process, and upload data for effective microcomputer management. It mainly includes 89C52 single chip microcomputer control part, radio frequency card reader part, keyboard, display control circuit part, GM8125 serial port expansion circuit part, LED display circuit part, solenoid valve execution circuit part and upper PC database processing part. The RF card reader reads the electronic tag of the barrel from the site and uploads the tag code to the upper PC for identity determination. If the identity is legal, it will continue to open and close the electromagnetic valve and fill. During the filling process, the effective weight data on site will be uploaded to the upper computer in real time, which will be classified and summarized together with the electronic tag code. The upper computer will communicate with the server and send the data of each filling station.
The automatic filling machine monitors all kinds of filling equipment in the whole production line. On the control CRT, the running status of all production equipment related to the weighing system can be directly observed. In the picture, the animation indication function is set for the moving equipment such as motors, which realizes the drawing of historical curves, and can dynamically add/delete curves, stepless scaling of curve charts, dynamic comparison of curves, printing of curves, etc. Process parameters such as temperature, pressure and flow rate shall be recorded. In the PLC program of the lower computer, the fault alarm can be seen in the operation interface that the total fault alarm turns red and flashes continuously, and the buzzer in the hardware circuit generates alarm bell. When an alarm is generated, it will automatically switch to the fault analysis interface and directly see the alarm reason.
The automatic filling machine collects the weight of barrel identity data for the upper computer database to identify barrel identity and rules. Based on the inductance coil of EPC passive chip, it receives the R signal from the reader through the external LC loop, and provides power for the chip after being processed by the power circuit inside the chip. Through the damping load inside the chip, the data in the on-chip EEPROM is read into the reader, and the RF field is interrupted in a special way, so that the reader can write the data into the on-chip EEPROM. Reader data uploader server. An electronic tag is attached to the appropriate part of the bucket. When the bucket is put on the weighing platform, the RF card reader is aligned with the electronic tag, and the card reader is started to read the ID code of the electronic tag, and then the bottle ID number is taken out from the card reader and uploaded to the single chip microcomputer, which then uploads the data to the upper PC to enter the gas cylinder information database. The ID number is queried and compared in the database, and a code is returned to the single chip microcomputer. On the one hand, the single chip microcomputer returns a signal to the card reader to close the card reader, on the other hand, the single chip microcomputer carries out the related control operation of gas filling according to the program setting.
Main technical parameters of multi-station weighing filling machine:
(1) specification of packaging barrel: 4Kg or 6Kg.
(2) Filling station: 12
(3) Power supply: 50/60HZ 380VAC+10%
(4) Filling No.0.5.
(5 packs (maximum): 4Kg:1800 barrels per hour 6K-1600 barrels per hour.
Composition and function introduction of weighing system
Bucket separator and bucket fixer
The filling barrel of the filling system is conveyed by the conveyor chain plate. When the packaging barrels with the same specifications enter the production line, first, the barrels that are firmly attached to the car will be separated according to a certain spacing, forming a packaging barrel sequence with a certain spacing. The realization method is as follows: the front barrel is separated from the subsequent barrel by the front and rear baffles, and the two baffles are alternately switched on and off according to a certain period, and the spacing of the barrels is pulled apart by the movement of the roller table to form an equidistant filling barrel sequence (12 barrels in each group).
The barrel fixer fixes a group of barrels that have left in a specific position and then waits. The photoelectric switch is used to detect the position of the bucket, and the PLC calculates the time when the bucket reaches the predetermined position, and extends the cylinder of the fixed bucket to position the bucket. Once the last filling barrel enters the filling position, the barrel feeding roller table is in an idle state. At this time, the barrel pushing beam directly pushes a group of packaging barrels onto the barrel feeding roller table to prepare for the next filling step.
Roller carriage
N pallets are installed at equal intervals on the annular chain conveyor belt to drive the filling bucket forward. The distance between the supporting plates is equal to the distance between the two spray guns, so that 12 filling barrels are made corresponding to the 12 spray guns. The motor driving the pallet is controlled by frequency converter, which is convenient for adjusting the running speed and positioning of the pallet of the roller table. A photoelectric switch is fixedly installed on the side of the pallet of the roller table, and the running period of the roller table is controlled by measuring the number of pallets. Proper adjustment of the position of photoelectric switch can ensure that the barrel mouth corresponds to the spray gun.
Multi-barrel filling
The 12 filling barrels on the barrel feeding roller table are driven by the roller table drag plate and sent under the 12 filling heads. 12 barrels are placed on 12 scales, and the barrel mouth locator locates the barrel mouth. After the spray gun descends into the barrel mouth, the barrel mouth locator returns to its position, and the weighing system performs peeling operation. According to the set filling weight value, the weighing instrument and PLO control the fast feeding and slow feeding. After feeding, the spray gun is lifted to the barrel mouth, and the roller table drag plate drives the filled barrel to the next process.
Liquid storage tank control
Because of the high production efficiency of multi-station filling line, two liquid storage tanks are designed at the upper part of the filling system, and the two tanks are connected by pipelines. The lower part of the liquid storage tank is connected with the filling head through a flexible pipeline, and the upper part of the tank body is a feeding pipeline, on which a pneumatic cut-off valve is installed to control the feeding speed. A liquid level switch is installed in the tank. When the liquid level is lower than the low material level, the material pump is started to continuously send the materials to the liquid storage tank. When the liquid level reaches the high level, turn off the material pump.
capper
The main function of the capping machine is to use the closing punch to tightly close the aluminum ring caps that have not been compacted and tightened, and handle up to 6 barrel caps at a time. At the entrance of the capping machine, it is also necessary to separate barrels and block barrels. The barrel blocking, barrel separating and pressing of the capping machine are controlled by an independent PLC control system, while the barrel feeding and barrel discharging links are controlled by the main control cabinet. The PLC of the main control cabinet generates control signals to control the start and stop of the barrel feeding roller table, thus controlling the number of barrels fed into the capping machine, and coordinating the whole filling process.
electrical control system
Multi-station liquid filling machine is controlled by programmable controller (PLC) for the whole coordination of barrel positioning, roller running, weighing and filling, material in trough, etc. Man-machine interface is used for manual and automatic control, which saves a lot of buttons, switches and other devices on the panel and is convenient for operation. At the same time, there are many status displays on the touch screen, which is convenient for the operator to know the running status of the system. High-precision weighing module and high-stability weighing instrument are selected to control the filling process, which fully meets the accuracy and speed requirements of the system.
There are two control modes of filling system: manual and automatic. Manual operation can realize single filling, independent operation of roller table, lifting of spray gun and other actions. The automatic mode is to control the processes of dividing barrels, positioning, dragging barrels, periodic operation of roller table and filling of the system according to the prescribed procedures. Before the system starts, the specifications of the barrel can also be set, which is suitable for a variety of similar barrel-shaped filling.
Control method of main process
(A) the control of the bucket separator and the bucket setter
The front baffle and the rear baffle of the bucket separator and the bucket fixer cooperate with the chain conveyor to complete the function of bucket separation. Before the bucket separator is started, put a bucket between the front baffle and the rear baffle, and the distance between the two baffles is exactly the distance of a bucket (the distance between baffles can be adjusted to adapt to the change of bucket shape). The action of the baffle is controlled by a timer, and 12 barrels are released at a time. At the beginning, the two baffles are all extended, and the actions of the baffles during bucket separation are as follows: the front baffle is retracted, the delay T1 is delayed, and the rear baffle is retracted. Delay T2 again; The front baffle is extended, delayed by T3, and the rear baffle is extended. These four actions are repeated 12 times, and the separation of 12 barrels is completed. The spacing between the separated barrels is realized by adjusting the conveying speed and delay time of the chain plate.
The control of fixed barrel is also realized by timer. There are 12 barrel fixers, which are driven by cylinders respectively. The distance between the fixed bucket positions is consistent with the distance between the roller table pallets. When the first bucket separated by the bucket separator passes through the photoelectric switch, the timer 10 starts counting, and after the set time T10, the first bucket fixing cylinder extends to block and position the first bucket; When the second bucket passes through the photoelectric switch, the timer 11 starts counting, and the second bucket cylinder extends after the set time T11. Repeat this way to complete the positioning of 12 barrels. In practice, because of the fast running speed of the chain plate, 12 barrels move forward continuously, and the extension time of the barrel stopper needs to be accurately controlled. It takes many experiments to determine the accurate time of each timer.
The positioned 12 barrels are pushed to the barrel temporary storage area by the pusher when the filling process stops, so as to prepare for the pusher to drive the filling barrels to the filling position.
(2) Pallet and multi-barrel filling control
In order to ensure that the filling barrel is accurately delivered to the spray gun mouth, the stop position of the carriage must be accurately controlled. The speed control of the carriage is realized by the frequency converter. Setting the start and stop time of the frequency converter properly can make the carriage control more accurate and stable. We use the photoelectric switch to detect the position of the pallet for positioning, and use the photoelectric switch to detect the pulse leading edge of the pallet as a benchmark. When the last pallet arrives, we control the frequency converter to run slowly to stop the pallet at a more accurate position. After many tests, the maximum position error of the carriage is less than 5mm, which is usually about 2 mm.
In order to ensure that the spray gun can enter the barrel mouth reliably when it descends, the mechanical positioning device of the barrel mouth is installed at two positions of the filling position, and the positioning device of the barrel mouth is started before the spray gun descends, so as to ensure that the spray gun can enter the barrel smoothly.
The filling process is completed by PLC and weighing instrument, and one weighing instrument corresponds to one weighing platform. Before filling, the system automatically determines whether the tare weight value is within the set range. If it is less than the set tare weight value, the instrument will not be peeled and the filling process will not be started. This function can avoid the wrong filling situation due to the fact that the bucket is not in place.
(3) capping machine control
A group of barrels filled by the filling machine are sent to the conveyor chain plate, covered manually and grouped. That is, a photoelectric switch is installed in front of the capping machine, and when it is detected that six barrels pass, the operation of the conveyor chain plate will be automatically stopped to complete a grouping. The grouped barrels enter the chain plate of the capping machine in turn and continue to move forward. The capping machine consists of six stations, and each time it completes the capping action of six barrels. When the first barrel comes in, the barrel blocking device at the first station extends out to block the first barrel; And so on, a total of 6 barrels are blocked. Then, the six pressure heads simultaneously press and tighten to complete the capping action, and after time delay, the pressure heads rise to complete a capping cycle.
(4) Anti-congestion control
The core equipment of filling production line is filling machine and capping machine. It is responsible for accurate filling and capping after filling, and the transmission mechanism between them is an S-shaped conveyor chain with a length of about 5 m.
Board. The speed of this chain plate can be adjusted by frequency conversion according to the actual situation. In actual work, it is necessary to provide controlled (speed control and quantity control) barrel feeding operation for the barrel feeding link of the capping machine.
Due to the special position and function of the S-shaped conveyor chain plate, there is a security problem that cannot be ignored, that is, how to control the motion parameters of the S-shaped conveyor chain plate to ensure that the density of the barrel clusters above the chain plate is transmitted in an adaptive state, so as to effectively prevent the container from being squeezed due to the over-dense interval of the barrel clusters (squeezing will lead to the unbearable load of the barrel outlet chain of the filling machine when delivering barrels to the outside, which not only interferes with the normal filling process, but may damage the chain in serious cases). Therefore, it is necessary to strictly control the movement of the S-chain plate to ensure that the interval between barrels and clusters is within a reasonable range. In general, congestion is caused by the failure of the capping machine to send the barrel out of the capping machine in time.
There are two ways to judge the occurrence of congestion:
(1) Let the PLC generate a periodic square wave (the high-level time of the square wave is 7 seconds wider than the low-level time of 0.3 seconds), and take the high-level period of this square wave as the benchmark for investigation. Install a photoelectric switch near the capping machine on the S-shaped roller table. A pulse is generated when the bucket passes through the photoelectric switch. During the period of high level of periodic square wave, the duration of pulse is accumulated and the number of pulses is recorded. When the accumulated pulse duration exceeds the set value (determined by experiments) and the number of pulses is less than the predetermined value, it is judged as congestion.
(2) Comparing the number of barrels in and out before and after each operation of the capping machine, once the inconsistency is found, a congestion signal will be generated immediately.
The above two points act as OR logic, that is, the system will generate corresponding signals as soon as any situation occurs.
System disposal measures after congestion:
(1) the S-shaped roller table immediately stops conveying;
(2) At the end of the nearest filling cycle, the filling machine lifts the spray gun, and the subsequent actions are suspended without going down (only suspending actions, not terminating the working process of the filling machine), and the chain plate is dragged without running. After waiting for the congestion to be eliminated, artificially lift the suspended state, start dragging the chain plate, and continue the next filling cycle.
Concluding remarks
The stability and safety of automatic filling line and other equipment are important product attributes that cannot be ignored. In addition to using high-quality components and reliable equipment structure in hardware, it is also extremely important to improve the control method in software. In the software design of multi-station liquid filling line, we use anti-congestion algorithm, tare weight discrimination, inlet and outlet counting and other methods to effectively ensure the stable operation of the system. A considerable number of algorithms are rarely activated in the normal state of the system, but the startup of related algorithm content will play a key role in the operation safety of the whole system in the event of abnormal conditions (such as congestion in the transmission link and abnormal container in the filling position link). Security is the premise of stability, the basis of normal operation of the system and the core quality of products, and also a prerequisite. In the aspect of automation control, if we don't consider the problem thoroughly before making the foundation, any small details will probably cause safety problems or even personal injuries, which will directly affect the quality of the whole equipment. Therefore, how to avoid any hidden safety problems in the details is a basic skill that the designers of automation control link can't ignore.
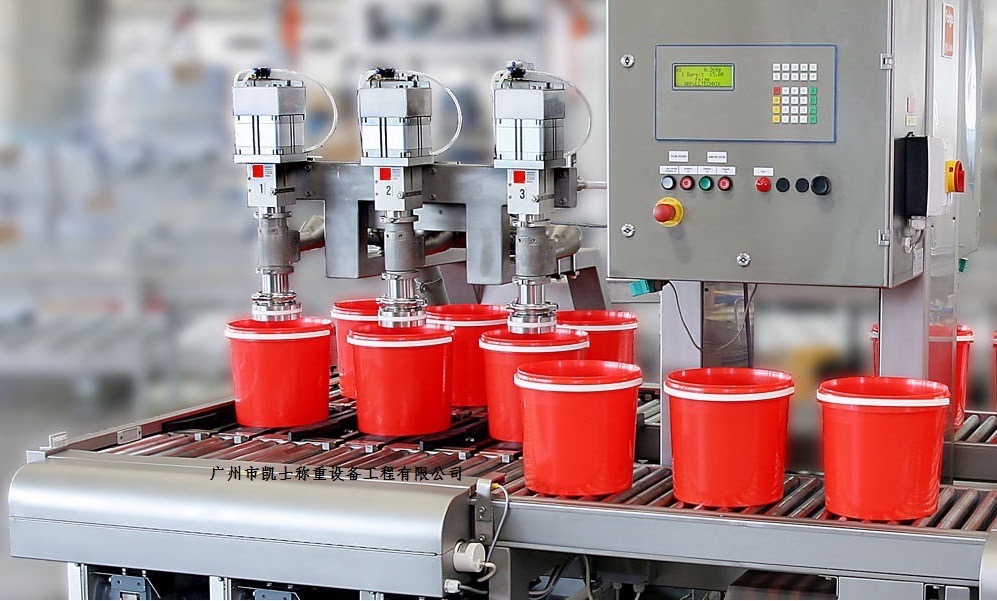
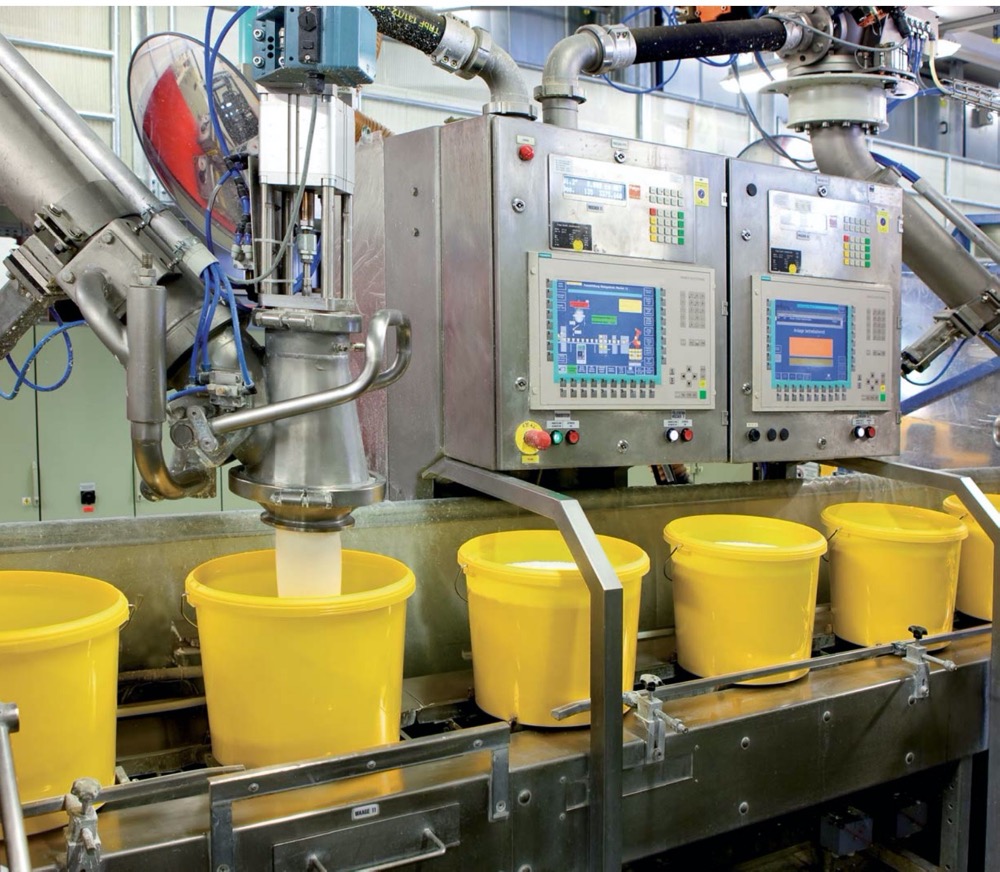
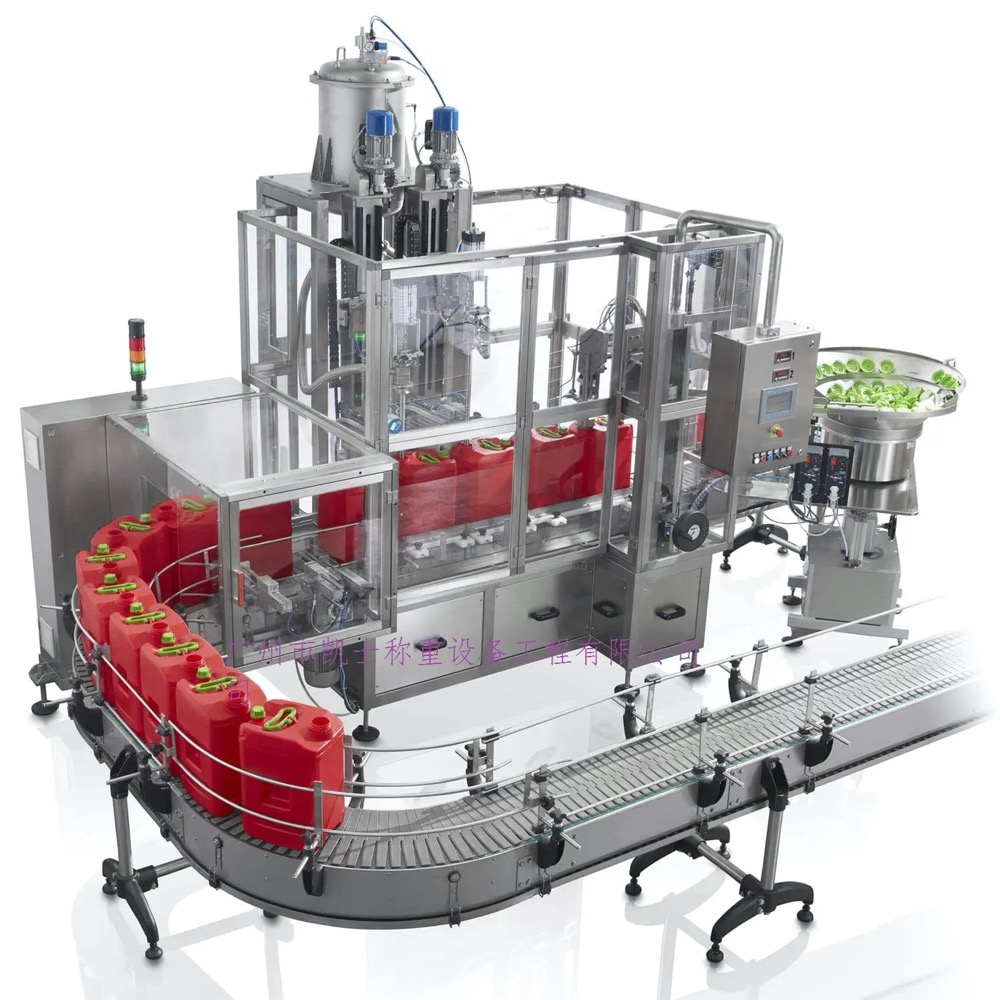
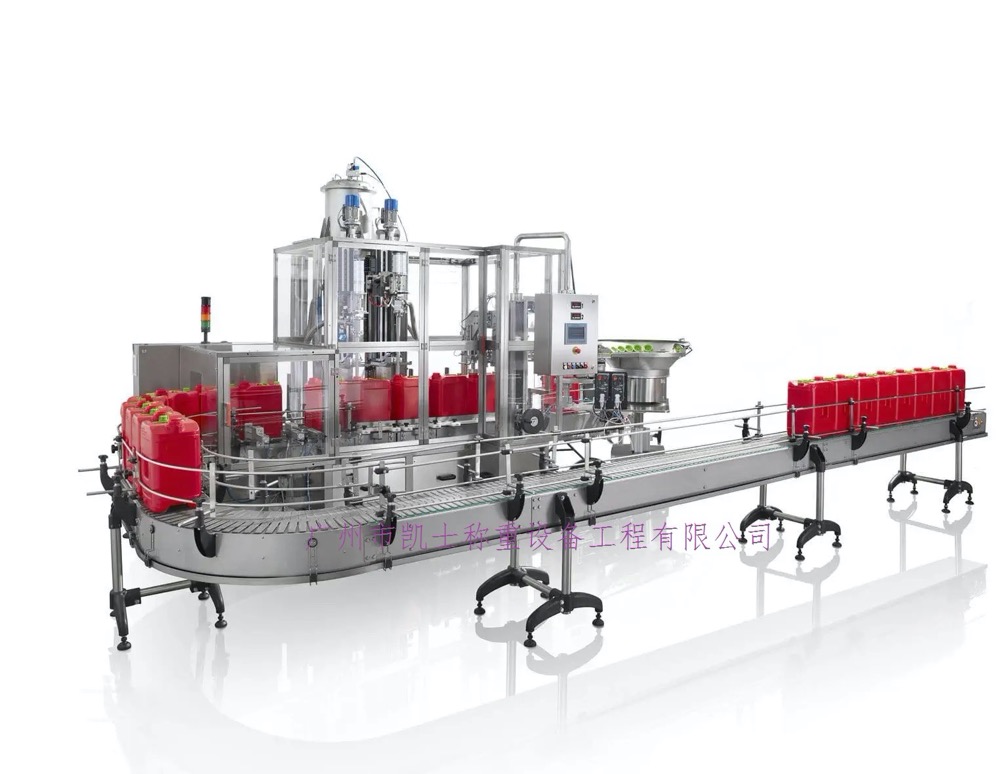