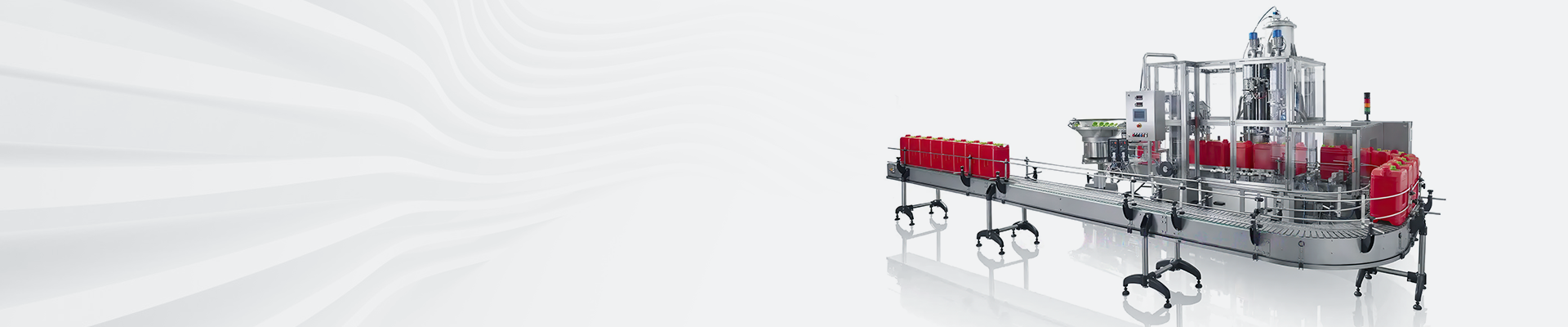
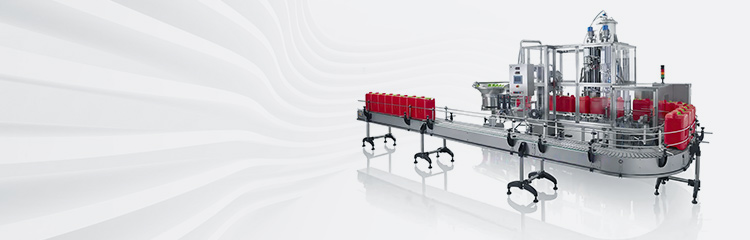

Summary:The liquid filling machine adopts Siemens S7-200CPU226cnDC/DC/DC PLC as the core control, and at the same time, extends EM235 analog module for weight acquisition, and the upper computer adopts integrated embedded TPC1061Ti touch screen to realize the functions of status display, set value input and operation process monitoring, etc. The upper computer adopts integrated embedded TPC1061Ti touch screen to realize the functions of status display, set value input and operation process monitoring.
Liquid filling machine according to JJG687-2008 "liquid material quantitative filling machine" verification procedures, automatic filling machine (fixed capacity and fixed-weight type) of the verification can be completed through the weighing method, using with a serial port (RS232) based on the VB platform compilation, its functions include data acquisition, data processing, generating documents, as well as data printing. In order to adapt to the needs of different specifications of the filling, the system has two ways of working automatically and manually: secondly, in the system can be manually set up the filling parameters. Parameter settings include: setting the weight of the filling container (i.e., tare weight), set the filling weight (i.e., net filling volume).
The weighing and filling machine adopts Siemens S7-200CPU226cnDC/DC/DC PLC as the core control, at the same time, it extends EM235 analog module for weight collection, and the upper computer adopts integrated embedded TPC1061Ti touch screen to realize the functions of status display, set value input and operation process monitoring.
The automatic filling machine mainly adopts the weighing and dosing method to realize the quantitative filling of liquid by collecting the data from the weighing module. Need to measure the amount of filling and real-time display, the filling system uses a weighing module and weighing instrument, set its range of 0 ~ 40kg, the output is a standard voltage signal 0 ~ 10V, through the EM235 analog input channel to achieve the measurement of the quality of the cans, the port of EM235 is set to 0.0010. In order to ensure the accuracy of filling, the system in the front of the pump to add a solenoid valve, to ensure that the start / stop the pump can immediately connect and cut off the liquid inflow, the pump selection parameters of 12V. Ensure that the start / stop can be immediately connected and cut off the inflow of liquid, the pump selection parameters for the 12VDC flow rate of 3.1L/min maximum pressure of 0.48MPa, using intermediate relays as a conversion to achieve the control of the solenoid valve, pump. In the manual/automatic switching is realized through the two-position selection button, followed by the start, manual filling is realized through the button.
I / 0 allocation of the filling system, the need for seven switching individual inputs, an analog input signal real-time collection of filling quality, two switching outputs to control the action of the pump and the solenoid valve, the PLC system has two modes of operation, the use of the main program to call the structure of the subroutine, to reduce the scanning time, the conversion of the measured value, the stop and emergency stops, such as extraneous reasoning. Upper machine using configuration software for monitoring interface design, the software can quickly component and generate the upper machine monitoring system, through the field data acquisition and processing, to animation display, alarm processing, process control. Real-time curve, historical curve and report output and other ways. Monitoring system through the screen real-time display of the current filling quality, filling the number of barrels and other field work status, in the host computer can carry out the corresponding operation, through the interface for the filling mode selection and start, stop and other buttons operation. It can change the filling quality, number of barrels and manually remove the tare weight (i.e. the quality of filled bottles) when using different filling barrels.
In order to realize the above monitoring requirements, the monitoring interface adopts Haniwa effect and fast flow attribute setting to simulate the dynamic filling process; by adding standard buttons to realize manual/automatic selection, start, stop, emergency stop and manual opening of pumps and solenoid valves; by setting the display and output attributes of labels to realize the real-time display of filling quality setting, the number of barrels to be filled, and the display of the number of barrels to be filled, etc., the configuration of the monitoring screen can monitor the operation status of the filling system. Monitoring the operation status of the filling system, realizing the purpose of monitoring the PLC operation through the operation of the touch screen, establishing the connection between the system and the external hardware equipment, enabling the MCGS to read the data from the external equipment and controlling the working status of the external equipment, and realizing the real-time monitoring of the filling process. Configure the device components in the device window to be S7-200 as the monitored device components, set "Universal Serial Parent Device 0" to be "Universal Serial Device" and "Sub Device 0" to be "Siemens S7200PPI"; secondly, it is necessary to connect the graphic objects in the operation screen and the programming software in the PLC, which can be done by defining the real-time database in the MCGS and then connecting to the real-time data base through the channel connection in the device window. This can be done by defining the real-time database in the MCGS, and then through the channel connection in the device window, providing the real-time database with the channel connection of the data variables collected from the external devices.