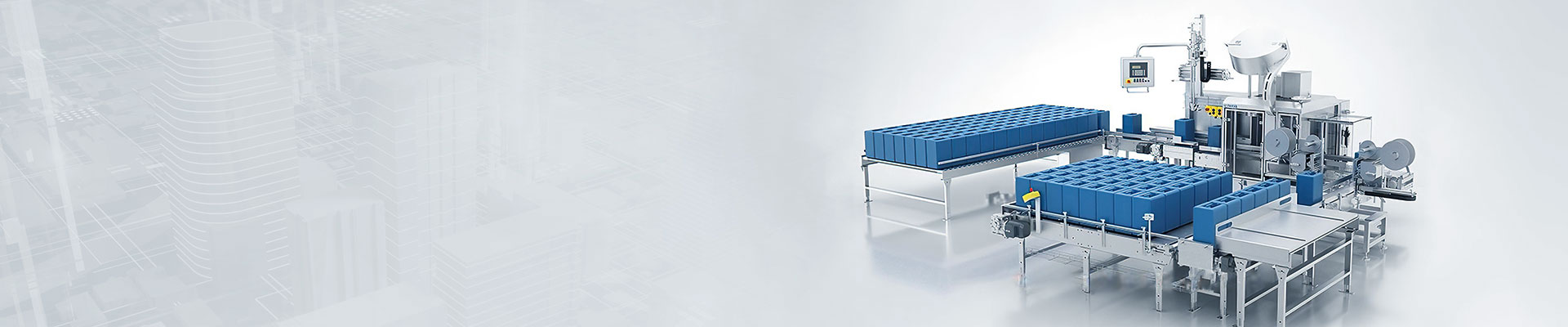
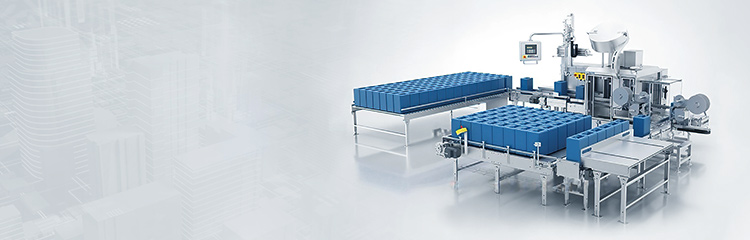
Liquid filling machine to send information to the weighing system through the serial port to read the weighing data after the weighing system in receiving such information, will be through the RS232 serial port to the microcontroller's serial port to send the data, automatic filling machine (fixed capacity and fixed weight type) of the verification can be completed through the weighing method, the use of the with a serial port (RS232) based on the VB platform to prepare, its functions include data acquisition, data processing, The functions include data acquisition, data processing, file generation, and data printing.

Automatic Filling machine has two working modes: automatic driving and manual driving. Through the computer interface to switch between manual and automatic switch to switch, generally use the automatic state to let the PLC automatically track and set parameters for automatic control, when the equipment needs maintenance, debugging or special circumstances can be used to manually drive a single device start, stop. Generally used through the pump to add directly to the filling method, not good for filling the amount of real-time control, but also can not automatically record the amount of real-time addition, so the consumption of solvents, solutions, waste is relatively large, the filling ratio is not accurate; another method of controlling the speed of the pump motor through the frequency converter to add the amount of filling required to give the process, the method of control is not highly accurate, the response time is slow, and can not be realized automatically. Closed-loop control and meet the control requirements.
Liquid filling machine is mainly composed of four parts: transfer device, filling device, suction and sealing device and detection and sensing device. Transmission device consists of conveyor belt, transmission gear, conveyor belt, conveyor motor and lifting cylinder; filling device consists of filling gun, filling barrel, synchronous motor, rodless cylinder and roller arm; suction capping device consists of suction capping device; detection and sensing device consists of photoelectric sensors, proximity switches and weighing sensors.
Liquid filling machine each sensor signal to carry out directly into the corresponding weighing controller, through the serial port or Modbus protocol weighing controller will be the weight of the signal transmission to the computer, the computer according to the automatic filling machine weighing control of each raw material silo dosage of the final control valve, add the required weight of raw materials.
Programmable controller or intelligent input/output module mainly learns the raw material warehouse and dosage valve status and sends the control switch all the warehouse door signals industrial computer is the core of the automatic filling machine, mainly in the completion of a variety of formulas and raw material management; control of raw materials to add the order of addition; add the amount of and in the automatic filling machine process data management and analysis.
Basic parameters:
Maximum weighing capacity: 60kg
Minimum Sensitivity: 0.01kg
Filling error: ±0.01-0.02kg
Filling speed: 60L about 500-800 barrels/hour
Control mode: 2-speed control
Filling method: insertion type, liquid level up
Gun head line: Teflon gun head, valve + Teflon hose
Structure material: host SUS304 stainless steel, conveying palletizing carbon steel anticorrosion paint.
Weighing platform size: 500 × 500mm (304 stainless steel power raceway)
Empty barrel raceway: 500mm × 2500mm (304 stainless steel power raceway) with another 1200mm slope without power roller
Heavy drum raceway: 500mm×2500mm (304 stainless steel power raceway, 2 sets)
Separate barrel device: for 60L barrels, carbon steel anti-corrosion paint structure, 304 stainless steel raceway.
Palletizing equipment: pan-transfer type, suitable for pallets 1200×1200×140mm, including supplying pallets, palletizing, and lower pallet conveying.
Pipe pressure: 0.2-0.6MPa (related to material properties).
Material interface: DN40 flange connector 4, according to the user to provide interface standards
Air Connection: User supplied 12mm air hose connector for quick coupling connection
Power supply: AC220/50Hz (user-supplied to one side of the machine)
Using air source: 0.4-0.8Mpa (provided by the user to the side of the machine)
Use temperature: -10℃-50℃
Base conditions: solid concrete floor of the assistant suspension agent flat, concrete thickness should be more than 10cm.
Optional models: standard, explosion-proof filling
Head piping: SUS304 stainless steel and PTFE (316L optional)
Material interface: DN40 quick-fit pagoda connector, optional flange connector.
Air supply interface: 8mm air tube access